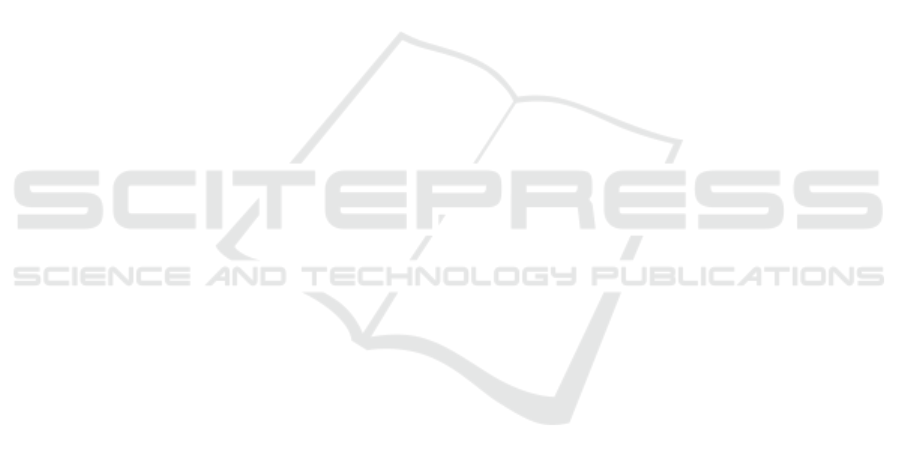
and other solution strategies for the DVRP (Psaraftis
et al., 2016) need to be adapted to the proposed dy-
namic real-time VRP-environment to ensure compa-
rability. The gathered insights can then be used to
gain optimization performance.
REFERENCES
AbdAllah, A. M. F., Essam, D. L., and Sarker, R. A. (2017).
On solving periodic re-optimization dynamic vehicle
routing problems. Applied Soft Computing, 55:1–12.
Barkaoui, M. and Gendreau, M. (2013). An adaptive
evolutionary approach for real-time vehicle routing
and dispatching. Computers & Operations Research,
40(7):1766–1776.
Bektas, T., Repoussis, P., and Tarantilis, C. (2014). Dy-
namic vehicle routing problems. In Toth, P. and Vigo,
D., editors, Vehicle routing, MOS-SIAM series on op-
timization, pages 299–347. Society for Industrial and
Applied Mathematics and Mathematical Optimization
Society, Philadelphia.
Branke, J., Middendorf, M., Noeth, G., and Dessouky, M.
(2005). Waiting strategies for dynamic vehicle rout-
ing. Transportation Science, 39(3):298–312.
Chiang, Y.-S. and O. Roberts, P. (1980). A note on transit
time and reliability for regular-route trucking. Trans-
portation Research Part B: Methodological, 14(1-
2):59–65.
Cr
´
eput, J.-C., Hajjam, A., Koukam, A., and Kuhn, O.
(2012). Self-organizing maps in population based
metaheuristic to the dynamic vehicle routing problem.
Journal of Combinatorial Optimization, 24(4):437–
458.
Elhassania, M., Jaouad, B., and Ahmed, E. A. (2014). Solv-
ing the dynamic vehicle routing problem using ge-
netic algorithms. In 2014 International Conference on
Logistics and Operations Management (GOL), pages
62–69.
Gan, Z., Tao, L., and Ying, Q. (2013). Automated guide ve-
hicles dynamic scheduling based on annealing genetic
algorithm. Indonesian Journal of Electrical Engineer-
ing and Computer Science, 11(5):2508–2515.
Gehring, H. and Homberger, J. (1999). A parallel hy-
brid evolutionary metaheuristic for the vehicle rout-
ing problem with time windows: Jyv
¨
askyl
¨
a, finnland.
In Miettinen, K., M
¨
akel
¨
a, M., and Toivanen, J., ed-
itors, Proceedings of EU-ROGEN99, pages 57–64,
Jyv
¨
askyl
¨
a, Finnland.
Ghannadpour, S. F., Noori, S., and Tavakkoli-Moghaddam,
R. (2013). Multiobjective dynamic vehicle routing
problem with fuzzy travel times and customers’ sat-
isfaction in supply chain management. IEEE Trans-
actions on Engineering Management, 60(4):777–790.
Ghannadpour, S. F., Noori, S., Tavakkoli-Moghaddam, R.,
and Ghoseiri, K. (2014). A multi-objective dynamic
vehicle routing problem with fuzzy time windows:
Model, solution and application. Applied Soft Com-
puting, 14:504–527.
Haghani, A. and Jung, S. (2005). A dynamic vehicle routing
problem with time-dependent travel times. Computers
& Operations Research, 32(11):2959–2986.
Hanshar, F. T. and Ombuki-Berman, B. M. (2007). Dy-
namic vehicle routing using genetic algorithms. Ap-
plied Intelligence, 27(1):89–99.
Harik, G. (1995). Finding multimodal solutions using re-
stricted tournament selection. In Eshelman, L. J., edi-
tor, Proceedings of the Sixth International Conference
on Genetic Algorithms, pages 24–31. M. Kaufman,
San Francisco, Calif.
Ichoua, S., Gendreau, M., and Potvin, J.-Y. (2003). Vehicle
dispatching with time-dependent travel times. Euro-
pean Journal of Operational Research, 144(2):379–
396.
Liebermann, G. J., Hillier, F. S., Fackler, M., Bauer,
G., Honold, G., Michels, K.-N., Rehklau, U.,
and Weigert, M. (1997). Operations Research:
Einf
¨
uhrung. Internationale Standardlehrb
¨
ucher der
Wirtschafts- und Sozialwissenschaften. De Gruyter
Oldenbourg, M
¨
unchen, 5. aufl. edition.
Naumann, F. and Herschel, M. (2010). An introduction to
duplicate detection, volume #3 of Synthesis lectures
on data management. Morgan & Claypool Publishers,
San Rafael, Calif.
Pillac, V., Gendreau, M., Gu
´
eret, C., and Medaglia, A. L.
(2013). A review of dynamic vehicle routing prob-
lems. European Journal of Operational Research,
225(1):1–11.
Psaraftis, H. N., Wen, M., and Kontovas, C. A. (2016). Dy-
namic vehicle routing problems: Three decades and
counting. Networks, 67(1):3–31.
Ritzinger, U., Puchinger, J., and Hartl, R. F. (2015). A sur-
vey on dynamic and stochastic vehicle routing prob-
lems. International Journal of Production Research,
54(1):215–231.
Russell, R. A. and Urban, T. L. (2008). Vehicle routing with
soft time windows and erlang travel times. Journal of
the Operational Research Society, 59(9):1220–1228.
Tan, K. C., Chew, Y. H., and Lee, L. H. (2006). A hybrid
multiobjective evolutionary algorithm for solving ve-
hicle routing problem with time windows. Computa-
tional Optimization and Applications, 34(1):115–151.
Taniguchi, E. and Shimamoto, H. (2004). Intelligent trans-
portation system based dynamic vehicle routing and
scheduling with variable travel times. Transporta-
tion Research Part C: Emerging Technologies, 12(3-
4):235–250.