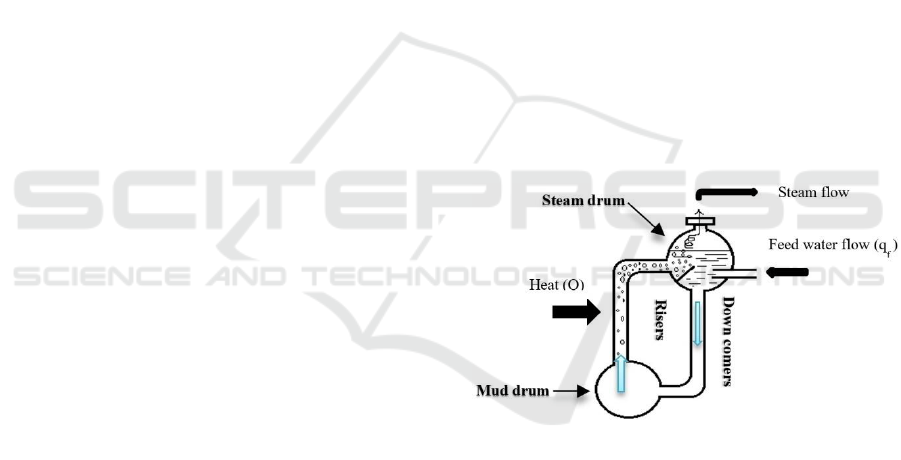
as combination of conventional single variable
control loops and computation of variables that
cannot be measured directly (Balchen & Mumme,
1988). Advanced control techniques have also been
proposed to improve the performance of the control
system in comparison of a decentralized one (Tan, et
al., 2004). More complex and robust methodologies
such as LQG/LTR, H∞-control, predictive control,
and fuzzy control, have been also applied to improve
boiler performance (Tan, et al., 2005) in specific
cases. Based on (Sanjoy Kumar Chakraborty,
Nilotpal Manna and Surodh Dey, April 2014) the
importance of three-elements boiler drum level
control has been presented. From (Keyur Solanki,
Jalpa Shah, Nishith Bhatt, 2014), we can also prove
previous assumption on the level control scheme
based on the 3-element controller.
In this paper an adaptive control strategy will be
proposed to cope with nonlinearity of the boiler while
regulating its process characteristics on the desired
value. The whole procedure is done based on the
following pillars. First, a mathematical description is
provided through a nonlinear model for steam drum
of a D-type water tube boiler with natural circulation.
The model is derived from first principle modelling
method and is based on physical principles and
construction data. To validate the model, some real
data from a specific boiler have been considered and
used to tune the mdoel according to the classic grey-
box approach. Second, to compensate the
nonlinearities of the model, we divide the whole
operating range into several smaller ranges where the
process can be approximated by linear models. By
using system identification techniques, it is possible
to obtain many black-box models of the system,
linearized around various working conditions. Each
black-box model is only valid closed to its
corresponding operating point. Then, a specific
controller (a PID for compliance with the market) is
designed for each working point. Finally, two
adaptive techniques have been conveived and tested:
a gain-scheduling one and an adaptive one based on
interpolation approaches.
2 MODEL DESCRIPTION
2.1 D-type Water Tube Boiler
As a general working principles of D-type water tube
boiler, tubes are used to convey water and steam
through the boiler. The combustion gases flow pass
the outside surfaces of the tubes. The simplified
sketch of D-type water tube boiler configuration is
shown in Figure1. This boiler consists of a series of
tubes and two drums (upper and lower ones). Drums
distribute water to the tubes and these water tubes
connect the drums and form a wall around the
combustion area, where the heat is generated. Water
is transferred into the upper drum through a feed
water inlet line. The water tubes which is called
‘down comers’ and the lower drum is filled
completely with water and the upper drum is only
filled with water to a certain level to provide space for
the steam. The upper drum is called ‘steam drum’. As
fuel is burned in combustion area, heat is transferred
to the adjacent tubes named ‘risers’. Water circulate
from steam drum through down comers and into the
lower drum.
Lower drum is referred to as the ‘mud drum’.
From mud drum, water is distributed to the risers
surrounding the combustion area. Water in risers is
heated and steam-water mixture is produced and
enters the steam drum. Steam is separated from water
and goes to the steam outlet and eventually into the
plant.
Steam drum has a very complex mechanism and
it has a tricky behaviour. In this project, the main
focus is on the designing the suitable control system
for steam drum.
Figure 1: D-type water tube boiler.
2.2 Nonlinear Dynamic Model of Steam
Drum Boiler
A key property of boilers is that there is a very
efficient heat transfer due to boiling and
condensation. All parts of the system which are in
contact with the saturated water-steam mixture will
be considered in thermal equilibrium. Energy stored
in steam and water is released or absorbed very
rapidly when the pressure changes. This mechanism
is the key for understanding boiler dynamics. The
rapid release of energy ensures that different parts of
the boiler change their temperature in the same way
(K.J. Åström, R.D. Bell, 2000).
ICINCO 2017 - 14th International Conference on Informatics in Control, Automation and Robotics
366