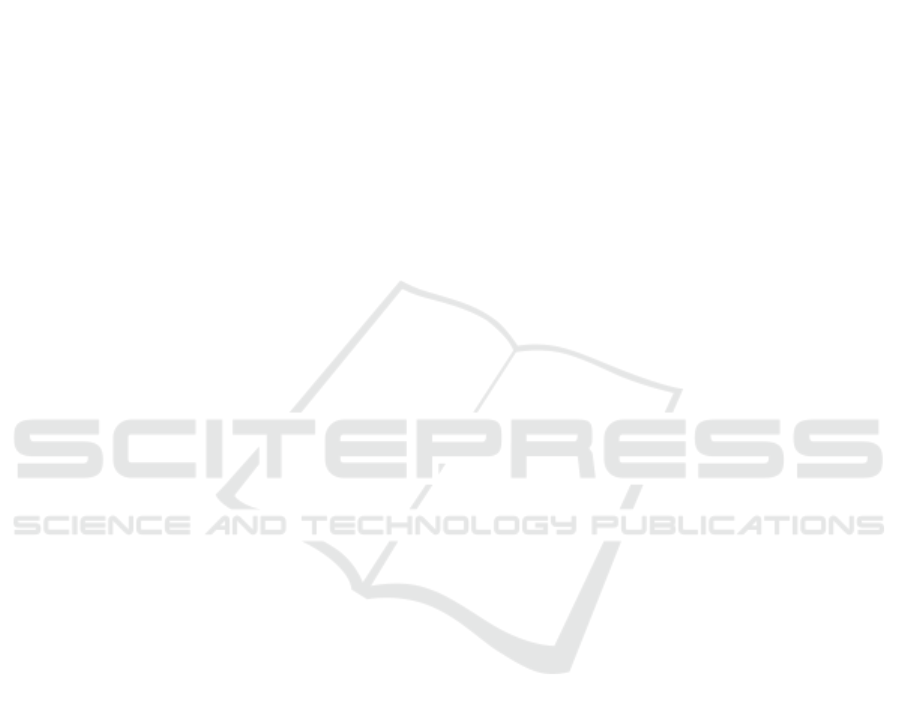
Impedance Control of a Redundant Parallel Manipulator
Juan de Dios Flores Mendez
1
, Henrik Schiøler
1
, Ole Madsen
2
and Shaoping Bai
2
1
Department of Electronic Systems, Aalborg University, Frederik Bajers Vej 7C, 9220, Aalborg East, Denmark
2
Department of Mechanical and Manufacturing Engineering, Aalborg University,
Fibigerstraede 16, 9220, Aalborg East, Denmark
Keywords:
Robotics, Redundant Parallel Manipulators, Control, Optimization, Compliant Motion, Impedance Control.
Abstract:
This paper presents the design of Impedance Control to a redundantly actuated Parallel Kinematic Manipulator.
The proposed control is based on treating each limb as a single system and their connection through the internal
interaction forces. The controller introduces a stiffness and damping matrices that decouples the dynamic
behaviour of the robot. Control allocation of torques is applied through an optimization that promotes even
distribution of torques over actuators. Simulations showed a good compliance behaviour in low frequencies.
1 INTRODUCTION
Parallel Kinematic Manipulators (PKMs) have been
mainly used in pick and place operations or posi-
tioning systems in manufacturing due to their high
speed, high accelerations and low inertia (Patel and
George, 2012), with applications such as assembly
(McCallion and Pham, 1979), positioning (Ming and
Higuchi, 1994), motion simulators (Salcudean et al.,
1994), pick and place (Powell, 1982), and material
processing operations such as drilling (Company and
Pierrot, 2002).
The inherent stiffness of the PKMs and higher
speed (Taghirad, 2013) than the serial kinematic ma-
nipulators make them ideal for performing different
tasks in the manufacturing sectors such as assembly
and material processing (Schutz and Wahl, 2011).
The tasks of assembly, material processing as
polishing or de-burring and material handling are
tasks that require compliant motions (Bruyninckx and
Schutter, 1996) i.e. the robot required to adapt the
torques and forces when in contact with environmen-
tal objects.
An approach to compliant motion is the so called
Impedance Control (Hogan, 1985). Impedance Con-
trol is classified as an indirect force control because is
designed to avoid the necessity to measure the force in
the mobile platform. The aim of Impedance Control
is to impose a desired apparent mechanical stiffness
and damping in the Cartesian space of the robot. In
a robotic system that can perform 3 translations by 3
actuators, it becomes a straight forward task because
there is a one to one mapping from the Cartesian space
to the actuator space. In a robotic system with actua-
tor redundancy it is not a trivial task.
PKMs with redundant actuation are those that
have more actuators than degrees of freedom. The
control of redundant PKMs requires the solution of
inverse dynamics which is not straight forward and
techniques as the Moore-Penrose pseudo inverse ma-
trix (Briot et al., 2013) or the null space of the forces
is used (Kock and Schumacher, 2011) to solve this
problem. There are advantages of redundant actuated
robots such as improvement of Cartesian stiffness
within the worspace, homogeneous symmetric force
output and a need for optimization due to the fact
that the dynamic equations are indeterminate (Cheng
et al., 2001).
Recently, the BlueWorkforce company (Hjørnet,
2016) developed a new industrial redundant PKM
(The Ragnar Robot) with an optimized extended
workspace and relatively low price. By optimizing
the mechanical design and force transmission it was
possible to change materials and reduce costs.
The motivation behind the work presented in this
paper is to introduce compliant motion control in re-
dundantly actuated PKMs such as the Ragnar robot
for optimization to perform different compliant mo-
tion tasks in a manufacturing environment.
In this paper, we proposed an impedance con-
troller for a redundant parallel manipulator by setting
a desired stiffness and damping for each coordinate
axis in the cartesian space. The proposed method
considers every limb as a separate system. Limb dy-
104
Mendez, J., Schiøler, H., Madsen, O. and Bai, S.
Impedance Control of a Redundant Parallel Manipulator.
DOI: 10.5220/0006433301040111
In Proceedings of the 14th International Conference on Informatics in Control, Automation and Robotics (ICINCO 2017) - Volume 1, pages 104-111
ISBN: 978-989-758-263-9
Copyright © 2017 by SCITEPRESS – Science and Technology Publications, Lda. All r ights reserved