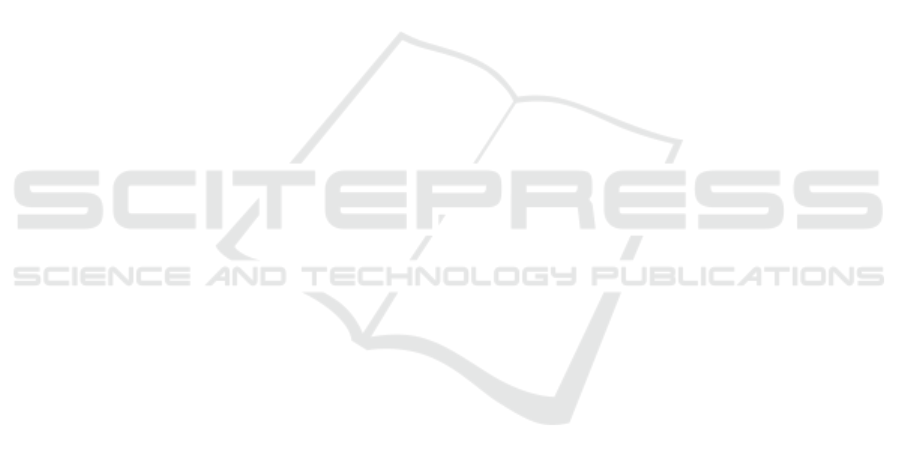
not move autonomously if the operator is not sending
any command. In this test the operator was simply
trying to center the arm above the hole of the con-
tainer and the control system was helping the operator
by slightly modifying the operator’s commands.
4 CONCLUSIONS AND
OUTLOOK
In this paper we presented a usable system for remote
environmental inspection. The data collected during
the inspection are used afterwards for the preparation
of a human intervention and for the integration with
simulation softwares. The system is easy to use on the
operator side and the collected data are shown in real
time on a Graphical User Interface. The GUI helps
can help the operator to collect the data based on the
data collected so far.
In future, this system could be integrated with an
anti-collision system which creates in real-time an oc-
cupancy grid map of the environment using the data
collected with the RGB-D cameras. This could allow,
coupled with path planning strategies, an autonomous
data collection approach.
Furthermore, a 3D alignment algorithm between
point clouds and CAD models can be added to the
system, in order to obtain remove the sensor noise
from the model and being able to compute precisely
the distance between the measure and the object.
REFERENCES
Agosta, S., Sierra, R., and Chapron, F. (2015). High-speed
mobile communications in hostile environments. In
Journal of Physics: Conference Series, volume 664,
page 052001. IOP Publishing.
Battistoni, G., Cerutti, F., Fasso, A., Ferrari, A., Muraro,
S., Ranft, J., Roesler, S., Sala, P., Albrow, M., and
Raja, R. (2007). The fluka code: Description and
benchmarking. In AIP Conference proceedings, vol-
ume 896, pages 31–49. AIP.
Cruz, L., Lucio, D., and Velho, L. (2012). Kinect and rgbd
images: Challenges and applications. In Graphics,
Patterns and Images Tutorials (SIBGRAPI-T), 2012
25th SIBGRAPI Conference on, pages 36–49. IEEE.
Deutsch, L. P. (1996). Gzip file format specification version
4.3.
Di Castro, M., Masi, A., Lunghi, G., and Losito, R. An in-
cremental slam algorithm for indoor autonomous nav-
igation.
Dumont, G., Pedrosa, F. B. D. S., Carbonez, P., Forkel-
Wirth, D., Ninin, P., Fuentes, E. R., Roesler, S., and
Vollaire, J. (2016). Integrated operational dosimetry
system at cern. Radiation Protection Dosimetry.
Engelhard, N., Endres, F., Hess, J., Sturm, J., and Burgard,
W. (2011). Real-time 3d visual slam with a hand-held
rgb-d camera. In Proc. of the RGB-D Workshop on
3D Perception in Robotics at the European Robotics
Forum, Vasteras, Sweden, volume 180, pages 1–15.
Forkel-Wirth, D., Roesler, S., Silari, M., Streit-Bianchi,
M., Theis, C., Vincke, H., and Vincke, H. (2013).
Radiation protection at cern. arXiv preprint
arXiv:1303.6519.
Hoppe, H., DeRose, T., Duchamp, T., McDonald, J., and
Stuetzle, W. (1992). Surface reconstruction from un-
organized points, volume 26. ACM.
Izadi, S., Kim, D., Hilliges, O., Molyneaux, D., Newcombe,
R., Kohli, P., Shotton, J., Hodges, S., Freeman, D.,
Davison, A., et al. (2011). Kinectfusion: real-time 3d
reconstruction and interaction using a moving depth
camera. In Proceedings of the 24th annual ACM sym-
posium on User interface software and technology,
pages 559–568. ACM.
Kershaw, K., Feral, B., Grenard, J.-L., Feniet, T., De Man,
S., Hazelaar-Bal, C., Bertone, C., and Ingo, R. (2013).
Remote inspection, measurement and handling for
maintenance and operation at cern. International
Journal of Advanced Robotic Systems, 10(11):382.
Leader, J. C. (1978). Atmospheric propagation of partially
coherent radiation. JOSA, 68(2):175–185.
Li, B. Y., Mian, A. S., Liu, W., and Krishna, A. (2013). Us-
ing kinect for face recognition under varying poses,
expressions, illumination and disguise. In Applica-
tions of Computer Vision (WACV), 2013 IEEE Work-
shop on, pages 186–192. IEEE.
Lunghi, G., Marin Prades, R., and Di Castro, M. (2016).
An advanced, adaptive and multimodal graphical user
interface for human-robot teleoperation in radioactive
scenarios. In Proceedings of the 13th International
Conference on Informatics in Control, Automation
and Robotics, volume 2, pages 224–231. ICINCO.
Meagher, D. (1982). Geometric modeling using octree en-
coding. Computer graphics and image processing,
19(2):129–147.
Modarres, M. (2006). Risk analysis in engineering: tech-
niques, tools, and trends. CRC press.
Spiezia, G., Brugger, M., Peronnard, P., Roeed, K., Masi,
A., Kramer, D., Calviani, M., Wijnands, T., Ferrari,
A., Pignard, C., et al. (2011). The lhc radiation moni-
toring system-radmon. PoS, page 024.
Taylor, J., Bordeaux, L., Cashman, T., Corish, B., Keskin,
C., Sharp, T., Soto, E., Sweeney, D., Valentin, J.,
Luff, B., et al. (2016). Efficient and precise interactive
hand tracking through joint, continuous optimization
of pose and correspondences. ACM Transactions on
Graphics (TOG), 35(4):143.
Wijnands, T. Alara principles: Cern alara approach. In SPS
technical coordination meeting, volume 10.
Zollh
¨
ofer, M., Nießner, M., Izadi, S., Rehmann, C., Zach,
C., Fisher, M., Wu, C., Fitzgibbon, A., Loop, C.,
Theobalt, C., et al. (2014). Real-time non-rigid recon-
struction using an rgb-d camera. ACM Transactions
on Graphics (TOG), 33(4):156.
ICINCO 2017 - 14th International Conference on Informatics in Control, Automation and Robotics
238