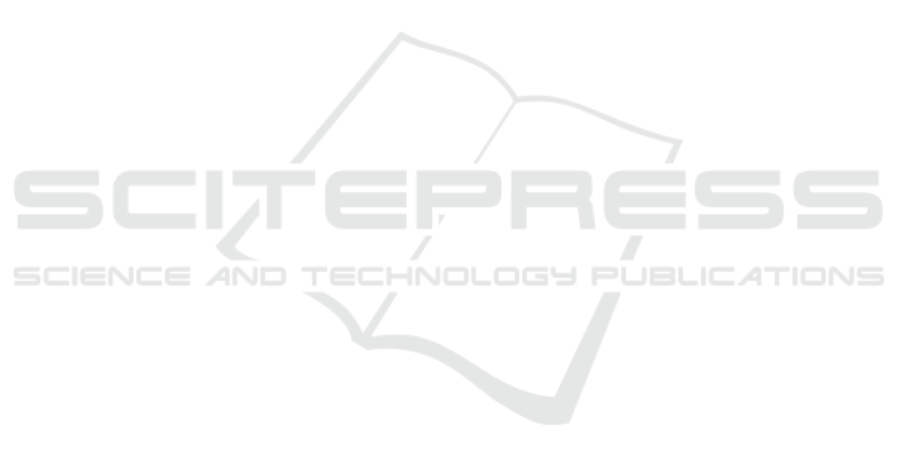
• Developing a modelling and simulation tool for
identifying risks, quantifying them and deciding
on how to mitigate them. This technical part of
the work relies on a Discrete Event Simulation
(DES) engine provided by the OscaR library (Os-
caR, 2012) and combined with Monte Carlo Sim-
ulation (MCS) techniques. It is fully described
and benchmarked in (Landtsheer et al., 2016).
• Building a user-friendly interface to support the
global risk management workflow depicted in
Figure 1. This is the scope of the present paper.
• Validating our work through a group of companies
that are already trying out the tool.
Our modelling framework includes concepts such as
storages and several types of production processes.
In addition, we defined a query language on models.
It is fully declarative and includes arithmetic, tempo-
ral, and logic operators, as well as basic queries on
the elements of our factory model (contents of a stor-
age, running state of a process, etc). Based on this
query language, the software tool is able to estimate
the probabilities of different scenarios (e.g. delay in
deliveries, defective parts or poor quality) and their
impact.
In this paper, we show how the modelling con-
cepts and simulation tool are supporting the global
risk management process in an efficient, consistent
and user-friendly way using a web-based interface.
The main steps of the process support are as follows:
• Risk-oriented process modelling: the model is
built with the aim to express the required risks and
not especially to be a full scale model. As risks are
fully identified in the next step, it may need to be
refined to reach the right granularity.
• Risk identification: in this key step, a hierarchi-
cal risk model is defined using a structured wiz-
ard covering major risk categories such as qual-
ity, quantity and delay risks. Different queries are
used to express the risks for each category.
• Risk-oriented simulation: the model instrumented
with queries is run using the DES and MCS, and
raw results (collected traces or statistics) can be
explored directly in the tool.
• Risk analysis and measures: the measurements
collected using the risk queries are presented in
a risk dashboard according to the structured risk
model. It allows the risk analyst to zoom in spe-
cific risk categories or look at the behaviour of
specific element according to specific risk cate-
gories. Based on this, some risk control measures
can be identified and validated using a new round
of simulation. The best value of specific parame-
ters can also be determined, e.g. the threshold or
the quantity for an order policy.
The paper is structured as follows. Section 2 gives
some background on our framework. Section 3 de-
scribes a short case study consistently used in the next
sections. Section 4 to 7 describe our modelling, risk
identification, simulation and analysis steps, respec-
tively. Finally, section 8 draws some conclusions and
describes some future work.
2 BACKGROUND: SIMQRI
SIMULATION META-MODEL
All the main elements of manufacturing processes are
represented in our simulation meta-model, which al-
lows us to define concrete models that are simulated
in a DES engine. In addition to this, we designed a
Query Language over concrete simulations in order
to collect and analyse data.
2.1 Meta-model Overview
This section introduces the basic blocks for represent-
ing factories. Figure 2 summarises the meta-model of
concepts used at that purpose. It is composed of ac-
tivatable components such as storages and processes
through which items can flow.
• Storages represent any kind of storage device or
place for raw materials, like a warehouse, a barrel
or a silo. They have a maximum capacity. When
this capacity is reached, they either overflow, or
processes trying to put more items into them are
blocked, depending on the settings of the storage.
If a full storage overflows, any exceeding material
is lost.
• Batch processes are factory processes that work in
a batch fashion; supplies are collected from vari-
ous storages, the process then runs for some time,
and finally the produced outputs are dispatched to
their respective storages before this whole cycle
starts again. They exist in different flavours: with
a single or multiple production lines.
• Splitting processes are similar to batch processes,
except that they have several sets of outputs that
can be selected according to some rules. It can be
used to model failing processes and quality assur-
ance process.
• Continuous processes are factory processes that
typically run on a conveyor belt. Items are contin-
uously picked from input stocks and undergo the
process taking some time. Continuous processes
SIMULTECH 2016 - 6th International Conference on Simulation and Modeling Methodologies, Technologies and Applications
340