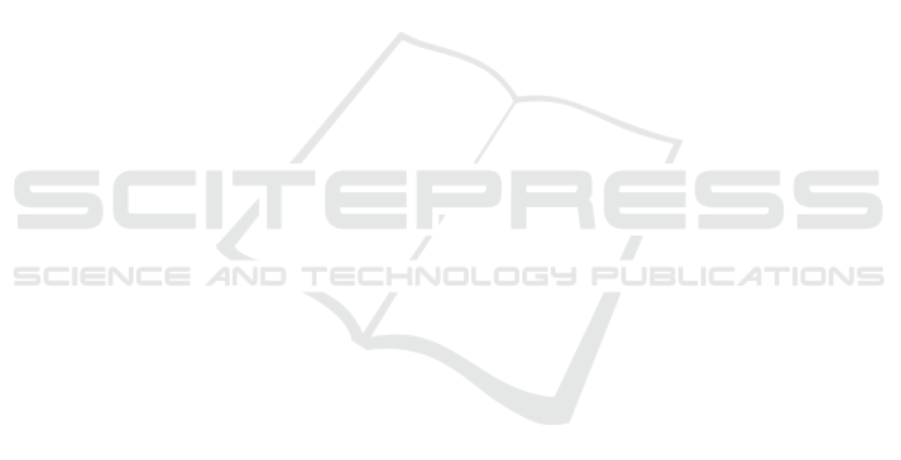
with the technical safety concept, we defined a novel
methodology to derive further requirements and in-
puts from the functional SR in coherence with the
early system design (preAA). Using the syntax for
safety requirements we are able to generate UVM ver-
ification components and whole testbenches from the
definition of the functional SR and their constraints.
For each constraint of the functional SR, a new UVM
validator is added on the ports or one end of the sig-
nal. A validator consists of a configurable comparator
with the pin/port/signal attached to one input and a
reference signal or constant value attached to the sec-
ond input. The output of the comparator can be either
1 (true) or 0 (zero) and are connected via arithmetic
or algebraic function blocks to create the boolean op-
erations. In addition we use non safety requirements
in the SysML specification to provide stimuli blocks
for relevant operating modes and driving maneuvers.
Depending on the non safety requirements and con-
straints and if the pin/port/signal is an unused input of
a block the testbench generator creates a stimuli block
and attaches it. This block generates either values
that are within the specifications in order to validate
proper operation or to generate invalid stimuli to ver-
ify safety mechanisms within the model. To vary the
parameters and stimuli of our system and to cover up
corner cases we use the benefits of Coverage-Driven
Verification (CDV), with its aim to detach from di-
rect - user depended - testing (Accellera, 2015). This
methodology provides the definition of so called ver-
ification goals, which can be verified by smart test
scenarios. The intelligence is mainly achieved by
creating simulation configurations (stimuli), with re-
spect to some predefined constraints. This concept
is widely known as Constraint Random Verification
(CRV) (Kitchen and Kuehlmann, 2007). CRV mainly
consists of two core concepts, which is on one hand
the usage of Markov-chain Monte Carlo to guarantee
coverage through probability and on the other hand
the processing of constraints with SAT solvers. As
described above, it is important to vary parameters
such that many different input combinations can be
covered. The defined internal values of the DUT vary
according to a predefined probability distribution. In
this case we use Gaussian distribution with the defini-
tion of a value of 3 sigma.
5 FUTURE WORK
To show the efficiency, this novel method will be
applied on a complex battery management system
example from the automotive industry. We will
show how the tesbenches are automatically gener-
ated from our defined requirements and constraint
in UML/MARTE. This testbenches will be automat-
ically connected to the design under test. Further-
more, SysML models will be used to define more pre-
cisely our stimuli inputs. In addition we will build
our methodology into the Eclipse Papyrus environ-
ment, so every UML editor will be able to simulate
UML/MARTE models by installing our plugin. This
tool will also be published for download and also be
used for educational purposes.
ACKNOWLEDGMENTS
The approach presented above is an experiment un-
dertaken in the framework of OpenES CATRENE
Project: CA703 - 2013 research program supported
by the FFG (Austrian Research Promotion Agency),
project-number 843380 in tight cooperation with
CISC Semiconductor.
REFERENCES
Accellera (2015). Universal Verification Methodology
(UVM) 1.2 User’s Guide. Technical report, Accellera.
Catrene (2016). OpenES CATRENE Project: CA703.
ETAS (2014). ETAS Embedded Systems Consulting: Elec-
tronic Control Unit ( ECU ) - Webinar Basics of Au-
tomotive ECU. pages 1–30.
ISO (2011). Functional Safety ISO26262 - Part 4: Product
development at the system level. 2011:1–35.
Kim, H., Wong, W. E., Debroy, V., and Bae, D. (2010).
Bridging the Gap between Fault Trees and UML State
Machine Diagrams for Safety Analysis. 2010 Asia
Pacific Software Engineering Conference, pages 196–
205.
Kirchsteiger, C. M., Grinschgl, J., Trummer, C., Steger, C.,
Weiß, R., and Pistauer, M. (2008). Automatic test gen-
eration from semi-formal specifications for functional
verification of system-on-chip designs. 2008 IEEE In-
ternational Systems Conference Proceedings, SysCon
2008, pages 421–428.
Kitchen, N. and Kuehlmann, A. (2007). Stimulus Genera-
tion for Constrained Random Simulation. In Proceed-
ings of the 2007 IEEE/ACM International Conference
on Computer- aided Design, pages 258–265, Piscat-
away, NJ, USA.
Mader, R., Armengaud, E., Leitner, A., Kreiner, C.,
Bourrouilh, Q., Grießnig, G., Steger, C., and Weiß,
R. (2011). Computer Safety, Reliability, and Se-
curity: 30th International Conference,SAFECOMP
2011, Naples, Italy, September 19-22, 2011. Proceed-
ings. chapter Computer-A, pages 113–127. Springer
Berlin Heidelberg, Berlin, Heidelberg.
Mhenni, F. and Nguyen, N. (2014). Automatic Fault
Tree Generation From SysML System Models. 2014
PEC 2016 - International Conference on Pervasive and Embedded Computing
74