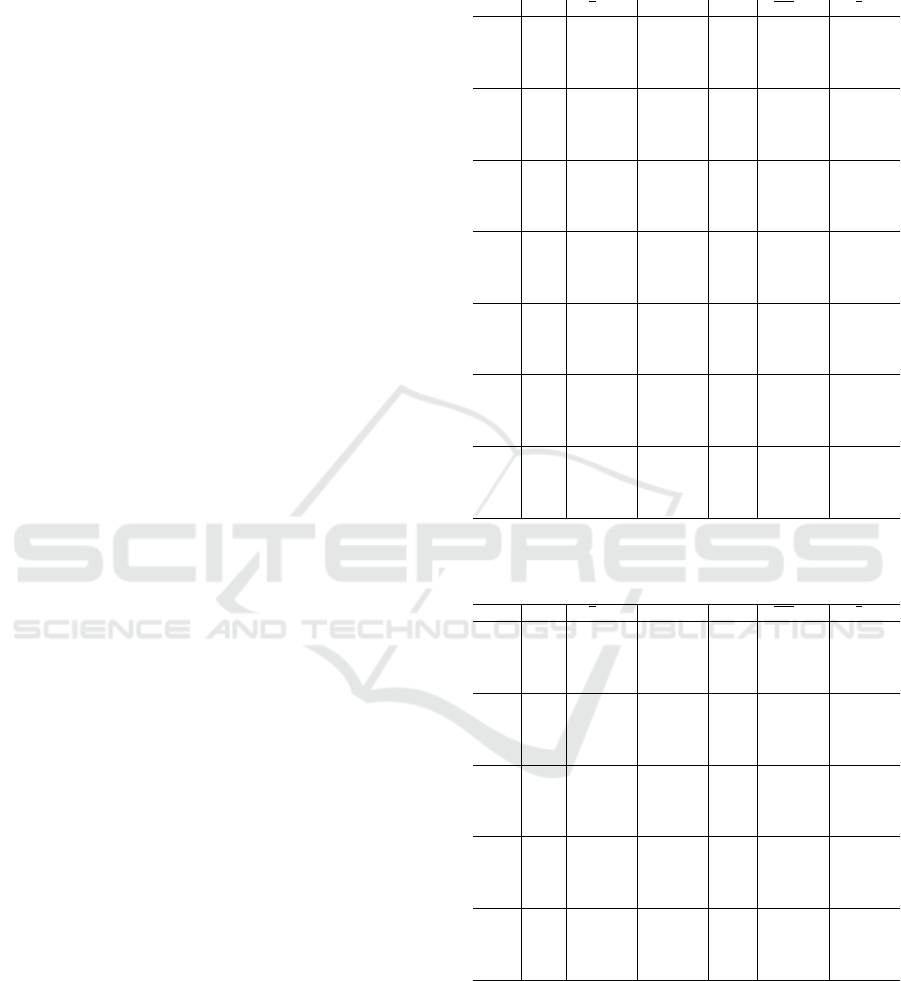
the ground truth distance and area as shown in Fig. 7
d), f) and h). Then, we applied the four measurement
methods again. The results are shown in in group 5
and 6 of Tab. 1 and group 3 and 4 of Tab. 2. The
support line and the support plane methods are overall
more suitable and give better results, or perform at
least on par.
5.3 Pilot Study
We asked a group of eight novice users and one expert
user to perform all different methods on the task of
measuring the distance of the upper two corners of
an outdoor window and the area of the window, in
analogy to the experiment described above. All users
were introduced to the system, and all measurements
with all methods were repeated three times.
Even for novice users with a short introduction to the
system, the results for the support line and support
plane method clearly outperform the standard method
and the support point method, as indicated by the re-
sults listed at the bottom of Tab. 1 and Tab. 2 respec-
tively.
The results in terms of the accuracy of the individual
methods for the distance and the area measurements
is depicted in Fig. 8. The line and the support plane
method consistently and considerably outperform the
standard and support point method, and, more impor-
tantly, all measurements have a considerably smaller
variation.
The users were asked to complete a short question-
aire about the overall usability and the intuitiveness
of the GUI and the overall approaches. The questions
and the answers given by the users are summed in
Tab 3. At a glance, users mainly voted for the support
line and support plane method to be favorable over
the standard and the support point method in terms of
ease of use. Being asked about the usefulness of the
three methods introduced in this work, users tended to
favor the support line and the support plane method
over the support line method. Concerning the accu-
racy and rapidness of the measurements, users pre-
ferred the plane support and the line support method,
respectively.
6 DISCUSSION AND
CONCLUSION
In this work, we have described different methods for
indirect measurements using a total station. Based on
the results of the experiments conducted, our methods
consistently outperform the standard method, even
when applied by novice users. One reason for the
Table 1: Distance measurements for experiments and meth-
ods: ground truth (r), direct targeting (a), support point (b),
support line (c), support plane (d).
Record Meth. d [m]
ˆ
σ
d
[m] N d
re f
[m] ∆d [m]
lab.
90
◦
(r) 600.191e-3 82.942e-6 4.000 600.191e-3 0
(a) 586.664e-3 273.151e-6 4.000 600.191e-3 13.527e-3
(b) 599.712e-3 39.655e-6 3.000 600.191e-3 478.897e-6
(c) 599.803e-3 866.189e-6 5.000 600.191e-3 387.538e-6
(d) 604.457e-3 3.636e-3 5.000 600.191e-3 4.266e-3
lab.
45
◦
(r) 600.191e-3 82.942e-6 4.000 600.191e-3 0
(a) 582.446e-3 1.192e-3 5.000 600.191e-3 17.745e-3
(b) 584.189e-3 240.581e-6 4.000 600.191e-3 16.002e-3
(c) 598.194e-3 229.861e-6 3.000 600.191e-3 1.997e-3
(d) 598.545e-3 654.487e-6 5.000 600.191e-3 1.646e-3
indoor
90
◦
(r) 881.992e-3 362.719e-6 10.000 881.992e-3 0
(a) 893.240e-3 820.525e-6 8.000 881.992e-3 11.248e-3
(b) 886.912e-3 1.921e-3 10.000 881.992e-3 4.920e-3
(c) 887.088e-3 830.455e-6 10.000 881.992e-3 5.096e-3
(d) 885.561e-3 957.555e-6 9.000 881.992e-3 3.569e-3
indoor
45
◦
(r) 881.702e-3 221.990e-6 5.000 881.702e-3 0
(a) 897.636e-3 3.285e-3 5.000 881.702e-3 15.934e-3
(b) 894.017e-3 2.142e-3 5.000 881.702e-3 12.314e-3
(c) 882.071e-3 607.033e-6 5.000 881.702e-3 369.144e-6
(d) 882.079e-3 1.165e-3 5.000 881.702e-3 377.119e-6
outdoor
90
◦
(r) 566.360e-3 20.239e-6 4.000 566.360e-3 0
(a) 576.559e-3 351.065e-6 4.000 566.360e-3 10.199e-3
(b) 565.040e-3 1.615e-3 5.000 566.360e-3 1.320e-3
(c) 564.474e-3 32.128e-6 3.000 566.360e-3 1.886e-3
(d) 564.664e-3 200.672e-6 4.000 566.360e-3 1.696e-3
outdoor
45
◦
(r) 2.192 107.789e-6 10.000 2.192 0
(a) 2.196 1.182e-3 10.000 2.192 4.463e-3
(b) 2.193 1.248e-3 10.000 2.192 1.761e-3
(c) 2.189 819.832e-6 10.000 2.192 2.303e-3
(d) 2.190 1.212e-3 10.000 2.192 1.587e-3
pilot
study
(r) 2.192 107.789e-6 10.000 2.192 0
(a) 2.214 14.497e-3 53.000 2.192 22.456e-3
(b) 2.218 21.181e-3 53.000 2.192 26.853e-3
(c) 2.188 4.148e-3 54.000 2.192 3.529e-3
(d) 2.188 4.740e-3 54.000 2.192 3.406e-3
Table 2: Area measurements for different experiments and
methods: ground truth (r), direct targeting (a), support point
(b), support line (c), support plane (d).
Record Meth. d [m]
ˆ
σ
d
[m] N d
re f
[m] ∆d [m]
indoor
90
◦
(r) 881.992e-3 362.719e-6 10.000 881.992e-3 0
(a) 893.240e-3 820.525e-6 8.000 881.992e-3 11.248e-3
(b) 886.912e-3 1.921e-3 10.000 881.992e-3 4.920e-3
(c) 887.088e-3 830.455e-6 10.000 881.992e-3 5.096e-3
(d) 885.561e-3 957.555e-6 9.000 881.992e-3 3.569e-3
indoor
45
◦
(r) 838.086e-3 37.490e-6 4.000 838.086e-3 0
(a) 862.706e-3 1.079e-3 4.000 838.086e-3 24.620e-3
(b) 854.846e-3 2.750e-3 5.000 838.086e-3 16.760e-3
(c) 840.750e-3 20.712e-6 3.000 838.086e-3 2.663e-3
(d) 839.188e-3 53.872e-6 3.000 838.086e-3 1.102e-3
outdoor
90
◦
(r) 883.245e-3 25.067e-6 4.000 883.245e-3 0
(a) 888.800e-3 14.479e-6 3.000 883.245e-3 5.555e-3
(b) 882.519e-3 807.959e-6 4.000 883.245e-3 726.362e-6
(c) 881.964e-3 813.967e-6 5.000 883.245e-3 1.282e-3
(d) 882.181e-3 249.838e-6 4.000 883.245e-3 1.065e-3
outdoor
45
◦
(r) 1.733 82.370e-6 5.000 1.733 0
(a) 1.747 2.096e-3 5.000 1.733 13.809e-3
(b) 1.737 2.827e-3 5.000 1.733 4.119e-3
(c) 1.729 472.108e-6 4.000 1.733 4.515e-3
(d) 1.731 632.497e-6 4.000 1.733 1.632e-3
pilot
study
(r) 1.733 82.370e-6 5.000 1.733 0
(a) 1.790 33.749e-3 27.000 1.733 56.605e-3
(b) 1.751 13.249e-3 26.000 1.733 18.326e-3
(c) 1.726 5.354e-3 27.000 1.733 6.882e-3
(d) 1.727 5.486e-3 27.000 1.733 6.431e-3
huge gain in accuracy is due to the definition of the
reference method, as the requirement that the pro-
jected laser beam has to be fully on the visible surface
causes the big systematic error of the measurement
method.
As a result of our experimental evaluation, we
will further work on improving the individual meth-
ods to automatically detect outliers (e.g. by employ-
Measuring Human-made Corner Structures with a Robotic Total Station using Support Points, Lines and Planes
25