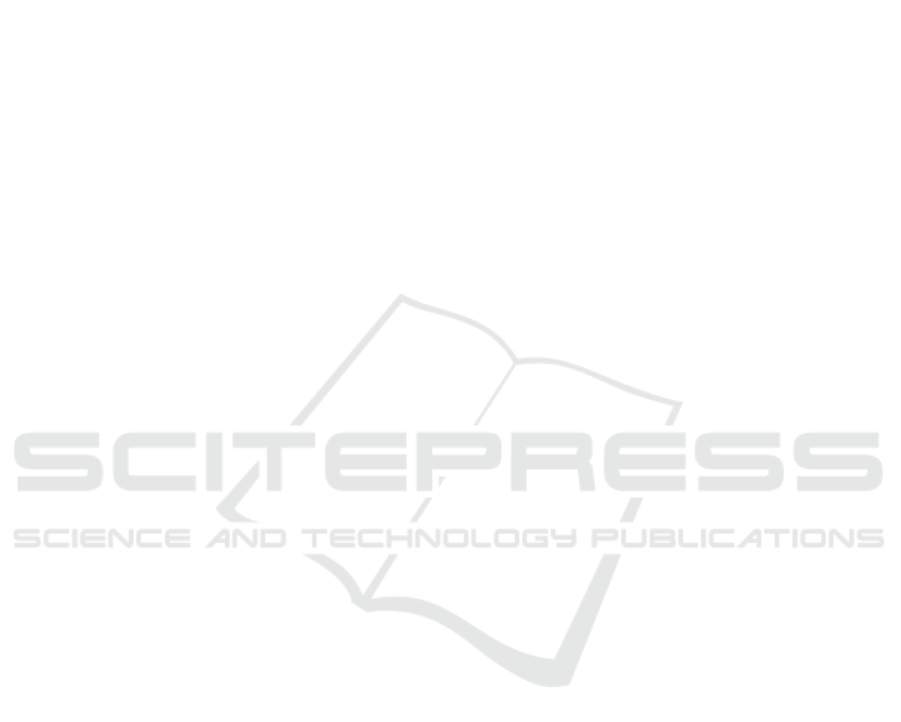
A Hybrid Visualization of the Environment using Smart
Ultrasound-based Sensor Arrays
Emir Sokic, Kenan Softic, Mina Ferizbegovic, Jasmina Zubaca and Melita Ahic-Djokic
Faculty of Electrical Engineering, Sarajevo, Bosnia and Herzegovina
Keywords:
Sensory System, Environment Analysis, Distributed System, Ultrasound, Laser, Sensor, Robotics.
Abstract:
This paper presents the work in progress on the design and testing of a distributed ultrasound-based sensory
system for hybrid 1D and 2D environment visualisation. Many common sensors used in robotics, such as
infrared and ultrasonic sensors, cameras and lasers mainly focus on quantifying distances and shapes, while
rarely have the ability to differentiate among different sensed surfaces/materials. We propose an inexpensive
prototype sensory system based on popular ultrasonic sensors which uses ultrasonic reflections to determine
the acoustic reflection coefficients. This additional feature allows differentiating among sensed objects. More-
over, the developed ultrasonic cells are equipped with a microcontroller for basic signal processing and a
communication link for integration into a sensor network. In this paper, we discuss the possibility of fusing
obtained sensor array data and laser measurements.
1 INTRODUCTION
Probably the most important part of an autonomous
robotic system is a precise and reliable sensing el-
ement. Without sensors, it is extremely difficult
to achieve any type of motion control. Techniques
such as SLAM (simultaneous localization and map-
ping problem) rely on information provided by sen-
sors (Fuentes-Pacheco et al., 2015). Analysis of
the robotic system surroundings is very important
in different areas: industrial robotics (Kaltsoukalas
et al., 2015), medical surgery, space exploration
(Elfes et al., 2006), and autonomous navigation of
unmanned underwater, ground, or air vehicle, just to
name a few.
Different types of sensors are used for environ-
ment analysis: infrared and ultrasonic sensors, (ther-
mal) cameras, lasers etc. Different sensors have dif-
ferent disadvantages: optical sensors are sensitive to
environmental conditions (such as light, rain, fog,
etc.) (Benet et al., 2002), lasers are power-demanding
(Jung et al., 2008) and expensive, RGB cameras can-
not provide information about distance of nearby ob-
jects or object structure on their own (Fern
´
andez et al.,
2007).
In contrast, ultrasonic sensors are cheap, rela-
tively accurate and reliable. These sensors, which are
widely used in robotic systems, flow measurements
(Han et al., 2011), fault detection (D. Champaigne,
2007) and process monitoring (Kim et al., 2011) are
able to assess the structure and solidity of materials
(Grzelak et al., 2014).
Common low-cost solutions, such as the popular
HC-SR04, are ultrasonic sensors primarily developed
for distance measurements. In our previous work
(Zubaca et al., 2015) we have described the design
of an ultrasonic cell which is able to measure the dis-
tance and additionally measure the magnitude of the
reflected ultrasonic wave and differentiate among dif-
ferent materials. In this paper we will briefly present
the ultrasonic cell, while more information may be
found in (Zubaca et al., 2015).
A single ultrasonic cell may be used as a stan-
dalone sensing element. However, using multiple spa-
tially distributed sensors may enrich the information
on the observed environment. Therefore, we pro-
posed and developed a sensor array/network. The
ultrasonic cells communicate on two different buses:
SPI bus used for automatic remote (re)programming
of the cells, and RS485 bus for communication. The
buses are controlled by a master device, which acts
as the in-between element that processes communi-
cation between slave ultrasonic cells and master PC
computer.
One of the final goals of this project is to create
a hybrid multidimensional sensing platform, as illus-
trated in Figure 1. Combining ultrasonic readings
with other sensors (e.g. RGB camera) enables ac-
Sokic, E., Softic, K., Ferizbegovic, M., Zubaca, J. and Ahic-Djokic, M.
A Hybrid Visualization of the Environment using Smart Ultrasound-based Sensor Arrays.
DOI: 10.5220/0006008705730578
In Proceedings of the 13th International Conference on Informatics in Control, Automation and Robotics (ICINCO 2016) - Volume 1, pages 573-578
ISBN: 978-989-758-198-4
Copyright
c
2016 by SCITEPRESS – Science and Technology Publications, Lda. All rights reserved
573