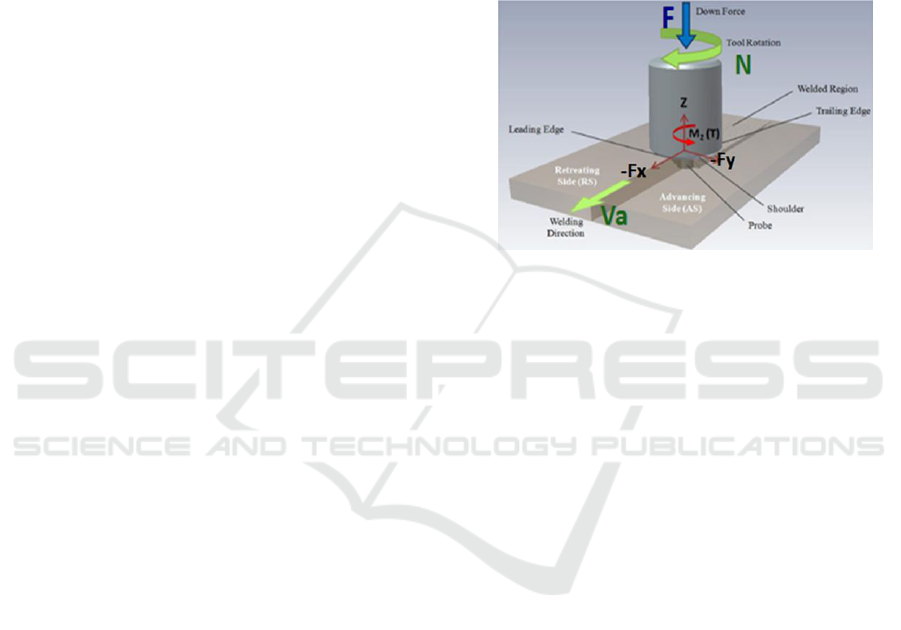
path has to be realized and many places have to be
reached by the tool. This flexibility of application is
best done by a serial robot. Although In recent years,
current researchers tried to replace the dedicated ma-
chines by serial robots due to their low cost. The idea
in this paper is to use an industrial serial robot to per-
form the friction stir welding process (FSW).
Due to the high thrust force required for FSW, gener-
ally a heavy industrial robot uses to perform the pro-
cess. Usually, the heavy industrial robots are consid-
ered among rigid structures, this condition remains
valid unless the forces needed to be created by the
robot do not exceed its carrying capacity, which is
not the case such as this process requires a very high
thrust force that must be provided by the serial robot
to hold the contact between the tool and the workpiece
surface. For example, to assemble two pieces of alu-
minum with 6 mm depth, we need 10 kN. For that rea-
son, its positioning accuracy becomes very low, when
the effect of transmission elasticity is non-negligible.
The deformation of the whole industrial robot needs
to be considered especially, for applications that re-
quire a precise position of the tool as described by
(Soron, 2008) and (Voellner et al., 2007), as in our
case, it is necessary that the tool follow a defined tra-
jectory. Therefore, this deformation makes deflection
in each joint of the robot, which causes an error in
following a given trajectory, see (Strombeck et al.,
2000) and affects evidently the quality of the weld.
The magnitude of this error depends on the robot po-
sition in the work space and the direction of welding
(Voellner et al., 2007), (Zaeh and Voellner, 2010) and
(Qin et al., 2014). The deviation error can be reduced
by solving this difficulty. Several work on manipula-
tor control has been developed to correct the deviation
of the robot tool (Yoshikawa, 2000), (Chiaverini et al.,
1994), (Raibert and Craig, 1981), et (De Luca et al.,
1989). However, there is always a lack of precision,
for this reason, in this work, an assistance device has
been associated to an industrial robot.
The static performance and the stiffniss of an indus-
trial robot can be greatly improved by adding a device
in form of a parallel structure.This assisting device
has the architecture of a parallel structure but it is not
an existing parallel robot. It is just tree thrust branches
able to create together very high thrust forces on the
tool which can be controlled easily. In this paper we
develop an optimization algorithm to minimize the
deviation error. For the first time this algorithm allows
the optimization of the parameters defined the paral-
lel structure. In the second time, the optimization of
the three forces created by this structure. Thereafter,
we simulated the workspace of the whole structure to
have an idea about its flexibility of the applications.
2 FSW PROCESS
As shown in Fig. 1 the rotating tool used for the FSW
process consists of a probe and a shoulder. Moreover,
the external forces exerted on it are the thrust force F
exerted by the FSW machine, F
x
the axial force dur-
ing welding when the tool advances along the joint
line the material’s resistance generates a force along
x
0
and Fy, then during tool rotation the flow of mate-
rial pushes the tool which generates a force along y
0
.
Figure 1: Princible of the FSW Process (Gibson et al.,
2014).
FSW is typically described in three steps. The
first step is plunging. Here, the probe penetrates into
the weld joint between the two parts to be assembled.
This step stops when the shoulder touches the surface.
The second step is welding. It involves the rotation of
the tool and needs a high force which locally softens
and mixes the material. This process assists the ad-
vance of the tool along the welding line (Fuller 2007,
2007). The third step is retraction; in this step the
probe is pulled out vertically from the material.
The FSW process is defined by four parameters,
the thrust force F, the welding speed Va, the rotation
speed N and the tilt angle B. The force is necessary for
maintaining contact between the tool and the pieces
to be welded. Further, it softens the material in or-
der to assist the penetration of the probe into the joint.
N and Va describe how fast the tool traverses along
the interface and rotates, respectively. These two tool
speeds have considerable importance, and therefore
they need to be correctly set to get a successful weld-
ing cycle. There is a relationship between the heat
input, the rotation speed and the welding speed dur-
ing welding. It is arguable that decreasing the lat-
eral speed or increasing the rotation speed will cause
a hotter weld. FSW is characterized by a slower Va
comparing to other welding processes. The last pa-
rameter is B, it tilts the tool mostly between 1.5
◦
and
3.5
◦
degrees such that the front of the tool is higher
than the rear. This inclination assists to forge the ma-
terial. See (Balasubramanian, 2009). To use this pro-
Parallel Robot Structure Optimizations for a Friction Stir Welding Application
373