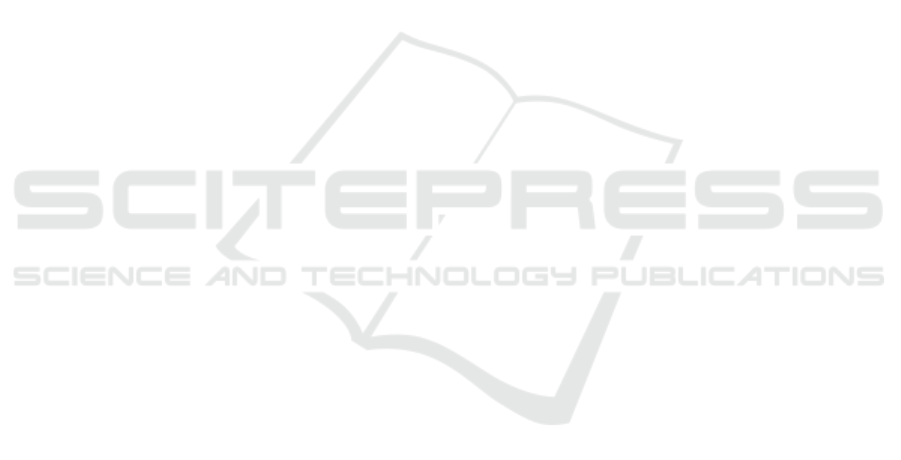
Postcondition: After an experiment, always prepare
for the next one (expNext transition) as follows:
6. If 3 was successful then remove the vacuum (tO f f
transition);
7. Enable the access into the IC (expIcEnt transi-
tion);
Procedure 3. The maintenance operations
(expMaint transition) must pe performed after 2
consecutive experiments at most.
Procedure 2 is identical to 1 with the exception
that it can contain only one shoot, expFin sequence.
The latter enforces maintenance operations after a
predefined number of experiments.
5 CONCLUSIONS
The current work proposes a novel approach for de-
riving operational procedures for a complex facil-
ity where multiple sub-systems interact between each
other. The constraints can be either local (at the
sub-system level) or global (between different sub-
systems). By using the MTSA software, we can au-
tomatically generate and simulate a procedure such
that the effects of the constraints can be understood.
A high workload represents the development of the
models based on the defined requirements. Further-
more, the constraint definition may include multiple
iterations based on their effects over the entire system
(the parallel composition of all sub-systems).
Future extensions of the current work are mostly
aimed to developing the models by including more
details regarding their behaviour. However, by aug-
menting the models complexity, the constraints defi-
nition will remain the same but their number will be
increased (based on the newly introduced states and
transitions). The ultimate goal for all further devel-
opments is the complete automation of different steps
(eg. automatic alignment procedure, automatic mis-
alignment detection and correction, etc.) and the im-
plementation of the synthesised controller for the au-
tomation of the entire operational process.
ACKNOWLEDGEMENTS
We would like to thank the members of the ELI-
NP team with special thanks to Ioan D
˘
ancus¸ (for the
fruitful insights regarding the alignment process) and
Daniel Ursescu (for reviewing and his valuable re-
marks). This work is supported by the Project Ex-
treme Light Infrastructure Nuclear Physics (ELI-NP)
- Phase II, a project co-financed by the Romanian
Government and European Union through the Euro-
pean Regional Development Fund.
REFERENCES
Bertolino, A., Inverardi, P., Pelliccione, P., Pelliccione, P.,
and Tivoli, M. (2009). Automatic synthesis of behav-
ior protocols for composable web-services. In Pro-
ceedings of the the 7th Joint Meeting of the European
Software Engineering Conference and the ACM SIG-
SOFT Symposium on The Foundations of Software En-
gineering, pages 141 – 150.
Braberman, V., D’Ippolito, N., Piterman, N., Sykes, D., and
Uchitel, S. (2013). Controller synthesis: From mod-
elling to enactment. In Proceedings of the 2013 Inter-
national Conference on Software Engineering, pages
1347 – 1350.
D’Ippolito, N., Braberman, V., Piterman, N., and Uchitel, S.
(2011). Synthesis of live behaviour models for fallible
domains. In 2011 33rd International Conference on
Software Engineering (ICSE), pages 211–220.
D’Ippolito, N., Braberman, V., Piterman, N., and Uchitel, S.
(2012). The Modal Transition System Control Prob-
lem, pages 155–170. Springer Berlin Heidelberg.
D’Ippolito, N., Fischbein, D., Chechik, M., and Uchitel, S.
(2008). Mtsa: The modal transition system analyser.
In 2008 23rd IEEE/ACM International Conference on
Automated Software Engineering, pages 475–476.
et.al., F. N. (2016). Laser driven nuclear physics at elinp.
Romanian Reports in Physics, 68:S37S144.
Gales, S., Balabanski, D. L., Negoita, F., Tesileanu, O., Ur,
C. A., Ursescu, D., and Zamfir, N. V. (2016). New
frontiers in nuclear physics with high-power lasers
and brilliant monochromatic gamma beams. Physica
Scripta, 91(9):093004.
Giannakopoulou, D. and Magee, J. (2003). Fluent model
checking for event-based systems. SIGSOFT Software
Engineering Notes, 28(5):257–266.
Isley, P. (2017). The modal transition system analyser.
http://mtsa.dc.uba.ar/.
Joslin, P. (2013). Synthesis of event-based controllers for
software engineering. PhD thesis, Imperial College
London.
Keller, R. M. (1976). Formal verification of parallel pro-
grams. Commun. ACM, 19(7):371 – 384.
Magee, J. and Kramer, J. (2006). Concurrency: State Mod-
els and Java Programs. Wiley Publishing, 2nd edition.
Ur, C., Balabanski, D., Cata-Danil, G., Gales, S., Morjan,
I., Tesileanu, O., Ursescu, D., Ursu, I., and Zamfir, N.
(2015). The elinp facility for nuclear physics. Nuclear
Instruments and Methods in Physics Research Sec-
tion B: Beam Interactions with Materials and Atoms,
355(9):198 – 202.
Ursescu, D., Cheriaux, G., Audebert, P., Kalashnikov, M.,
Toncian, T., Cerchez, M., Kaluza, M., Paulus, G.,
Priebe, G., Dabu, R., Cernaianu, M., Dinescu, M.,
Asavei, T., Dancus, I., Neagu, L., Boianu, A., Hooker,
C., Barty, C., and Haefner, C. (2016). Laser beam de-
livery at eli-np. Romanian Reports in Physics, 68:S11
S36.
Novel Approach of Deriving Operational Procedures for a Complex Research Facility
203