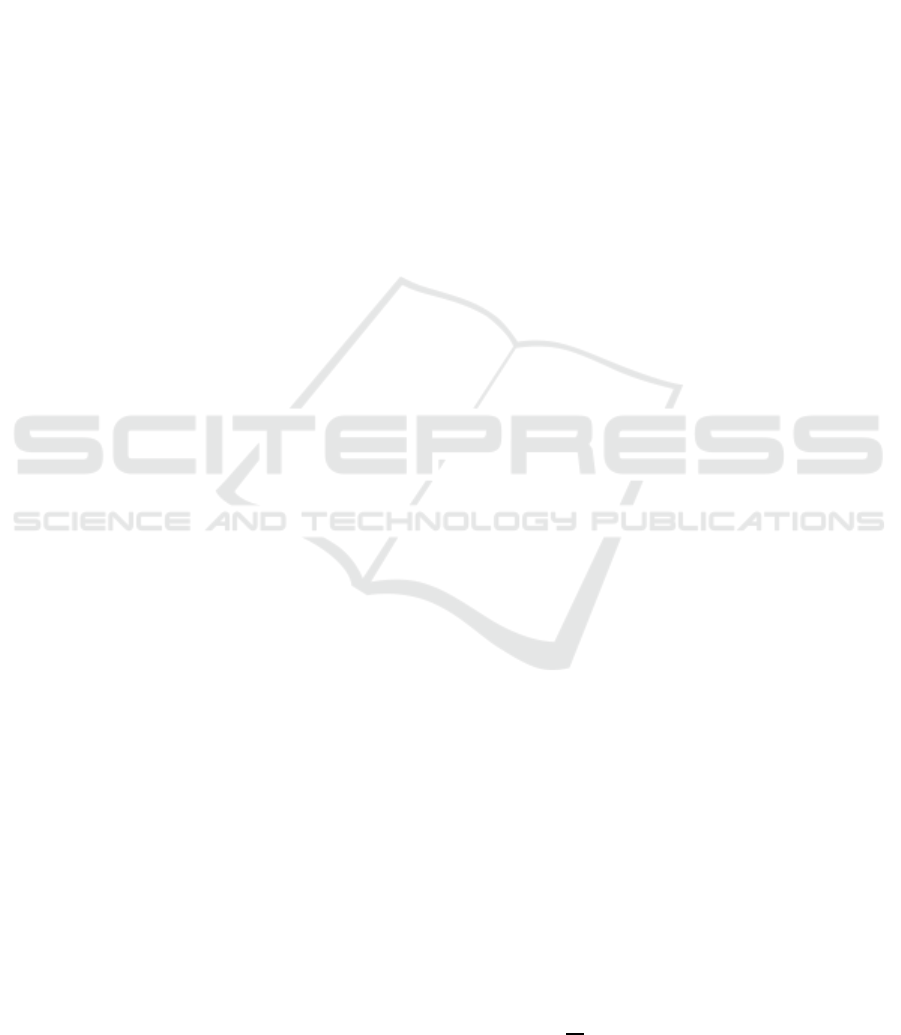
Numerical Simulation of Steady State Heat Distribution in Polymer
Concrete Heating with Aggregate Silica Sand and Shellfish
Lukman Hakim
1
and Fauzi
1
1
Department of Physics, Faculty of Mathematics and Natural Sciences, University of Sumatera Utara, USU Campus, Jalan
Bioteknologi No. 1 Medan, 20155, Indonesia
Keywords: Heat Transfer, Polymer Concrete, Simulation Numeric.
Abstract: Environmentally friendly polymer concrete by utilizing waste has been widely developed, one of which is
shellfish waste as filler and silica sand as aggregate. This study was to determine the numerical simulation of
heat distribution during the heating of polymer concrete with steady state with finite difference method of
concrete model polymer and to know thermal conduction characteristics micro . Variation in composition
made of silica sand , seashells (1: 1) or (50 gr: 50gr. Variations in the composition of epoxy resin 25% of the
total weight of sand and shells . The results of this simulation show that the maximum temperature of 80
0
C
is the maximum limit temperature in row one (1) column 2 to 7, row 7 column 2 to 7, and column 7. While
the temperature value of each node is 55 .0987
0
C is on elements (nodes) of five (5) and twenty-five (25).
While most small temperature values are at the nodes of eleven (11) with a value of 3.8333
0
C. heating time
is needed for 360 seconds. From the graph shows that the largest increase in the amount of temperature at
1800 seconds, while the time that shows steady state at 2160 seconds with a fixed value at 80
0
C
1 INTRODUCTION
Computational physics is one of the most important
groups of sciences because it can examine the form of
modeling of complex and complex equations solved
by a numerical approach (Lukman Hakim, 2014).
The finite element method is one of the numerical
methods used to solve equations Partial differential in
engineering science and mathematics problems such
as heat transfer, namely physical dividing complex
problems into elements to make it easier to get
solutions. Solution of each the element is then
combined so that it becomes a problem for the whole
problem (Vimala Rachmawati.,2015).
the research that will be discussed is heat transfer
by solving equations Numerical is the research that
describes the heat transfer elements that are presented
to capture thermal reactions in polymer concrete
which are numerically solved by the finite element
method. The construct equation is criticized into a
series of two-dimensional layers that are related to
finite difference calculations and use the function of
the form of quadrilateral elements (Vimala
Rachmawati.,2015).
Heating a material is the process of transferring
heat from a heat source in the form of a zinc plate
which is useful to find out how fast the heat is moving
and how much heat is occurring in each second. The
heat transfer process is the science of predicting
energy transfer that occurs due to temperature
differences between objects or materials. Steady
conduction heat transfer (steady state) is a conduction
process where the heat value (heat) is equal to time
(Halaudin, 2006).
Concrete is a construction material based on
cement adhesives and aggregates in the form of sand
and gravel (Calvelri, L, Miraglia, N, Papia, M. 2003).
One of the most influential material for polymer
building materials concrete the aggregate of silica
sand and seashell which is expected after testing this
thermal conductivity is having high heat conductivity,
high strength, resistance to corrosion and chemicals
(Shinta Marito, 2009).
Heat transfer in polymer concrete is conduction,
from high-temperature objects to low-temperature
objects that have conductivity properties. the thermal
productivity of a material is the size the ability of
materials to conduct heat (thermal).
Mathematically, the equation of heat distribution
by conduction is formulated:
(1)
Hakim, L. and Fauzi, .
Numerical Simulation of Steady State Heat Distribution in Polymer Concrete Heating with Aggregate Silica Sand and Shellfish.
DOI: 10.5220/0010103910911094
In Proceedings of the International Conference of Science, Technology, Engineering, Environmental and Ramification Researches (ICOSTEERR 2018) - Research in Industry 4.0, pages
1091-1094
ISBN: 978-989-758-449-7
Copyright
c
2020 by SCITEPRESS – Science and Technology Publications, Lda. All rights reserved
1091