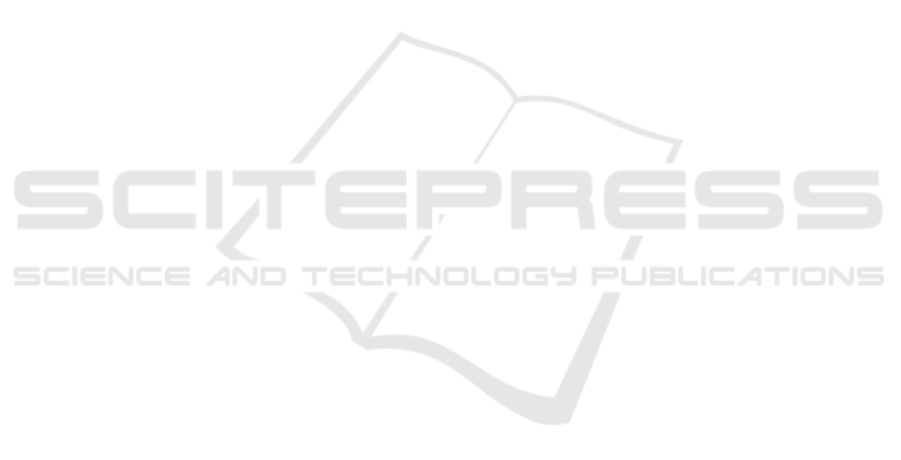
knowledge. The newly added knowledge should be
properly recorded and managed for avoiding
unnecessary loss and keeping
With development of information technology,
the development of aero-craft system is changing
towards a driving mode based on data, information,
knowledge and wisdom. The knowledge module and
product developing automation have becoming key
measures for improving development efficiency.
Thus, it requires unified depiction and organization
of knowledge storage, description, transmit, share
and reuse for covering corresponding aero-craft
development phrases. The method is supposed to
support the knowledge sharing, organizing and
automatic application during aero-craft development
procedure.
In this work, a novel knowledge network model
for aero-craft development is proposed for
integrating knowledge engineering and product
design. The main contributions include follows:
(1) Discussing the knowledge framework for
product development. Based on design of "product-
task-discipline", the internal structure and
connectivity of knowledge were discussed from
application and case study perspectives. The
framework covers all knowledge involving sectors
in product development.
(2) Constructing aerospace term base, and
using ontology language to express the standardized
terms and their interrelationships.
(3) Analysing product data model system and
combining multi-view requests. The relationships
between physical structure model, data result model,
case studies were discussed. Through connecting
product structure and development tasks, the reuse
of knowledge is improved. On the other hand, the
multi-disciplinary knowledge is automatically
matched to the product structure and development
tasks via using standardized terms in knowledge
expression, as a semantic support for knowledge
automation.
(4) Pushing knowledge based on application
scenarios within the knowledge network framework.
Taking aero-craft knowledge as a case study,
modelling it using ontology and using SPARQL
ontology reasoning query technology for knowledge
pushing and searching.
The merits of the proposed method: (1)
Combining knowledge network model and product
development mode, the knowledge generated during
the whole aero-craft development is organized and
modified to fit the requirements of practitioners with
the purpose of improving knowledge utilization
efficiency while lowering the management cost. (2)
Organizing knowledge according to the work flow,
which facilitates the automatic application of
knowledge in aero-craft development. (3) Fully
expressing the logic reasoning based on ontology
terms of knowledge, and knowledge pushing based
on scenarios is realized.
2 THE RELATED WORK
For knowledge organization and modelling the
current methods are only focus on single discipline
or function, as they are highly specified which are
impossible to satisfy the need of digital prototype
based developing mode. No report on life cycle
knowledge management and application. Some
researchers established knowledge models based on
product structure and specified disciplinary domain.
Yongdang proposed the implementing framework of
knowledge organization model for aircraft engine
design based on ontology (Yongdang et al., 2007).
Changjie et al. put forward ontology based
knowledge expressing method for tooling design
knowledge, which included four sub-ontology
models: design object, designer, design flow and
design knowledge (Changjie et al., 2014). Bock
established a product-based descriptive model to
depict products from environmental, behavioural,
and performance perspectives (Bock et al., 2010).
The existing methods have some values in various
applications, but they have certain limitations in
current product design activities. Physical
prototyping is now gradually replaced by digital
prototyping. The knowledge generated in the process
requires for proper management. Knowledge
organization model should be robust and adaptive
during the mode transformation, due to co-existence
of knowledge within new and old prototype
development modes (Abdullah et al., 2002). For
development of complicated product such as aero-
craft system, multi-disciplinary knowledge is
desirable, hence knowledge organization should.
Instead of single knowledge note, knowledge cluster
is required. Current knowledge models are
developed for certain phrase, which cannot handle
the life cycle (Teswanich et al., 2002). During the
establishing ontology, the relationships between
tasks, products and knowledge have always been
neglected. In the proposed knowledge model, digital
prototyping and expression of technical terms during
product development are discussed, with a focus on
modelling knowledge demand and application of
CAD system.
Research on Knowledge Network Modelling for Aero-craft System Design
241