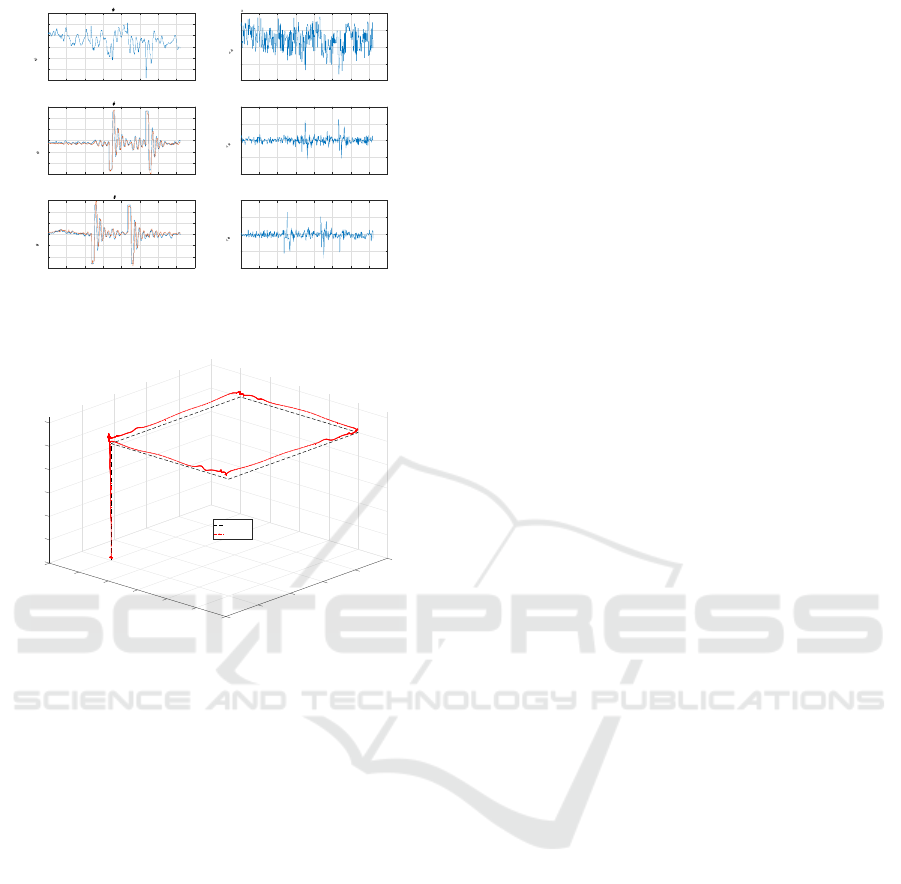
0 500 1000 1500 2000 2500 3000 3500 4000
time in (ms)
-0.02
0
0.02
0.04
0.06
0.08
0.1
YAW( ) angle in radians
YAW( ) PD controller
0 500 1000 1500 2000 2500 3000 3500 4000
time in (ms)
-15
-10
-5
0
5
Nm
10
-3
YAW Torque control
0 500 1000 1500 2000 2500 3000 3500 4000
time in (ms)
-0.3
-0.2
-0.1
0
0.1
0.2
0.3
ROLL( ) angle in radians
ROLL( ) PD controller
0 500 1000 1500 2000 2500 3000 3500 4000
time in (ms)
-0.1
-0.05
0
0.05
0.1
Nm
ROLL Torque control
0 500 1000 1500 2000 2500 3000 3500 4000
time in (ms)
-0.3
-0.2
-0.1
0
0.1
0.2
0.3
PITCH( ) angle in radians
PITCH( ) PD controller
0 500 1000 1500 2000 2500 3000 3500 4000
time in (ms)
-0.1
-0.05
0
0.05
0.1
Nm
PITCH Torque control
Figure 9: Real Torques and desired angles ROLL, PITCH
and YAW with a BS controllers.
1
0
-2.5
0.2
0.5
-2
0.4
0.6
X-Y-Z trajectory BS controller
-1.5
0
Z position in metres
Y position in metres
0.8
X position in metres
-1
-0.5
1
-0.5
1.2
-1
0
-1.5
0.5
Desired Trajectory
Trajectory
Figure 10: Real 3D trajectories using a BS controllers.
the other hand for positioning control the control al-
gorithms were developed under C++ and ROS, which
allow us to create a network where the ground sta-
tion, robots and sensors can exchange information at
120 Hz. The Drone performance was tested using
an square trajectory with 2 metres side, which was
enough to move the desired roll and pitch angles and
see their control response with the PD controller. The
desired angles was reached within a short period of
time, for instance 0.25 rad in 100 ms on the experi-
mental results for roll angle as figure 6 shows. Re-
garding positioning control, a linear PD controller and
a non linear Backstepping controller were tested, get-
ting a better response for X and Y position with the
Backstepping controller in figure 8 than the PD in fig-
ure 5, whereas for the altitude Z the PD controller had
a quicker response compared with BS as shown in fig-
ures 7 and 10.
REFERENCES
Bouabdallah, S. and Siegwart, R. (2005). Backstepping and
sliding-mode techniques applied to an indoor micro
quadrotor. Proceedings - IEEE International Confer-
ence on Robotics and Automation, 2005(April):2247–
2252.
Campbell, J., Hamilton, J., Iskandarani, M., and Givigi, S.
(2012). A systems approach for the development of a
quadrotor aircraft. In SysCon 2012 - 2012 IEEE In-
ternational Systems Conference, Proceedings, pages
110–116.
Castillo, P., Lozano, R., and Dzul, A. (2005). Stabilization
of a mini rotorcraft with four rotors: Experimental
implementation of linear and nonlinear control laws.
IEEE Control Systems Magazine, 25(6):45–55.
Corona-Sanchez, J. J. and Rodriguez-Cortes, H. (2013). Ex-
perimental real-time validation of an attitude nonlin-
ear controller for the quadrotor vehicle. In 2013 Inter-
national Conference on Unmanned Aircraft Systems,
ICUAS 2013 - Conference Proceedings, pages 453–
460.
Das, A., Lewis, F., and Subbarao, K. (2009). Backstepping
approach for controlling a quadrotor using lagrange
form dynamics. Journal of Intelligent and Robotic
Systems: Theory and Applications, 56(1-2):127–151.
Gomes, L. L., Leal, L., and Oliveira (2016). Unmanned
quadcopter control using a motion capture system.
IEEE Latin America Transactions, 14(8):3606–3613.
Khatoon, S., Gupta, D., and Das, L. K. (2014). Pid &
lqr control for a quadrotor: Modeling and simulation.
Proceedings of the 2014 International Conference on
Advances in Computing, Communications and Infor-
matics, ICACCI 2014, pages 796–802.
Kim, P. (2010). Kalman Filter for Beginners with MATLAB
Examples. A-JIN, Republic of Korea, 1 edition.
Mashood, A., Mohammed, M., Abdulwahab, M., Abdul-
wahab, S., and Noura, H. (2016). A hardware setup
for formation flight of uavs using motion tracking sys-
tem. In ISMA 2015 - 10th International Symposium on
Mechatronics and its Applications.
Reyes-Valeria, E., Enriquez-Caldera, R., Camacho-Lara, S.,
and Guichard, J. (2013). Lqr control for a quadrotor
using unit quaternions: Modeling and simulation bt -
electronics, communications and computing (coniele-
comp), 2013 international conference on. pages 172–
178.
Runcharoon, K. and Srichatrapimuk, V. (2013). Slid-
ing mode control of quadrotor. 2013 International
Conference on Technological Advances in Electrical,
Electronics and Computer Engineering (TAEECE),
(1):552–557.
Saif, A. A. H. (2009). Quadrotor control using feedback
linearization with dynamic extension. 2009 6th Inter-
national Symposium on Mechatronics and its Applica-
tions, ISMA 2009, (1):25–27.
Zheng, H., Zeng, Q., Chen, W., Zhu, H., and Chen, C.
(2016). Improved pid control algorithm for quadrotor
based on mcs. In Proceedings of 2016 IEEE Chinese
Guidance, Navigation and Control Conference, num-
ber 1, pages 1780–1783, Nanjin, China.
Real-Time Setup with PD and Backstepping Control for a Pelican Quadrotor
681