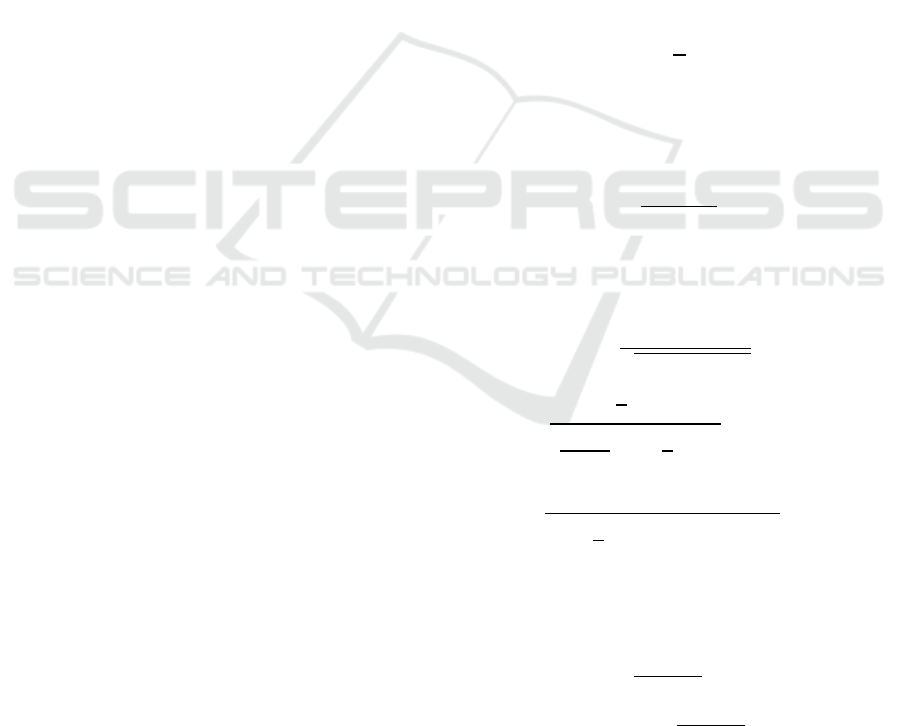
REFERENCES
Bathe, K-J., 1996. Finite Element Procedures. Prentice-
Hall, Inc., New Jersey.
Busch, M., 2012. Zur Effizienten Kopplung von
Simulationsprogrammen. Dissertation in mechanical
engineering at the University Kassel, kassel university
press GmbH, Kassel.
Chung, G-J., Kim, D-H., 2010. Structural Analysis of
600Kgf Heavy Duty Handling Robot. In 2010 IEEE
Conference on Robotics, Automation and
Mechatronics, pp. 40-44.
Dietz, S., Hippmann, G., Schupp, G., 2001. Interaction of
Vehicles and Flexible Tracks by Co-Simulation of
Multibody Vehicle Systems and Finite Element Track
Models. In The Dynamics of Vehicles on Roads and
Tracks, 37, pp. 372-384, Swets & Zeitlinger, 17th
IAVSD Symposium, Denmark.
Hearn, E.J., 1997. Mechanic of Materials 1. Third Edition,
Butterworth-Heinemann, Oxford, Woburn, pp. 299-
300.
Jung, T. J., 2011. Methoden der Mehrkörper-
dynamiksimulation als Grundlage realitätsnaher
Virtueller Welten. Dissertation at RWTH Aachen
University, Departement for Electrical Engineering
and Information Technology.
Kono, D., Lorenzer, Th., Wegener, K., 2010. Comparison
of Rigid Body Mechanics and Finite Element Method
for Machine Tool Evaluation. Eidgenössische
Technische Hochschule Zürich, Institut für Werkzeug-
maschinen und Fertigung.
Michalczyk, K., 2009. Analysis of helical compression
spring support influence on its deformation. In The
Archive of mechanical Engineering, Vol LVI, Number
4, pp. 349-362.
Rieg, F., Steinhilper, R., (Hrsg) 2012. Handbuch
Konstruktion. Carl Hanser Verlag München, Wien, pp.
849-857.
Roßmann, J., Schluse, M., Schlette, C., Waspe, R., 2013.
A New Approach to 3D Simulation Technology as
Enabling Technology for eRobotics. In Van Impe, Jan
F.M and Logist, Filip (Eds.): 1st International
Simulation Tools Conference & Expo 2013,
SIMEX’2013.
Stettinger, G., Benedikt, M., Thek, N., Zehetner, J., 2013.
On the difficulties of real-time co-simulation. In V
International Conference on Computational Methods
for Coupled Problems in Science and Engineering,
Coupled Problems, S. Idelsohn, M. Papadrakakis,
B.Schrefler (Eds.).
Stettinger, G., Horn, M., Benedikt, M., Zehetner, J., 2014.
Model-based Coupling Approach for non-iterative
Real-Time Co-Simulation. Conference paper European
Control Conference (ECC), France.
Stewart, D., Trinkle, J.C., 2000. An Implicit Time-Stepping
Scheme for Rigid Body Dynamics with Coulomb
Friction. ICRA.
Wang, X., Mills, J.K., 2004. A FEM Model for Active
Vibration Control of Flexible Linkages. In
Proceedings of the 2004 IEEE International
Conference on Robotics and Automation, New
Orleans, LA, pp. 4308-4313.
Weise, J., Brieß, K., Adomeit, A., Reimerdes, H.-G.,
Göller, M., Dill-mann, R., 2012. An Intelligent
Building Blocks Concept for On-Orbit-Satellite
Servicing. In Proceedings of the International
Symposium on Artificial Intelligence, Robotics and
Automation in Space (iSAIRAS), Turin (Italy).
Wellmer, G., 2014. Ein partitioniertes Verfahren für die
aeroelastische Freiflugsimulation. Einreichung zum
Deutschen Luft- und Raumfahrtkongress 2014, Docu-
mentID: 340310.
APPENDIX
The spring constant of a compression spring can
be defined in two ways. First, it can be done
experimentally by using the linear relation between
the compression and the force:
On the other hand, it can be calculated using
certain material criteria and manufacturing
parameters ((Hearn, 1997), see Table 1 for definition
of the variables):
The rotation of a compression spring is
described and validated in (Michalczyk, 2009).
In this equation, the total length of the wire
and the slope angle were defined.
The manufacturing parameters of the spring
modelled for the validation were taken from a usual
SIMULTECH 2017 - 7th International Conference on Simulation and Modeling Methodologies, Technologies and Applications
124