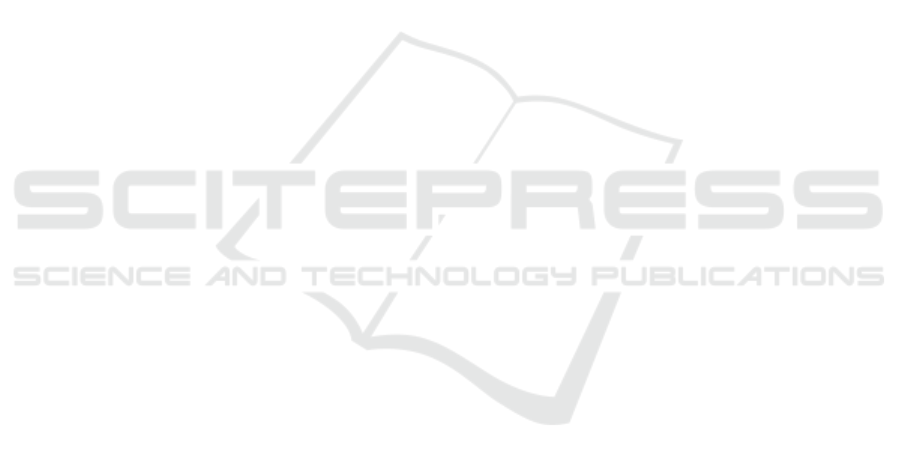
Langrangian Relaxation of Multi Level Capacitated Lot Sizing
Problem with Consideration of Lead Time
Hanaa Razki and Ahmed Moussa
Laboratory of InformationTechnologies and Communication, ENSA,University Abdelmalek Essaâdi, Tanger, Morroco
Razki.hanaa@gmail.com
Keyword: Tactical Planning, Multi Level Capacitated Lot Sizing Problem, Lagrangian Relaxation.
Abstract: Tactical planning consists to develop production plans by determining the quantities of products
manufactured by period to best meet customer demand at lower costs. This issue has been widely
discussed, according to two criteria: multi level and single level planning. The concept of multi level
reflects well the manufacturing structure. For this, we propose in this work a new mathematical model of lot
sizing finite capacity (Multi Level Capacitated Lot Sizing Problem) based on Lagrangian relaxation
optimization approach. Comparisons of this new model with traditional one demonstrate the efficiency of
this new approach as well in simulated case as real situations. The generated production plans are optimal
with 68% -98% compared to classical models.
1 INTRODUCTION
We are always looking for a relatively effective
solution that can help increase the level of
performance of production systems. This problem of
planning and scheduling production with limited
capacity resources reflects setup times, waiting and
production as well as different costs of production.
The formulations of the Big Bucket model (BB)
as Capacitated Lot Sizing Problem (CLSP) are
considered as a reference model for addressing the
plan generation of problematic production manager
in a single site environment (Comelli et al. 2008),
the Multi Level Capacitated Lot Sizing Problem
(MLCLSP), is recognized as a reference model and
deals with Manufacturing Resources Planning (MRP
and MRPII) issues, can be found in the literature for
some studies this problem (Almeder et al.2011,
Berretta et al.2005, Chen &Chu2003). If single site
issues have been extensively studied in the literature
(Nascimento et al.2010) point to the lack of a
reference model for multi site issues. This model
only determines the production quantities and
periods, regardless of the actual production sequence
of commands within a period of time. This type of
modeling has the advantage that it allows flexible
sequencing orders in a period, a significant cost
calculation. For small-Bucket models (SB) are
known, the Continuous Setup Lot Sizing Problem
(PRSP) and the Proportional Lot Sizing and
Scheduling Problem (PLSP).
The problem Multi Level Capacitated Lot Sizing
Problem (MLCLSP) is one of the most difficult
optimization problems known in the production. It
arises in any company that uses the sequential
approach to planning MRP. The approach was based
on the control of quantities on demand, compliance
with the BOM structure and the level of stock.
Consideration of production capacity and
product classifications pushed the authors to
consider the multiplicity of production resources
(Buschkuhl et al.2008), and we will find models of
mono or multi resource. Multi resource models
enable more accurate modeling of the operating
range of the various products and better estimate the
capacity of the production system. (Bel 1998)
demonstrated that to find feasible solutions for
MLCLSP is NP-complete, and when there are
considered setup time. Therefore, the proposed
Lagrangian heuristics include a feasibility strategy to
find feasible solutions from the penalization of the
constraints of the problem.
Most of the models and algorithms proposed
MLCLSP (Tempelmeier et al.2008) rely on one of
two possibilities: either the lead time is neglected,
and the lead time is taken into account, there is at
least one period for each component, forcing the
transit time (the number of periods) of finished
12
Razki, H. and Moussa, A.
Langrangian Relaxation of Multi Level Capacitated Lot Sizing Problem with Consideration of Lead Time.
In Doctoral Consortium (DCORES 2017), pages 12-19