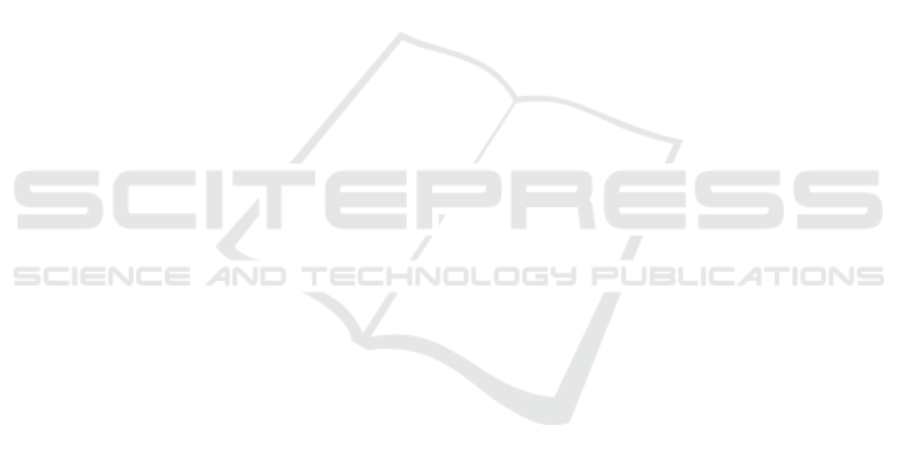
REFERENCES
˚
Akerberg, J., Gidlund, M., and Bj
¨
orkman, M. (2011). Fu-
ture research challenges in wireless sensor and actu-
ator networks targeting industrial automation. In In-
dustrial Informatics (INDIN), pages 410–415. IEEE.
Barrenetxea, G., Ingelrest, F., Schaefer, G., Vetterli, M.,
Couach, O., and Parlange, M. (2008). Sensorscope:
Out-of-the-box environmental monitoring. In Infor-
mation Processing in Sensor Networks (IPSN’08),
pages 332–343. IEEE.
Bertrand-Krajewski, J.-L., Bardin, J.-P., Mourad, M., and
Beranger, Y. (2003). Accounting for sensor calibra-
tion, concentration heterogeneity, measurement and
sampling uncertainties in monitoring urban drainage
systems. Water Science & Technology, 47:95–102.
Boulis, A. (2007). Castalia: revealing pitfalls in design-
ing distributed algorithms in wsn. In 5th International
Conference on Embedded networked sensor systems,
pages 407–408. ACM.
Braga, R., Rossetti, R., Reis, L. P., and Oliveira, E. C.
(2008). Applying multi-agent systems to simulate dy-
namic control in flexible manufacturing scenarios. In
Cybernetics and Systems 2008, pages 488–493, Vi-
enna. OSGK.
Branisavljevi
´
c, N., Kapelan, Z., and Prodanovi
´
c, D. (2011).
Improved real-time data anomaly detection using con-
text classification. Journal of Hydroinformatics,
13(3):307–323.
Cao, X., Chen, J., Xiao, Y., and Sun, Y. (2008). Distributed
collaborative control using wireless sensor and actu-
ator networks. In Future Generation Communication
and Networking (FGCN’08), pages 3–6. IEEE.
Chen, J., Li, H., Sheng, D., and Li, W. (2015). A hy-
brid data-driven modeling method on sensor condi-
tion monitoring and fault diagnosis for power plants.
International Journal of Electrical Power & Energy
Systems, 71:274–284.
Dai, X., Long, Z., Yang, B., and Tan, X. (2011). Robust
fault detection observer in wireless networked control
systems. In Chinese Control and Decision Conference
(CCDC), pages 2147–2152. IEEE.
Dwivedi, A., Patle, V., and Vyas, O. (2010). Investigation
on effectiveness of simulation results for wireless sen-
sor networks. Information Processing and Manage-
ment, pages 202–208.
Eriksson, J. (2009). Detailed simulation of heterogeneous
wireless sensor networks. Licentiate thesis, Uppsala
University, Sweden.
Freitas, T. R., Coelho, A., and Rossetti, R. (2010). Correct-
ing routing information through GPS data processing.
In Intelligent Transportation Systems (ITSC), pages
706–711. IEEE.
Liu, S., Araujo, M., Brunskill, E., Rossetti, R., Barros,
J., and Krishnan, R. (2013). Understanding sequen-
tial decisions via inverse reinforcement learning. In
Mobile Data Management (MDM), pages 177–186.
IEEE.
Neumann, P. (2007). Communication in industrial automa-
tionwhat is going on? Control Engineering Practice,
15(11):1332–1347.
Passos, L. S., Rossetti, R., and Gabriel, J. (2011). An agent
methodology for processes, the environment, and ser-
vices. In Intelligent Transportation Systems (ITSC),
pages 2124–2129. IEEE.
Ramamurthy, H., Prabhu, B., Gadh, R., and Madni, A. M.
(2007). Wireless industrial monitoring and control us-
ing a smart sensor platform. Sensors Journal, IEEE,
7(5):611–618.
Ramanathan, N., Balzano, L., Burt, M., Estrin, D., Harmon,
T., Harvey, C., Jay, J., Kohler, E., Rothenberg, S., and
Srivastava, M. (2006). Rapid deployment with confi-
dence: Calibration and fault detection in environmen-
tal sensor networks. Center for Embedded Network
Sensing.
Ravichandran, J. and Arulappan, A. I. (2013). Data valida-
tion algorithm for wireless sensor networks. Interna-
tional Journal of Distributed Sensor Networks, 2013.
Rossetti, R., Oliveira, E. C., and Bazzan, A. (2007). To-
wards a specification of a framework for sustainable
transportation analysis. In 13th Portuguese Confer-
ence on Artificial Intelligence, EPIA, Guimar
˜
aes, Por-
tugal, pages 179–190. APPIA.
Sharma, A. B., Golubchik, L., and Govindan, R. (2010).
Sensor faults: Detection methods and prevalence in
real-world datasets. ACM Transactions on Sensor Net-
works (TOSN), 6(3):23.
Song, C.-C., Feng, C.-F., Wang, C.-H., and Liaw, D.-C.
(2011). Simulation and experimental analysis of a
zigbee sensor network with fault detection and recon-
figuration mechanism. In Asian Control Conference
(ASCC), pages 659–664. IEEE.
Szczodrak, M., Zahedi, S., Ji, P., Mylaraswamy, D., Sri-
vastava, M., and Young, R. (2008). Simulation frame-
work for qoi characterization of sensor networks in the
presence of faults.
Szewczyk, R., Mainwaring, A., Polastre, J., Anderson, J.,
and Culler, D. (2004). An analysis of a large scale
habitat monitoring application. In 2nd International
Conference on Embedded networked sensor systems,
pages 214–226. ACM.
Tolle, G., Polastre, J., Szewczyk, R., Culler, D., Turner,
N., Tu, K., Burgess, S., Dawson, T., Buonadonna,
P., Gay, D., et al. (2005). A macroscope in the red-
woods. In 3rd International Conference on Embedded
networked sensor systems, pages 51–63. ACM.
Vasconcelos, G., Petry, M., Almeida, J. E., Rossetti, R., and
Coelho, A. L. (2012). Using UWB for human tra-
jectory extraction. In 24th European Modeling and
Simulation Symposium, EMSS, pages 428–433.
Zhang, C., Ren, J., Gao, C., Yan, Z., and Li, L. (2009). Sen-
sor fault detection in wireless sensor networks. In IET
International Communication Conference on Wireless
Mobile and Computing, pages 66–69.
SIMULTECH 2016 - 6th International Conference on Simulation and Modeling Methodologies, Technologies and Applications
338