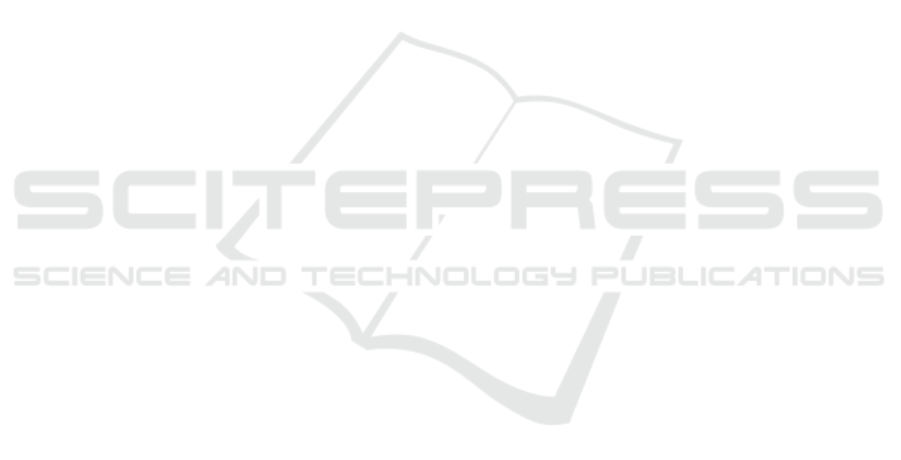
the nominal temporal resolution of 120 ns, which is
in the order of the minimum event delay provided by
the SCD sensor.
Finally, besides being the system able of work-
ing at such high speeds, the system is small, portable,
with a synchronous control and is oriented to limited
resources systems, as autonomous robotics.
ACKNOWLEDGEMENTS
This work has been supported by the Spanish Min-
istry of Economy and Competitiveness (MINECO)
and the EU regional development funds (FEDER)
project: TEC2015-66947-R.
REFERENCES
Acosta, D., Garcia, O., and Aponte, J. (2006). Laser tri-
angulation for shape acquisition in a 3d scanner plus
scanner. In Ceballos, S., editor, CERMA2006: Elec-
tronics, Robotics and Automotive Mechanics Confer-
ence, Proceedings, pages 14–19. IEEE Computer So-
ciety. Electronics, Robotics and Automotive Mechan-
ics Conference, Cuernavaca, MEXICO, SEP 26-29,
2006.
Boluda, J. A., Pardo, F., and Vegara, F. (2016). A selective
change driven system for high-speed motion analysis.
Sensors, 16(11):1875:1–19.
Camunas-Mesa, L., Zamarreno-Ramos, C., Linares-
Barranco, A., Acosta-Jimenez, A. J., Serrano-
Gotarredona, T., and Linares-Barranco, B. (2012).
An Event-Driven Multi-Kernel Convolution Proces-
sor Module for Event-Driven Vision Sensors. IEEE
J. Solid-St. Circ., 47(2):504–517.
Camunas-Mesa, L. A., Serrano-Gotarredona, T., and
Linares-Barranco, B. (2014). Event-driven sensing
and processing for high-speed robotic vision. In 2014
IEEE Biomedical Circuits and Systems Conference
(BIOCAS), Biomedical Circuits and Systems Confer-
ence, pages 516–519. IEEE; IEEE Circuits & Syst
Soc; Nano Tera; Medtronic Inc; gsk; Ecole Polytech-
nique Federale Lausanne; CSEM; IEEE Engn Med &
Biol Soc.
Gollisch, T. and Meister, M. (2008). Rapid neural coding
in the retina with relative spike latencies. Science,
319(5866):1108–1111.
Herculano-Houzel, S. (2009). The human brain in num-
bers: a linearly scaled-up primate brain. Front. Hum.
Neurosci., 3.
Khoshelham, K. and Elberink, S. O. (2012). Accuracy and
Resolution of Kinect Depth Data for Indoor Mapping
Applications. Sensors, 12(2):1437–1454.
Liu, S.-C., Delbruck, T., Indiveri, G., Whatley, A., and Dou-
glas, R. (2015). Event-Based Neuromorphic Systems.
John Wiley & Sons Ltd., The Atrium, Southern Gate,
Chichester, West Sussex, PO19 8SQ, England, United
Kingdom.
Mahowald, M. (1992). VLSI Analogs of neural visual pro-
cessing: A synthesis of form and function. PhD thesis,
Computer Science Divivision, California Institute of
Technology, Pasadena, CA.
Pardo, F., Boluda, J. A., and Vegara, F. (2015). Selec-
tive Change Driven Vision Sensor With Continuous-
Time Logarithmic Photoreceptor and Winner-Take-
All Circuit for Pixel Selection. IEEE J. Solid-St. Circ.,
50(3):786–798.
Pardo, F., Zuccarello, P., Boluda, J. A., and Vegara, F.
(2011). Advantages of selective change driven vision
for resource-limited systems. special issue on video
analysis on resource-limited systems. IEEE T. Circ.
Syst. Vid., 21(10):1415–1423.
Serrano-Gotarredona, R., Oster, M., Lichtsteiner, P.,
Linares-Barranco, A., Paz-Vicente, R., Gomez-
Rodriguez, F., Kolle Riis, H., Delbruck, T., Liu, S. C.,
Zahnd, S., Whatley, A. M., Douglas, R., Hafliger, P.,
Jimenez-Moreno, G., Civit, A., Serrano-Gotarredona,
T., Acosta-Jimenez, A., and Linares-Barranco, B.
(2006). Aer building blocks for multi-layer multi-
chip neuromorphic vision systems. In Weiss, Y.,
Sch
¨
olkopf, P. B., and Platt, J. C., editors, Advances
in Neural Information Processing Systems 18, pages
1217–1224. MIT Press.
van Schaik, A., Delbruck, T., and Hasler, J. (2015). Neuro-
morphic Engineering Systems and Applications. Fron-
tiers in Neuroscience. Frontiers Media.
Vincent, J. F. V. (2009). Biomimetics - a review. Proceed-
ings of the Institution of Mechanical Engineers Part
H-Journal of Engineering in Medicine, 223(H8):919–
939.
Yousefzadeh, A., Serrano-Gotarredona, T., and Linares-
Barranco, B. (2015). Fast pipeline 128x128 pixel spik-
ing convolution core for event-driven vision process-
ing in fpgas. In Event-based Control, Communication,
and Signal Processing (EBCCSP), 2015 International
Conference on, pages 1–8. IEEE.
Zuccarello, P., Pardo, F., de la Plaza, A., and Boluda, J. A.
(2010a). A 32×32 pixels vision sensor for selec-
tive change driven readout strategy. In Fringe Posters
of the 36th European Sold-State Circuits Confernece
(ESSCIRC 2010).
Zuccarello, P., Pardo, F., de la Plaza, A., and Boluda, J. A.
(2010b). 32×32 winner-take-all matrix with single
winner selection. Electron. Lett., 46(5):333–335.
High-speed Motion Detection using Event-based Sensing
253