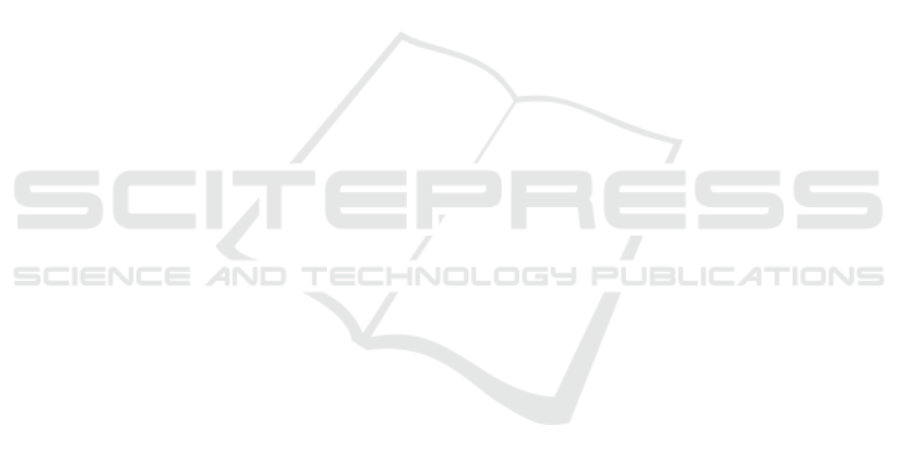
Once the dwell time prediction and/ or the storage
position of each incoming container at the yard have
been determined, the system generated a report with
this information. This report may include a graphical
representation of the yard. In this report, the location
in which the current container must be assigned is
specified (label 4 in the Figure 2). Based on this
information the yard planner may decide whether to
accept to locate the import container in the suggested
position. This action (label 5) is recorded in the
Action Database. Here, our idea is that the learning
system is generating solutions for the problem and the
human expert can validate them as being correct or
wrong, knowledge that can be further exploited to
refine the learning method of the system.
Finally (label 6), the decision made by the yard
planner is communicated to the TOS, which records
the transaction. As a final comment in this matter, we
observe that the architecture is not limited for a single
user. Rather, more than one yard planner may access
the service concurrently, which can be an
advantageous feature, as this information for
instance, could be provided to the yard crane
operators in a mobile device.
5 CASE STUDY: PORT OF
ARICA IN CHILE
The port of Arica, Chile is used in this case study
because it presents a high level of uncertainty in the
import processes and huge container dwell times. The
port of Arica occupies the 43rd position in the Latin
American containerized movements ranking
provided by UN-ECLAC; and the 6th position in the
Chilean port system, with a total of 204,174 TEUs
transferred in 2013 (Doerr 2013). The port consists
of a single multi-purpose terminal whose main
characteristic is that about 70% of the cargo
corresponds to cargo in transit from Bolivia. The port
presents special conditions for cargo handling, due to
the political agreements between Chile and Bolivia, a
reason for which the cargo has no storage fee (exports
for 60 days and imports up to 365 days). Furthermore,
the main hinterland (located in Bolivia) is more than
1000 kilometers away, in contrast with the main
Chilean ports, Valparaiso and San Antonio, whose
main hinterland (Metropolitan Region of Santiago) is
located at 120 kilometers from the ports.
The port of Arica lacks coordination of systems
with the hinterland such as appointment or booking
systems, or electronic data interchange. This fosters
the uncertainty and variability in port operations,
especially for the import processes. Long service
times (truck turnaround times) and container
rehandles are commonly observed. Under this
situation, the current practice of the yard managers is
to assign space to containers in a semi-random
fashion, where containers are located at the yard
considering only very simple rules that maximize
space utilization. A segregation-based policy for
storage space assignment of export containers has
been an efficient strategy for reducing rehandles
incurred when containers are loaded on the vessel.
Segregating export containers is commonly done
based on the vessel´s characteristics and the
corresponding route. These characteristics are
considered when the stowage plan is generated and
hence, rehandles are potentially minimized. In
contrast, the criteria for segregating import containers
are not so straightforwardly determined, especially if
high levels of uncertainty on the dispatching times are
observed.
In this paper a methodology to implement a dwell
time segregated policy for assigning space to import
containers is proposed. The policy considers
segregating containers based on predicted dwell time
intervals. In order to evaluate the different
classification and multi-classification algorithms
employed, the following metrics have been
considered: (i) number of instances correctly
classified, (ii) accuracy, (iii) Kappa´s coefficient; (iv)
the mean squared error; (v) the mean error in time
units” and (vi) the mean error for categorized factors.
A data base with container movements for the
years 2011, 2012 and August 2013 is included, with
a total of 151,640 import containers. Seven factors
were considered: (1) size of the container (20/40), (2)
type of container (Dry, Reefer, High Cube, etc.), (3)
the status of the container (full or empty), (4) weight,
(5) ship where the container is unloaded, (6)
consignee or customer, and (7) the cargo’s port of
origin.
The first four factors correspond to characteristics
of the container. The factors are numerical (size of
container and weight) and nominal (type, status, ship,
port of origin, consignee). The only dual attribute is
dwell time, and the nominal variable consignee has
the largest number of classes (about 5000 to 7000). It
is important to mention that the weight and port of
origin are factors not previously employed in the
literature (see Table 1).
ICORES 2017 - 6th International Conference on Operations Research and Enterprise Systems
134