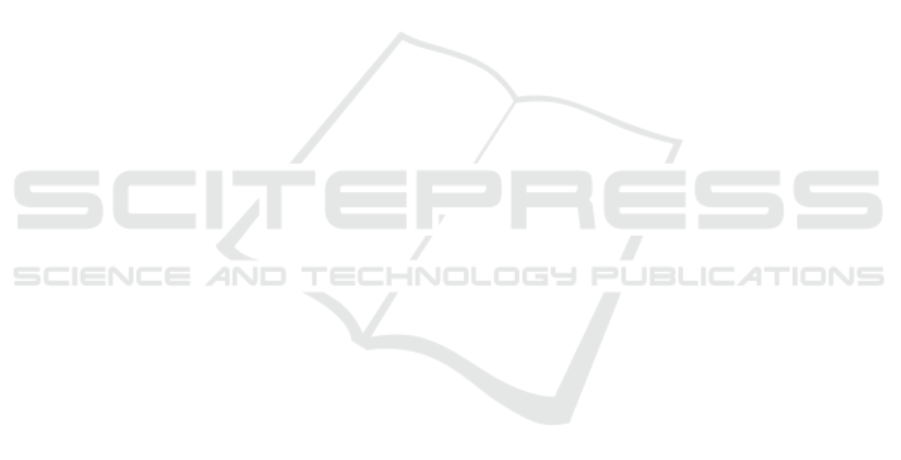
control the robot path. No localization are required
with the proposed method. In addition a stability anal-
ysis of those controllers and simulations highlighting
the efficiency of our approach have been provided. In
a second step, we have embedded them in a complete
navigation strategy allowing to navigate through an
orchard. We have explained how the different data
necessary for the control are derived, how the environ-
ment is modeled and how the robot is controlled using
the appropriate controllers. Finally a complete simu-
lation using ROS and Gazebo shows the efficiency of
the chosen approach in our agricultural context. The
next step of our work is to implement the controllers
on the Toro workman MDE robot. Finally, we also
plan to develop this sensor-based approach and take
advantage of its reactivity in order to navigate in a
dynamic environment.
REFERENCES
Bak, T. and Jakobsen, H. (2004). Agricultural robotic plat-
form with four wheel steering for weed detection.
Biosystems Engineering, 87(2):125–136.
Barawid, O. C., Mizushima, A., Ishii, K., and Noguchi,
N. (2007). Development of an autonomous naviga-
tion system using a two-dimensional laser scanner
in an orchard application. Biosystems Engineering,
96(2):139–149.
Bayar, G., Bergerman, M., Koku, A. B., and ilhan Konuk-
seven, E. (2015). Localization and control of an au-
tonomous orchard vehicle. Computers and Electron-
ics in Agriculture, 115:118–128.
Boyadzhiev, K. N. (1999). Spirals and conchospirals in the
flight of insects. The College Mathematics Journal,
30(1):21–31.
Durand-Petiteville, A., Cadenat, V., and Ouadah, N. (2015).
A complete sensor-based system to navigate through
a cluttered environment. In Informatics in Control,
Automation and Robotics (ICINCO), 2015 12th Inter-
national Conference on, volume 2, pages 166–173.
IEEE.
Eaton, R., Katupitiya, J., Siew, K. W., and Howarth, B.
(2009). Autonomous farming: Modelling and control
of agricultural machinery in a unified framework. In-
ternational journal of intelligent systems technologies
and applications, 8(1-4):444–457.
Fang, H., Fan, R., Thuilot, B., and Martinet, P. (2006).
Trajectory tracking control of farm vehicles in pres-
ence of sliding. Robotics and Autonomous Systems,
54(10):828–839.
Foley, J. A., Ramankutty, N., Brauman, K. A., Cassidy,
E. S., Gerber, J. S., Johnston, M., Mueller, N. D.,
O’Connell, C., Ray, D. K., West, P. C., Balzer, C.,
Bennett, E. M., Carpenter, S. R., Hill, J., Monfreda,
C., Polasky, S., Rockstr
¨
om, J., Sheehan, J., Siebert,
S., Tilman, D., and Zaks, D. P. M. (2011). Solutions
for a cultivated planet. Nature, 478:337–342.
Futterlieb, M., Cadenat, V., and Sentenac, T. (2014). A Nav-
igational Framework Combining Visual Servoing and
Spiral Obstacle Avoidance Techniques. In Interna-
tional Conference on Informatics in Control, Automa-
tion and Robotics ( ICINCO ) , pages 57–64, Vienna,
Austria. INSTICC.
Hansen, S., Bayramoglu, E., Andersen, J. C., Ravn, O., An-
dersen, N., and Poulsen, N. K. (2011). Orchard navi-
gation using derivative free kalman filtering. In Amer-
ican Control Conference (ACC), 2011, pages 4679–
4684. IEEE.
Johnson, D. A., Naffin, D. J., Puhalla, J. S., Sanchez, J., and
Wellington, C. K. (2009). Development and imple-
mentation of a team of robotic tractors for autonomous
peat moss harvesting. Journal of Field Robotics, 26(6-
7):549–571.
Mcfadyen, A., Durand-Petiteville, A., and Mejias, L.
(2014). Decision strategies for automated visual col-
lision avoidance. In Unmanned Aircraft Systems
(ICUAS), 2014 International Conference on, pages
715–725.
Reid, J. (2011). The impact of mechanization on agricul-
ture. Nat. Acad. Eng. Bridge, Issue Agric. Inf. Tech-
nol., 41(3):22–29.
Siciliano, B. and Khatib, O. (2016). Springer handbook of
robotics. Springer.
Zhang, J., Maeta, S., Bergerman, M., and Singh, S. (2014).
Mapping orchards for autonomous navigation. In
Proc. American Society of Agricultural and Biologi-
cal Engineers Annu. Int. Meeting.
Design of a Sensor-based Controller Performing U-turn to Navigate in Orchards
181