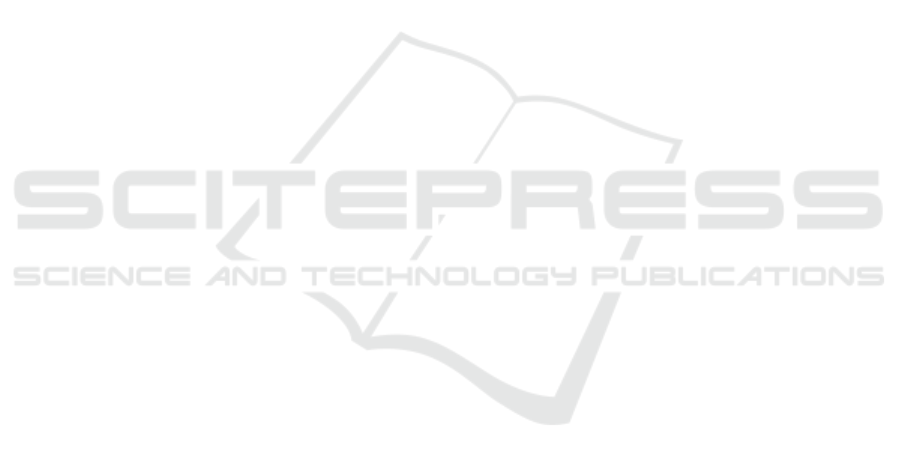
age and starvation without production, making the en-
ergy efficiency really low. Leaving a non-bottleneck
machine idle due to lack of multiple operation states
setting seems to be a routine and regular operating
practice in the industry. In (Z.Sun, 2011) considers
that modern machines or motors systems have multi-
ple adjustable power states instead of traditional ON,
OFF states. The power state is maintained on the ON
level when it is processing parts; while the power hi-
bernation mode may be triggered when it is detected
to be starved or blocked. In (L.Li, 2013), The inter-
actions between the adopted energy control decisions
and system state evolutions are modelled by Markov
decision process (MDP).The decision is to adjust the
energy mode for each machine according to not only
current states but also possible evolutions of system
states in the future. In (Z.Zhou, 2013), a heuristic
method considering throughput bottleneck detection
for real time electricity demand response under the
production constraint is introduced.
1.1 Energy Saving in Industrial Robots
One of the areas in which a significant amount of en-
ergy can be saved in manufacturing process is in in-
dustrial robots (IR). For example, the energy needed
during the production of cars is approximately 8%,
(D.Meike, 2011b). Therefore, the primary goal of
the optimization is to minimize the energy consump-
tion of a robotic cell for a given production rate by
changing the robot speeds, positions, order the oper-
ations and applying the robot power saving modes,
(L.Bukata, 2016). However, energy consumption re-
duction for IR can be achieved at different stages of
a manufacturing systems’ developments: During pro-
duction planning, commissioning process, or at opti-
mization stages, see (P.Matthias, 2015). At the pro-
duction planning stage, engineers are more flexible
with optimizing the process and defining a strategy
for reducing energy consumption, for example, by op-
timizing IR operation schedule, (D.Meike, 2011b) or
by optimizing IR parameters, like the speed and accel-
eration of the robots, (D.Meike, 2011a), (A.Kovetski,
2008). At the commissioning stage, reducing energy
consumption can be conducted by eliminating wait-
ing and iddle time of IR but manufacturing produc-
tivity must be considered. At the optimization stage,
the engineers cannot change the hardware apparatus
or the production rate. Therefore, the energy reduc-
tion must be done by releasing the actuator brake
earlier and implementing optimal trajectories using
time-scaling methods, (D.Meike, 2014), (P.Matthias,
2015), (S.Riazi, 2016).
1.2 Real World Line Balancing
Problems
Although many solutions for reducing the energy con-
sumption of IR have been provided, majority of them
are focused in primary stages. Optimizing the mo-
tion planning of IR can reduce energy consumption
but less interesting for practical point of view and
only effective for an IR manufacturers, (P.Matthias,
2015). Optimizing the operating parameters is a rela-
tively new method but is only effective in the produc-
tion planning stage, while the productivity rate at the
manufacturing system is planned, (P.Matthias, 2015).
In the end, an expert team designs the line, based on
all of these parameters and defines the maximum pro-
duction rate, adjust the IR parameters, program the
trajectories, schedule the tasks, etc. However, dur-
ing the lifespan of the line, which could be decades,
the line suffers a lot of changes due to market de-
mand with new products or models manufactured in
the same line, new technologies like for instance a
new robot arm that can run more faster than when
the line was designed, deteriorating systems that af-
fect the throughput and also produce a dynamic bot-
tleneck behaviour, etc, see (E.Garcia, 2016).
Many of the Operational Research approaches as
well as energy saving strategies implicity assume that
the problem to be solved involves a new, yet-to-be
build assembly line or yet-to-be-build-factory. How-
ever, the vast majority of real-world line balancing
tasks involve existing lines, (E.Falkenauer, 2005). In
fact, the target line tipically needs to be re-balanced
rather than balanced.
1.3 Previous Works
In (E.Falkenauer, 2005) was defined that each work-
station have its own identity, meaning that the work-
stations in the real world are indeed not identical.
The same concept was deep analyzed in our previous
works where not only the workstations are not identi-
cal, but also the components that form each machine
are different and do not have the same behaviour in
each cycle time repetition.The literature classify the
data used in the production line analysis into long-
term and short-term. Long-term is mainly used for
process planning, while short-term focuses primar-
ily on process control. In (E.Garcia, 2016), short-
term was divided into two new terms, mini-terms and
micro-terms, see Figure 1.
A mini-term may be defined as a part of the ma-
chine, in a policy preventive maintenance or a break-
down, which could be replaced in an easy and faster
maneuver than other machine sub-division. A micro-
Towards a Self-balancing Machine Velocity Production Line for Energy Saving
569