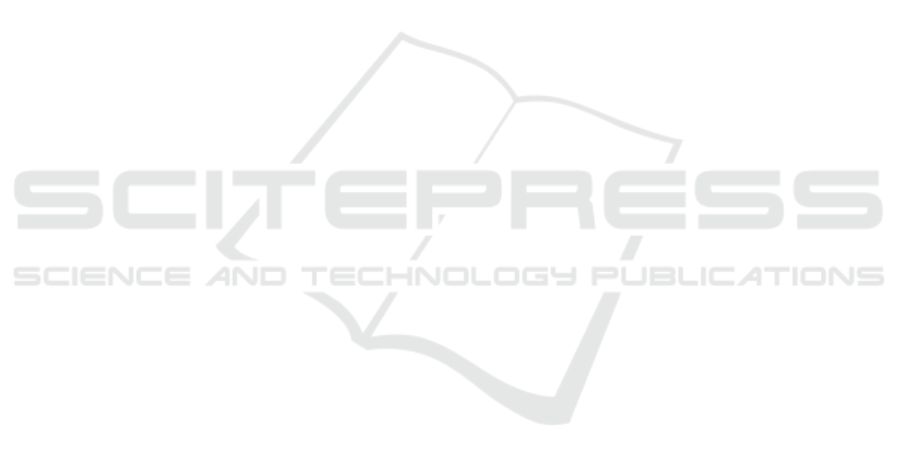
both examples. Work will be continued on improved
estimation of system matrices on operating regimes
with missing measurement data.
ACKNOWLEDGEMENTS
This work was partly supported by the project
OBSERVE of the Federal Ministry for Economic Af-
fairs and Energy, Germany (Grant-No.: 03ET1225C)
and partly supported by the Free and Hanseatic City
of Hamburg (Hamburg City Parliament publication
20/11568).
REFERENCES
Cichocki, A., Zdunek, R., Phan, A., and Amari, S. (2009).
Nonnegative matrix and tensor factorizations. Wiley,
Chichester.
Fanaee-T, H. and Gama, J. (2016). Tensor-based anomaly
detection: An interdisciplinary survey. Knowledge-
Based Systems, 98:130–147.
Gertler, J. (1991). Analytical redundancy methods in fault
detection and isolation. In Preprints of IFAC/IMACS
Symposium on Fault Detection, Supervision and
Safety for Technical Processes SAFEPROCESS91,
pages 9–21.
Isermann, R. (2006). Fault-diagnosis systems: an introduc-
tion from fault detection to fault tolerance. Springer
Science & Business Media.
Jagpal, R. (2006). EBC Annex 34 - computer aided eval-
uation of HVAC system performance - technical syn-
thesis report: Computer aided evaluation of HVAC
system performance.
Katipamula, S. and Brambley, M. (2005). Methods for
fault detection, diagnostics, and prognostics for build-
ing systems - a review, part I. HVAC&R Research,
11(1):3–25.
Kruppa, K. (2014). Dokumentation Matlab Heatlib - Zur
Verwendung mit Matlab. Dokumentation, Institut f
¨
ur
Regelungstechnik, TU Hamburg-Harburg.
Liberzon, D. (2003). Switching in systems and control,
ser. Systems & Control: Foundations & Applications.
Boston: Birkh
¨
auser.
Lichtenberg, G. (2011). Hybrid Tensor Systems. Habilita-
tion, Hamburg University of Technology.
Ljung, L. (2016). System identification toolbox: user’s
guide.
Mulders, A. V., Schoukens, J., Volckaert, M., and Diehl,
M. (2009). Two nonlinear optimization methods for
black box identification compared. IFAC Proceedings
Volumes, 42(10):1086 – 1091.
Murray-Smith, R. and Johansen, T. A. (1997). Multiple
Model Approaches to Modelling and Control. Taylor
and Francis, London.
Paduart, J., Lauwers, L., Swevers, J., Smolders, K.,
Schoukens, J., and Pintelon, R. (2010). Identification
of nonlinear systems using polynomial nonlinear state
space models. Automatica, 46(4):647 – 656.
Pangalos, G. (2015). Model-based Controller Design Meth-
ods for Heating Systems. dissertation, Hamburg Uni-
versity of Technology.
Pangalos, G., Eichler, A., and Lichtenberg, G. (2015). Hy-
brid Multilinear Modeling and Applications, pages
71–85. Springer International Publishing, Cham.
Pangalos, G. and Lichtenberg, G. (2012). Approach
to boolean controller design by algebraic relaxation
for heating systems. IFAC Proceedings Volumes,
45(9):210–215.
Rehault, N., Lichtenberg, G., Schmidt, F., and Harmsen,
A. (2013). Modellbasierte Qualit
¨
atssicherung des
energetischen Geb
¨
audebetriebs (ModQS). Abschluss-
bericht. Technical report.
Sewe, E., Harmsen, A., Pangalos, G., and Lichtenberg,
G. (2012). Umsetzung eines neuen Konzepts zur
Mehrkesselregelung mit Durchflusssensoren. HLH
L
¨
uftung/Klima - Heizung/Sanit
¨
ar - Geb
¨
audetechnik,
1:37 –42.
Van Overschee, P. and De Moor, B. (2012). Subspace iden-
tification for linear systems: Theory - Implementation
- Applications. Springer Science & Business Media.
Venkatasubramanian, V., Rengaswamy, R., Kavuri, S. N.,
and Yin, K. (2003). A review of process fault
detection and diagnosis: Part iii: Process history
based methods. Computers & chemical engineering,
27(3):327–346.
Vervliet, N., Debals, O., Sorber, L., and Lathauwer, L. D.
(2014). Breaking the curse of dimensionality using
decompositions of incomplete tensors: Tensor-based
scientific computing in big data analysis. IEEE Signal
Processing Magazine, 31(5):71–79.
Vervliet, N., Debals, O., Sorber, L., Van Barel, M., and
De Lathauwer, L. (2016). Tensorlab user guide.
Fault Detection for Heating Systems using Tensor Decompositions of Multi-linear Models
35