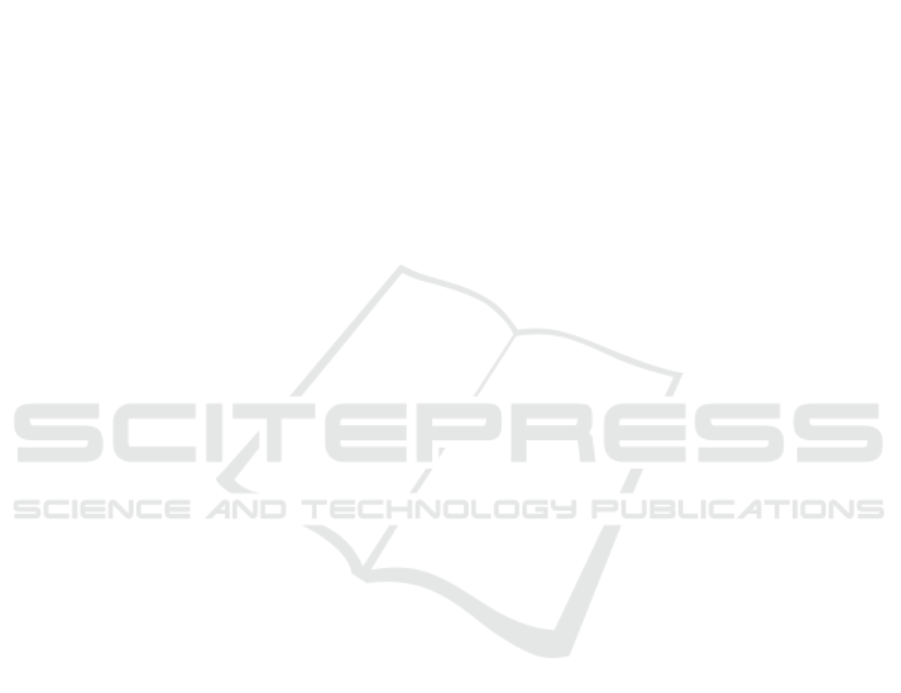
Investigation of Three Immiscible Fluids in a Microchannel
Accounting for the Pressure Gradient and the Electroosmotic Flow
Nicolas La Roche-Carrier, Guyh Dituba Ngoma, Fouad Erchiqui and Ibrahim Hamani
School of Engineering’s Department, University of Quebec in Abitibi-Témiscamingue,
445, Boulevard de l’Université, Rouyn-Noranda, Quebec, J9X 5E4, Canada
Keywords: Immiscible Fluids, Microchannel, Modeling and Simulation.
Abstract: This study deals with the investigation of three immiscible fluids in a microchannel consisting of two parallel
plates. These fluids were composed of two electric conducting fluids and one electric nonconducting fluid.
The concept of pumping a nonconducting fluid using interfacial viscous shear stress was applied accounting
for the effect of the electroosmosis and pressure gradient. The electric potential and the flow parameters were
found resolving the Poisson-Boltzmann equation and the modified Navier-Stokes equations for a hydraulic
steady fully-developed laminar flow of an incompressible fluid. The results achieved revealed the influence
of the wall and interfacial zeta potentials, the pressure difference, and the dynamic fluid viscosity ratio on the
flow characteristics of the three immiscible fluids. The developed approach was compared with a model of
two immiscible flows to highlight the relevance of this work.
1 INTRODUCTION
Microfluidic transport is widely used in the fields of
micropumps, micropower generation, chemical
processes, biomechanical processes and heat transfer,
where surface effects dominate the flow behavior
within microdevices (Dituba Ngoma G. et al., 2005).
The precise knowledge of the immiscible fluids flow
behavior in microchannels is essential to develop
high-performance microfluidic devices to pump a
nonconducting fluid by means of conducting fluids.
This can be achieved taking relevant fluid parameters
and microchannel configurations into consideration
in the planning, design and optimization phases. Most
previous investigations of pressure gradient and
electroosmotic flow in microchannels were
performed using a single conducting fluid with the
zeta potentials at the microchannel walls (Dhinakaran
S. et al., 2010; Vainshtein P. et al., 2002; and Brask
A. et al., 2005). There, the effects of surface potential,
electric field, ionic concentration and channel size on
the velocity distribution and the effect of friction on
flow characteristics. Furthermore, Yong et al., 2011
numerically analyzed the immiscible kerosene-water
two-phase flows in microchannels connected by a T-
junction using lattice Boltzmann method. In addition,
Dituba Ngoma G. et al., 2005; and Gao Y. et al., 2005,
conducted a study on two immiscible fluids
consisting of a conducting fluid and a nonconducting
fluid in a microchannel. The electric field and the
pressure gradient were applied. Moreover, an
analytical model of mixed electroosmotic/pressure
driven three immiscible fluids in a rectangular
microchannel was developed by Li H. et al., 2009.
They analyzed the effects of viscosity ratio,
electroosmosis and pressure gradient on velocity
profile and flow rate. Thorough analysis of previous
works clearly demonstrated that the research results
obtained are specific to the microchannel
configuration depending on considered key
parameters of fluids and microchannels. Therefore,
in this work, to enhance the fluid flow of
nonconducting fluids and performances of the flow in
microchannels, an investigation was conducted
considering the fluid flow of the three immiscible
fluids in a two parallel plates to deeply analyze the
impacts of the zeta potential, the pressure difference
and the dynamic viscosity on the flow characteristics
of the three fluids.
428
Roche-Carrier, N., Ngoma, G., Erchiqui, F. and Hamani, I.
Investigation of Three Immiscible Fluids in a Microchannel Accounting for the Pressure Gradient and the Electroosmotic Flow.
DOI: 10.5220/0006481004280433
In Proceedings of the 7th International Conference on Simulation and Modeling Methodologies, Technologies and Applications (SIMULTECH 2017), pages 428-433
ISBN: 978-989-758-265-3
Copyright © 2017 by SCITEPRESS – Science and Technology Publications, Lda. All rights reserved