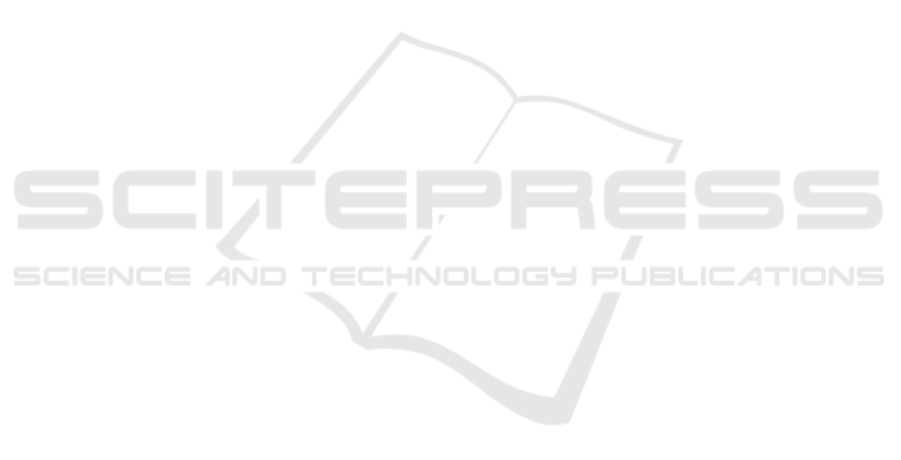
mula for the case of positive item assembly and disas-
sembly times and show that a ∆ increase in the assem-
bly and disassembly time is equivalent to a ∆ decrease
in the tolerable wait. Using this finding we apply the
(Dreyfuss and Giat, 2016) algorithm to find a solution
to the battery swapping problem, i.e., how to allocate
spare batteries in the network, and make the following
contributions.
We estimate the battery allocation problem of the
Better Place corporation if it had succeeded going
widespread in Israel and derive the optimal solution
for different service criteria. This example provides
valuable insight into the critical importance of assess-
ing correctly the tolerable wait time and the signifi-
cant losses that the firm incurs if it neglects to do so.
Second, we estimate the savings attained by reducing
battery swapping time. Third, we show how customer
arrival rate creates two classes of battery exchange
stations and therefore managers should develop two
different policies with respect to their service time to
customers. Although the Better Place adventure has
ended with bankruptcy in 2013, the battery swapping
idea is either applied or considered by other compa-
nies (e.g. XJ Group Corporation in Qingdao, Tesla
in California and Gogoro in Taipei). The model pre-
sented in this paper, therefore, may yet be applied in
real-life large-scale situations.
2 LITERATURE REVIEW
Electric vehicles are considered an environmentally-
friendly alternative to internal combustion engine cars
and are projected to eventually replace these fuel-
burning cars (Dijk et al., 2013). Drivers, however,
are still wary of these vehicles and therefore, many
governments provide substantial tax incentives to en-
courage their widespread adoption. Notable examples
are West European countries, the United States, China
and Japan (Zhou et al., 2015). Despite these efforts,
many drivers are wary of purchasing these cars and
most governments adoption goals have not been met
(Coffman et al., 2016). The major customer concern
is the “range anxiety”, namely, the fact that batteries
have limited range and their recharging time is very
long compared to internal combustion engine cars.
An innovative idea to overcome these issues was in-
troduced by the US-based company Better Place who
proposed to separate the vehicle ownership from the
battery ownership. In lieu of owning the battery, car
owners will purchase battery services from a firm that
will establish a network of battery swapping stations.
Researcher are examining many aspects of this propo-
sition such as the station design, the battery removal
and installation times, the required number of spare
batteries and the network layout and managing the
loads on the power grid (Mak et al., 2013; Yang and
Sun, 2015; Sarker et al., 2015). We contribute to
this research by solving the spare battery allocation
problem and demonstrating a large-scale application
of this problem.
The assumption that customers will tolerate a cer-
tain wait is at the core of this paper, which lies at the
intersection of inventory and customer service mod-
els. While the concept of a tolerable wait is hardly
ever considered in inventory models, it is quite com-
mon in the service industry and is associate with
numerous terms such as “expectation” (Durrande-
Moreau, 1999), “reasonable duration” (Katz et al.,
1991), “maximal tolerable wait” (Smidts and Pruyn,
1999) and “wait acceptability” (Demoulin and Dje-
lassi, 2013). From a service-oriented approach, the
customer’s attitude to wait is mainly subjective and
has cognitive and affective aspects (Demoulin and
Djelassi, 2013). From a logistics point of view this
wait is more objective and usually stated in the service
contract. Indeed, researchers have observed that most
inventory models fail “to capture the time-based as-
pects of service agreements as they are actually writ-
ten” (Caggiano et al., 2009, p.744). Our paper fills
this void by incorporating the tolerable wait into the
optimization criterion.
Our battery swapping network may be modelled
as an exchangeable-item repair system (Avci et al.,
2014). These inventory systems have been investi-
gated by researchers in different contexts (Basten and
van Houtum, 2014). A common performance mea-
sure for such systems is the fill rate, which measures
the fraction of customers who are served upon ar-
rival (Shtub and Simon, 1994; Caggiano et al., 2007).
These papers, however, do not develop explicit for-
mulas for the window fill rate but use numerical tech-
niques. In contrast, (Berg and Posner, 1990) develop
a formula for the window fill rate in a single loca-
tion when item assembly and disassembly is zero, and
(Dreyfuss and Giat, 2016) find that the window fill
rate is generally S-shaped with number spares in the
location and exploit this property to develop an effi-
cient near-optimal algorithm for finding the optimal
spare allocation. We extend these papers by consid-
ering the case of positive assembly and disassembly
times.
3 THE MODEL
Customers arrive with a depleted battery to a battery
swapping network that comprises L stations. Upon ar-
Optimizing Spare Battery Allocation in an Electric Vehicle Battery Swapping System
39