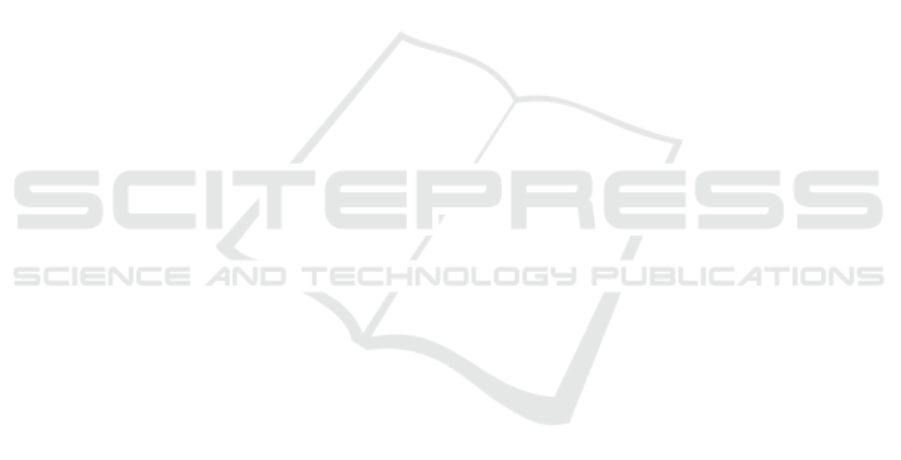
Christie, R. M. and Wu, S. D. (2002). Semiconductor capac-
ity planning: stochastic modelingand computational
studies. IIE Transactions, 34(2):131–143.
Escalona, P. and Ram
´
ırez, D. (2012). Expansi
´
on de capaci-
dad para un proceso, m
´
ultiples
´
ıtems y mezcla de tec-
nolog
´
ıas. In 41 Jornadas Argentinas de Informatica.
Fleischmann, B., Ferber, S., and Henrich, P. (2006). Strate-
gic planning of bmw’s global production network. In-
terfaces, 36(3):194–208.
Geng, N., Jiang, Z., and Chen, F. (2009). Stochastic pro-
gramming based capacity planning for semiconductor
wafer fab with uncertain demand and capacity. Euro-
pean Journal of Operational Research, 198(3):899–
908.
Guigues, V. (2009). Robust production management. Opti-
mization and Engineering, 10(4):505–532.
Hood, S. J., Bermon, S., and Barahona, F. (2003). Capacity
planning under demand uncertainty for semiconductor
manufacturing. Semiconductor Manufacturing, IEEE
Transactions on, 16(2):273–280.
Julka, N., Baines, T., Tjahjono, B., Lendermann, P., and Vi-
tanov, V. (2007). A review of multi-factor capacity
expansion models for manufacturing plants: Search-
ing for a holistic decision aid. International Journal
of Production Economics, 106(2):607–621.
Karabuk, S. and Wu, S. D. (2003). Coordinating strategic
capacity planning in the semiconductor industry. Op-
erations Research, 51(6):839–849.
Levis, A. A. and Papageorgiou, L. G. (2004). A hierarchical
solution approach for multi-site capacity planning un-
der uncertainty in the pharmaceutical industry. Com-
puters & Chemical Engineering, 28(5):707–725.
Li, C., Liu, F., Cao, H., and Wang, Q. (2009). A
stochastic dynamic programming based model for un-
certain production planning of re-manufacturing sys-
tem. International Journal of Production Research,
47(13):3657–3668.
Lin, J. T., Chen, T.-L., and Chu, H.-C. (2014). A stochastic
dynamic programming approach for multi-site capac-
ity planning in tft-lcd manufacturing under demand
uncertainty. International Journal of Production Eco-
nomics, 148:21–36.
Lorca, A., Sun, X. A., Litvinov, E., and Zheng, T.
(2016). Multistage adaptive robust optimization for
the unit commitment problem. Operations Research,
64(1):32–51.
Luss, H. (1982). Operations research and capacity ex-
pansion problems: A survey. Operations research,
30(5):907–947.
Mart
´
ınez-Costa, C., Mas-Machuca, M., Benedito, E., and
Corominas, A. (2014). A review of mathematical pro-
gramming models for strategic capacity planning in
manufacturing. International Journal of Production
Economics, 153:66–85.
Miller, D. M. and Davis, R. P. (1977). The machine require-
ments problem. The International Journal of Produc-
tion Research, 15(2):219–231.
Pflug, G. C. (2000). Some remarks on the value-at-risk
and the conditional value-at-risk. In Probabilistic con-
strained optimization, pages 272–281. Springer.
Pimentel, B. S., Mateus, G. R., and Almeida, F. A. (2013).
Stochastic capacity planning and dynamic network
design. International Journal of Production Eco-
nomics, 145(1):139–149.
Pratikakis, N. E., Realff, M. J., and Lee, J. H. (2010). Strate-
gic capacity decision-making in a stochastic man-
ufacturing environment using real-time approximate
dynamic programming. Naval Research Logistics
(NRL), 57(3):211–224.
Rajagopalan, S., Singh, M. R., and Morton, T. E. (1998).
Capacity expansion and replacement in growing
markets with uncertain technological breakthroughs.
Management Science, 44(1):12–30.
Rastogi, A. P., Fowler, J. W., Carlyle, W. M., Araz, O. M.,
Maltz, A., and B
¨
uke, B. (2011). Supply network
capacity planning for semiconductor manufacturing
with uncertain demand and correlation in demand
considerations. International Journal of Production
Economics, 134(2):322–332.
Rockafellar, R. T. and Uryasev, S. (2000). Optimization of
conditional value-at-risk. Journal of risk, 2:21–42.
Rockafellar, R. T., Uryasev, S., and Zabarankin, M. (2006).
Optimality conditions in portfolio analysis with gen-
eral deviation measures. Mathematical Programming,
108(2-3):515–540.
Sahinidis, N. V. (2004). Optimization under uncertainty:
state-of-the-art and opportunities. Computers &
Chemical Engineering, 28(6):971–983.
Shapiro, A. (2009). On a time consistency concept in risk
averse multistage stochastic programming. Opera-
tions Research Letters, 37(3):143–147.
Stephan, H. A., Gschwind, T., and Minner, S. (2010). Man-
ufacturing capacity planning and the value of multi-
stage stochastic programming under markovian de-
mand. Flexible services and manufacturing journal,
22(3-4):143–162.
Swaminathan, J. M. (2000). Tool capacity planning for
semiconductor fabrication facilities under demand un-
certainty. European Journal of Operational Research,
120(3):545–558.
Van Mieghem, J. A. (2003). Commissioned paper: Capacity
management, investment, and hedging: Review and
recent developments. Manufacturing & Service Oper-
ations Management, 5(4):269–302.
Wu, C.-H. and Chuang, Y.-T. (2010). An innovative ap-
proach for strategic capacity portfolio planning under
uncertainties. European Journal of Operational Re-
search, 207(2):1002–1013.
Wu, S. D., Erkoc, M., and Karabuk, S. (2005). Managing
capacity in the high-tech industry: A review of litera-
ture. The Engineering Economist, 50(2):125–158.
ICORES 2017 - 6th International Conference on Operations Research and Enterprise Systems
190