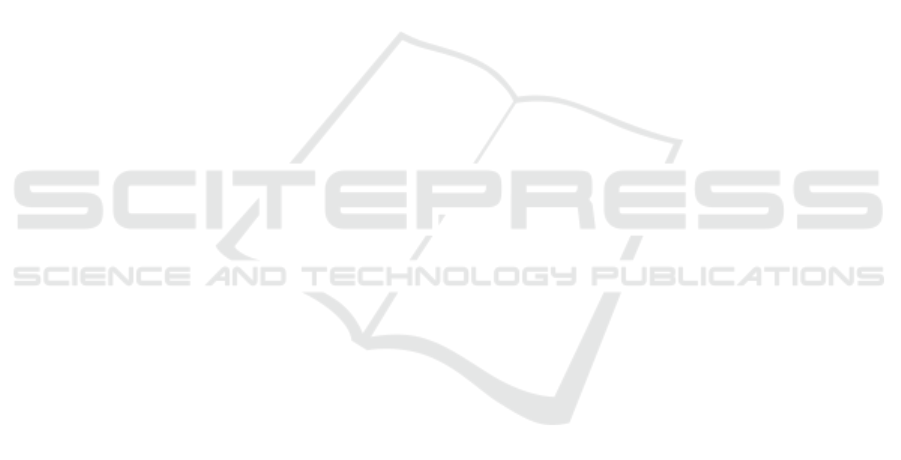
Application of Component Monitoring on
the Power Control Unit
Component monitoring was applied on the power
control unit provided by a supplier and several issues
were found. For instance, duplicated notifications on
state changes in a situation where a single notifica-
tion is expected and missing notifications when the
system goes on UPS source. Statistical analysis was
also applied on execution traces. The time intervals
for completing the executions of a given command
were collected and plotted in a diagram. The actual
distribution shape showed two peaks whereas a single
peak was expected. Further investigation revealed the
implementation decisions that were the cause of this
effect.
The described issues were missed in system level
tests. Component monitoring of behavior including
time improved the testing process.
7 CONCLUSIONS
The need for precise component interface specifica-
tions is longstanding in the industry and has drawn
attention of the research community. We presented
ComMA, a framework for interface behavior specifi-
cation with a rich tool support for different develop-
ment phases. The DSLs in ComMA integrate tech-
niques and results from different research areas and
provide a single entry point for engineers to specify
and develop component interfaces.
We did not employ the full expressive power of
the used formal languages. Instead, DSL constructs
are selected on the basis of the concrete needs of the
engineers and optimized for solving their most recur-
ring problems. Our experience in applying the DSLs
shows that this approach is crucial for the tool and lan-
guage adoption along with pragmatical aspects like
stable editors, ergonomic concrete syntax and visual-
ization. Whenever necessary, capabilities of special-
ized analysis tools can be used by building bridges in
the form of model transformations.
In general, ComMA was successfully applied on
the power control unit and fulfilled the tasks that were
the initial motivation of the framework. The applica-
tion of the techniques to several other components at
Philips is an ongoing work. This will provide further
validation insights.
The developed languages are not business-specific
and are not restricted to the medical domain. They are
aimed at problems that are found in other domains as
well and utilize general techniques thus making the
framework easily generalizable.
Future work intentions include extending the
toolset with transformations to model-based testing
and model checking facilities. Further experimenta-
tion with model learning aims at extending and im-
proving the interface behavior extraction from exist-
ing components.
REFERENCES
Barringer, H., Rydeheard, D. E., and Havelund, K. (2007).
Rule systems for run-time monitoring: From Eagle to
RuleR. In Sokolsky, O. and Tasiran, S., editors, Run-
time Verification, RV 2007, volume 4839 of Lecture
Notes in Computer Science, pages 111–125. Springer.
Behrmann, G., David, A., and Larsen, K. G. (2004). A
tutorial on Uppaal. In Bernardo, M. and Corradini, F.,
editors, Formal Methods for the Design of Real-Time
Systems, volume 3185 of Lecture Notes in Computer
Science, pages 200–236. Springer.
Bettini, L. (2013). Implementing Domain-Specific Lan-
guages with Xtext and Xtend. Packt Publishing Ltd.
Falcone, Y., Havelund, K., and Reger, G. (2013). A tutorial
on runtime verification. In Broy, M., Peled, D. A., and
Kalus, G., editors, Engineering Dependable Software
Systems, volume 34 of NATO Science for Peace and
Security Series, D: Information and Communication
Security, pages 141–175. IOS Press.
Groote, J. F. and Mousavi, M. R. (2014). Modeling and
Analysis of Communicating Systems. MIT Press.
Kim, H., Fried, D., Menegay, P., Soremekun, G., and Os-
ter, C. (2013). Application of integrated modeling and
analysis to development of complex systems. Proce-
dia Computer Science, 16:98 – 107.
Leucker, M. and Schallhart, C. (2009). A brief account of
runtime verification. The Journal of Logic and Alge-
braic Programming, 78(5):293 – 303.
Ouaknine, J. and Worrell, J. (2008). Some recent results in
metric temporal logic. In Cassez, F. and Jard, C., edi-
tors, Formal Modeling and Analysis of Timed Systems,
6th International Conference, FORMATS 2008, Saint
Malo, France, September 15-17, 2008. Proceedings,
volume 5215 of Lecture Notes in Computer Science,
pages 1–13. Springer.
G.H. Broadfoot (2005). ASD case notes: Costs and ben-
efits of applying formal methods to industrial control
software. In Fitzgerald, J., Hayes, I., and Tarlecki, A.,
editors, FM 2005: Formal Methods, LNCS, vol. 3582,
pages 548–551. Springer, Heidelberg.
Theelen, B. D., Florescu, O., Geilen, M., Huang, J., van der
Putten, P., and Voeten, J. (2007). Software/Hardware
Engineering with the Parallel Object-Oriented Specifi-
cation Language. In Proc. of MEMOCODE’07, pages
139–148. IEEE.
van Deursen, A. and Klint, P. (1998). Little languages: lit-
tle maintenance? Journal of Software Maintenance,
10(2):75–92.
MODELSWARD 2017 - 5th International Conference on Model-Driven Engineering and Software Development
352