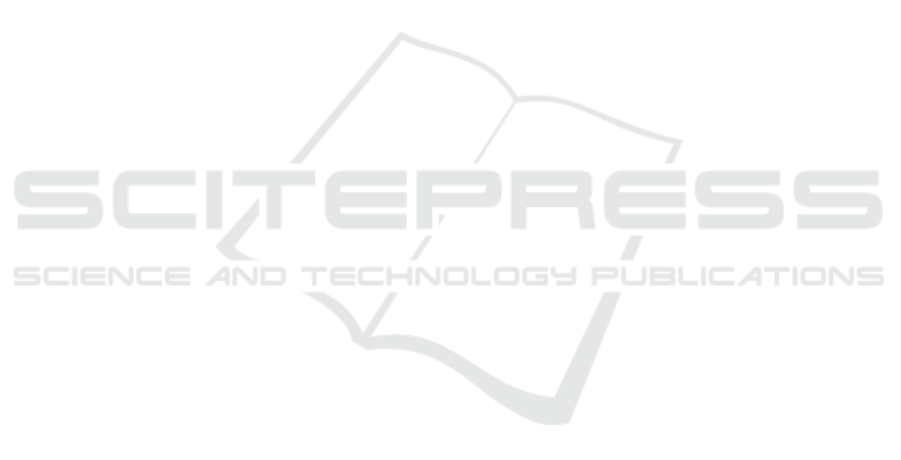
system to monitor thermal condition of machines us-
ing IR imaging and machine vision. Proposed sys-
tem is capable of detecting sudden heat changes and
autonomous heat flow by analysing thermal contour
behaviour or heat distribution profile. Major contri-
butions for the presented work are:
• All heat sources are detected, segmented, tracked
through out the inspection duration.
• Rate of heat flow on all directions for every heat
source are calculated.
• Presented system is computationally inexpensive
and performs in real-time.
2 LITERATURE REVIEW
Several studies are available on finding thermal
changes on infrared images. The studies are focused
several areas like diagnosing disease on human bod-
ies, monitoring building power consumption, moni-
toring factory manufactured product etc. Heat sig-
nature changes with disease either on the skin or in-
side muscular tissue. So researchers showed inter-
est on finding early symptoms of many diseases by
analysing the heat signature of human body (Kacz-
marek and Ruminski, 2009; Bagavathiappan et al.,
2009). Recently Rajoub & Zwiggelaar (Rajoub and
Zwiggelaar, 2014) proposed facial thermal analysis
for deception detection. These methods are limited
to check small heat changes from a single image and
are not suitable to measure heat flow on machines.
Building interior monitoring is another major us-
age of thermal imaging. Researchers proposed several
methods for 3D thermal mapping for build monitor-
ing (Vidas et al., 2013; Omar et al., 2014). Usages of
optical and infrared cameras are gaining interest for
creation of 3D thermal model (Rangel et al., 2014;
Saha et al., 2016). Thermal profile shows any heated
object very distinctly in the scene and this feature help
detection of any animal in dark. Researchers (Wein-
mann et al., 2014; Pal et al., 2016; Deshpande et al.,
2015) showed methods for object detection through
thermal imaging on robotic platform. All methods de-
tect heated object without any proposition for thermal
flow measurement.
Starman & Matz (Starman and Matz, 2011) pre-
sented a system for detecting cracks using infrared
thermography. This proposed system is very costly
and very specific to object. So the usages are lim-
ited for easy general usage for industrial predictive
analysis. Clough et al. (Clough et al., 2012) pro-
posed methods for condition monitoring thermal error
for spindles through thermal imaging. The system is
limited to only continuous temperature monitoring of
different parts of spindle. Al-Habaibeh & Robert (Al-
Habaibeh and Robert, 2003) proposed a method for
an autonomous monitoring system for several manu-
facturing like drilling, grinding, welding etc. using
novelty detection. Both the methods are lacking in
analysis of heat flow which is the most important fea-
ture for predictive machine inspection. Eftekhari et
al. (Eftekhari et al., 2013) proposed a fault detec-
tion algorithm for circuit fault in the stator windings
of an induction motor. The process generates his-
togram of temperature profile. It also explores the
correlation between hottest region on the motor body
and the fault severity. Subsequently, a comparison is
made with healthy motor features. Proposed method
is very much limited with the type of the machine
and required generalization for usage in a wide range
of machines. Ashish & Vijay (ASHISH and VIJAY,
2014) presented a survey for fault detection of ma-
chines based on temperature where standard devia-
tion, mean, skewness, energy, entropy are calculated
on the entire image to understand fault. So these sys-
tems are limited to find out any sudden abnormal heat
immediately.
3 SYSTEM OVERVIEW
Conditional monitoring is the process of identifying
a significant change which is indicative of a develop-
ing future fault in machines. Our goal is to present
a heat flow analysis model which will help us under-
stand further, such indicative behaviour of machines
in an unobtrusive way. Heat profile of any machines
changes with time and it flows from heat source to
colder regions, results in continuous heated regions.
We assume a machine would generate unwanted heat
patterns and flows in case of any fault. Therefore we
keep our interest only on finding heated regions and
corresponding heat flows.
3.1 FLIR based Infrared Imaging
Thermal imaging device or infrared cameras, can
only detect radiated heat energy. FLIR produces dif-
ferent variety of infrared imaging devices which is
customized for specific type usage. FLIR recently
launched a very cost effective product called FLIR
ONE (http://www.flir.com.hk/flirone), a smart-phone
attachment for easy usage by everyone. Our proposed
system uses a FLIR ONE as infrared imaging device.
FLIR ONE thermal sensor comes with 160x120 ther-
mal resolution and optical sensor with 640x480 res-
olution. Both images are blended using FLIR MSX
VISAPP 2017 - International Conference on Computer Vision Theory and Applications
638