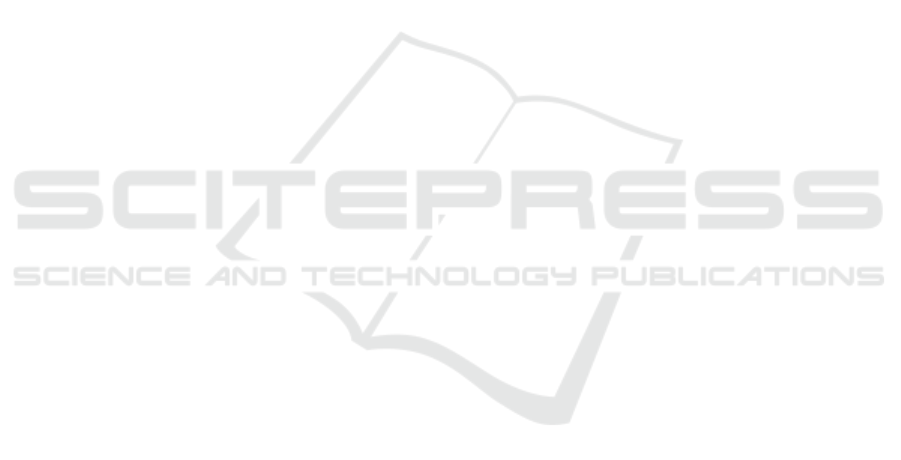
Colorni, A., Dorigo, M., Maniezzo, V., and Trubian, M.
(1994). Ant system for job-shop scheduling. Belgian
Journal of Operations Research, Statistics and Com-
puter Science, 34(1):39–53.
Davis, L. (1985). Job shop scheduling with genetic algo-
rithms. In Proceedings of an international conference
on genetic algorithms and their applications, volume
140. Carnegie-Mellon University Pittsburgh, PA.
Dell’Amico, M. and Trubian, M. (1993). Applying tabu
search to the job-shop scheduling problem. Annals of
Operations Research, 41(3):231–252.
Dorigo, M. (1992). Optimization, learning and natural al-
gorithms. Ph. D. Thesis, Politecnico di Milano, Italy.
Dorigo, M. and Gambardella, L. M. (1997a). Ant colonies
for the travelling salesman problem. BioSystems,
43(2):73–81.
Dorigo, M. and Gambardella, L. M. (1997b). Ant colony
system: a cooperative learning approach to the travel-
ing salesman problem. IEEE Transactions on evolu-
tionary computation, 1(1):53–66.
Dorigo, M., Maniezzo, V., and Colorni, A. (1996). Ant sys-
tem: optimization by a colony of cooperating agents.
IEEE Transactions on Systems, Man, and Cybernet-
ics, Part B (Cybernetics), 26(1):29–41.
Fisher, H. and Thompson, G. L. (1963). Probabilistic learn-
ing combinations of local job-shop scheduling rules.
Industrial scheduling, 3(2):225–251.
Gambardella, L. M. and Dorigo, M. (1996). Solving sym-
metric and asymmetric tsps by ant colonies. In In-
ternational conference on evolutionary computation,
pages 622–627.
Gao, J. and Chen, R. (2011). A hybrid genetic algorithm for
the distributed permutation flowshop scheduling prob-
lem. International Journal of Computational Intelli-
gence Systems, 4(4):497–508.
Garey, M. R., Johnson, D. S., and Sethi, R. (1976).
The complexity of flowshop and jobshop scheduling.
Mathematics of operations research, 1(2):117–129.
Jia, H., Fuh, J. Y., Nee, A. Y., and Zhang, Y. (2002). Web-
based multi-functional scheduling system for a dis-
tributed manufacturing environment. Concurrent En-
gineering, 10(1):27–39.
Jia, H., Fuh, J. Y., Nee, A. Y., and Zhang, Y. (2007). In-
tegration of genetic algorithm and gantt chart for job
shop scheduling in distributed manufacturing systems.
Computers & Industrial Engineering, 53(2):313–320.
Jia, H., Nee, A. Y., Fuh, J. Y., and Zhang, Y. (2003). A
modified genetic algorithm for distributed scheduling
problems. Journal of Intelligent Manufacturing, 14(3-
4):351–362.
Karimi, N. and Davoudpour, H. (2017). A knowledge-based
approach for multi-factory production systems. Com-
puters & Operations Research, 77:72–85.
Lawrence, S. (1984). Resource constrained project
scheduling: an experimental investigation of heuristic
scheduling techniques (supplement). Graduate School
of Industrial Administration.
Maniezzo, V. (1999). Exact and approximate nondeter-
ministic tree-search procedures for the quadratic as-
signment problem. INFORMS journal on computing,
11(4):358–369.
Naderi, B. and Azab, A. (2014). Modeling and heuristics for
scheduling of distributed job shops. Expert Systems
with Applications, 41(17):7754–7763.
Naderi, B. and Azab, A. (2015). An improved model and
novel simulated annealing for distributed job shop
problems. The International Journal of Advanced
Manufacturing Technology, pages 1–11.
Naderi, B. and Ruiz, R. (2010). The distributed permutation
flowshop scheduling problem. Computers & Opera-
tions Research, 37(4):754–768.
St
¨
utzle, T. (1998). Local search algorithms for combina-
torial problems. Darmstadt University of Technology
PhD Thesis, 20.
St
¨
utzle, T. and Hoos, H. (1997). Max-min ant system and
local search for the traveling salesman problem. In
Evolutionary Computation, 1997., IEEE International
Conference on, pages 309–314. IEEE.
St
¨
utzle, T. and Hoos, H. (2000). Max–min ant system. Fu-
ture generation computer systems, 16(8):889–914.
Taillard, E. (1993). Benchmarks for basic scheduling prob-
lems. European Journal of Operational Research,
64(2):278–285.
Talbi, E.-G. (2009). Metaheuristics: from design to imple-
mentation, volume 74. John Wiley & Sons.
Weaknesses of Ant System for the Distributed Job Shop Scheduling Problem
581