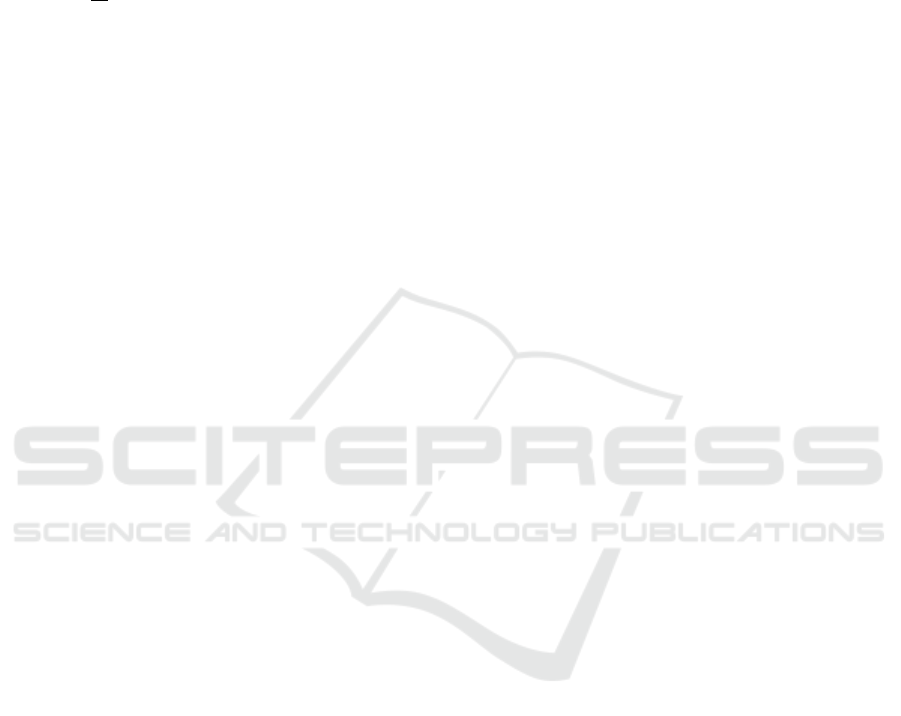
2.3 Complete Vehicle Model
Combining the drivetrain model, the external forces
and Newton’s second law of motion enables an ex-
pression for the longitudinal dynamics of the hauler.
In continuous time the expression is:
m
tot
(gr) ·
d
dt
v(t) = F
t
(t)−F
a
(t)−F
r
(t)−F
g
(t) (20)
where gr = gear and t = time.
2.4 Model Alteration for Optimisation
The complete vehicle model is to a large extent reused
when applied in the optimal control algorithm. Fol-
lowing the energy flow with the aim to calculate the
engine speed and torque corresponding to a step in
position and states, the structure of Section 2.1 to 2.3
is reused but in reversed order. When the ICE speed
and torque is known it is translated into a fuel flow.
Wheel Brake and Hub Reduction
(torque/speed node cgr). Differing from the
wheel brake model in Section 2.2 there is no need to
calculate the brake force when calculating the fuel
cost. If the step in energy state (speed decrease)
is negative and large enough so that application of
the wheel brakes is necessary to achieve balance in
equation (42), this will render in a loss of kinetic
energy but since the ICE will operate without adding
positive torque, no fuel will be injected and thus the
fuel cost is 0.
Torque Converter and Auxiliary Equipment
(torque/speed node engine). As the torque converter
is modelled only to be operating in lock-up mode, the
hauler never comes to full stop and consequently the
energy state is always > 0 in the optimised speed tra-
jectory. In practise this has limited impact since the
very high combined gear ratio in a hauler enables very
low vehicle speeds and since it is only at the end of
the cycle v = 0 is desired. At the engine speed/torque
node the loss from the ICE’s auxiliary equipment (al-
ternator, fan, etc) is added by means of a look-up ta-
ble, equation (21). This is not necessary when the
model is used for road estimation since the measured
torque signal from the engine ECU includes the aux-
iliary equipment loss.
T
Engine
= T
TC
+ T
aux.equip
(ω
TC
) (21)
Internal Combustion Engine (ICE). The inter-
nal combustion engine model in the optimisation al-
gorithm consists of a measured look up table with en-
gine speed, ω
Engine
, and engine torque, T
Engine
as in-
put and the fuel mass flow, ˙m
f
as output. The cost in
fuel mass, m
f
[kg], for one step in distance with corre-
sponding changes of states is evaluated using equation
(45).
3 ESTIMATION OF ROAD
INCLINATION AND ROLLING
RESISTANCE
Section 3 outlines a method for collecting the road re-
lated data that is needed in the optimisation algorithm.
The intention is to use sensors available in a standard
articulated hauler complemented with a commercially
available GPS. The data is collected and processed in
a Matlab algorithm and the road is stored in a map
like format with latitude and longitude coordinates as
identification points. The main parameters that are
identified in the algorithm are: latitude (ϕ), longitude
(λ), altitude (z), mean vehicle speed (v), road incli-
nation (α), vehicle heading (β), rolling resistance co-
efficient (c
r
), speed limit (v
max
) and travelling direc-
tion (Dir.). Of the quantities stored in the map, only
ϕ,λ,α,c
r
and v
max
are used in the optimisation algo-
rithm presented in Section 4. A method to estimate
the road inclination for on-road commercial vehicles
is exhaustively described in (Sahlholm, 2011) and has
been further enhanced for off-road vehicles and to in-
clude rolling resistance in the work of (Almes
˚
aker,
2010) and (Saaf and Hana, 2011). The method used
utilizes an extended Kalman filter (EKF) to work as
an observer for the unmeasured parameter rolling re-
sistance and also to help removing potential bias error
that develops when only using an inclination sensor to
measure the road inclination (Sahlholm, 2011), p.80-
88. In the estimation model, Section 3.2.6, the vehicle
model described in Section 2 and the road model de-
scribed in Section 3.2.5 are combined to generate the
quantities stored in the road map.
3.1 Map Building Process
The intention with the proposed map building process
is that the operator initially travels the track between
the loading and unloading sites 2 times to initiate the
map. The map data is updated off-line after each fin-
ished run which is a feasible scenario on a construc-
tion site since the distance between the loading and
unloading sites normally are within 2 km (approx. 6
min travel). On a high level, the map building process
can be described according to the steps below:
1. Operator drives the track between the loading and
unloading site forth and back as fast (but safe) as
possible while necessary sensor data is recorded.
2. The direction of the travel is detected and the data
updated accordingly.
3. The collected data is processed in the map-
building algorithm according to:
(a) Calculation of applied brake force.
Road Estimation and Fuel Optimal Control of an Off-Road Vehicle
61