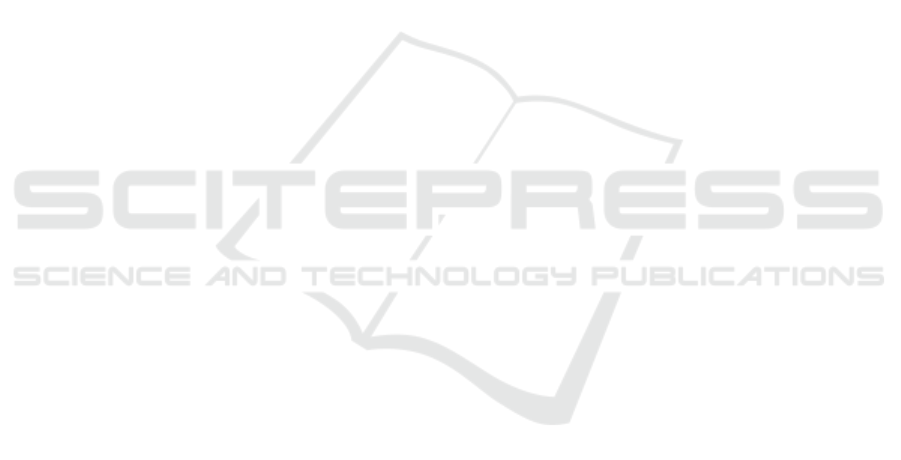
The far-field (Fraunhofer) distribution of
scattered optical power from this surface at angle
s
,
from an incident beam inclined at
i
, measured on a
detector subtending solid angle
d
, ranges from its
maximum at the angle of specular reflection
r
,
decreases gradually but not necessarily uniformly or
symmetrically, in ~ 2-steradians oriented (for
detection) in spherical coordinates about the axis of
the reflected beam, centred at the point of reflection
(Figure 1). Since for practicality,
i
is usually not
normal, the spot on the surface is not circular, and
must be accounted for if illuminated structure or
defects are large in comparison. The scatter power
measurement at non-normal angles is compensated
by a factor of (Cos
s
)
-1
to normalize the orientation
of the detector to the plane of the surface. The
altitudinal and azimuthal variation of the scattered
optical power about the specular axis need not
necessarily be regular or asymptotic, and in fact may
contain additional artefacts such as multiple
secondary maxima superimposed with power
fluctuations, uniform haze, and other variations.
The defect size, , and the roughness dimension,
',scaled in comparison to the wavelength,
determine the corresponding total 3D scatter
distribution (Bohren, 1998, Stover, 1995). There are
five zones of scaling, namely:
(І)
(І)
(І)
(І)
and
(І)
These can be restricted
to a few categories for precision surfaces. Scatter
from low spatial-frequency roughness (several
multiples of the optical wavelength; ') is present
in angular proximity to the specular reflection.
Microstructure containing higher spatial frequencies
(') scatters power at wider angles away from the
reflected beam. The scaling determines if the optical
path of scatter radiation is by direct reflection from
the surface or by instances or orders of multiple
reflections within the roughness, prior to impinging
on the detector. The power of the scattered
radiation, if scales with the sixth power of the
dimension of defects, and varies as
-4
. The non-
specular radiation at oblique angles is essentially
Rayleigh scatter produced by randomly oriented
sub-wavelength
(І)
defects, surface, and sub-
surface structure, and studied extensively by Church,
1979, and Stover, 1995. Indeed, scatter produced by
nanostructure, where ' is relatively minor (at multi-
lattice constant or multi-molecular dimensions) in
comparison with , is distributed uniformly over the
entire hemisphere, much as a Lambertian source,
and forms a noise-power baseline. The total power
distribution function may also contain Mie scatter
components from fractional to multi-wavelength
dimension defects (
(І)
), Rayleigh scatter from
sub-wavelength defects (), and a wide range of
features which additionally may be present on the
surface as texture, device patterns, debris, or damage
in a sub-surface region within an optical wavelength.
The remaining critical variables in defect and
artefact detection are the beam incidence angle and
its polarization, the scattering cross section, the spot
profile and size, and the detection arrangement. -
polarized light incident on a defect generates a
symmetric lobular altitudinal pattern oriented
orthogonal to the field, while-polarized light
illuminating a defect produces a uniform altitudinal
scatter distribution but is azimuthally lobular, i.e. a
90-degree rotation of the field. The beam
orientation and the positioning of detectors for
defect detection in the scattering plane is an
empirical art critically based on the selection of the
polarization of the incident beam to enhance high
defect-to-background contrast. For example, the
normal component of –polarization in near normal
incidence could be utilized to probe embedded
defects or voids with narrow oblique detection.
Similarly,-polarization may be useful to detect a
particle on a surface, where oblique incidence is
combined with wide normal detection. Additional
variables to consider are the specific defect shape
(usually not spherical), the defect material, whether
the defect resides on a dielectric or a conducting
surface, and the corresponding image charge
distributions. The operating wavelength may be
judiciously selected if the background surface, the
defect material, and the scatter thus produced are
reasonably well understood. The angular
distribution of scatter also suggests the utilization of
Fourier spatial filtering to distinguish scatter profiles
of a particular roughness range, device footprint, or
defect type, a technique widely in use in the
semiconductor industry to identify undesirable
defects on processed wafers.
Figure 2 shows representative angle-resolved
optical scatter data acquired at 633 nm on a polished
quartz optic, in which the logarithm of the relative
scatter produced is plotted versus the detector
(scatter) angle, which is varied from the incident
beam towards the specular reflected beam. The data
follows our discussion in the previous paragraph,
and the scatter power in relation to the surface
roughness spread is as indicated. The dynamic
range from the specular maximum power (flat
surface) to the scatter minimum power
(nanoroughness) is approximately 73 dB. The
specific scatter power for a defined roughness spread
at a prescribed angle could be resolved by
deliberately machining the corresponding structure
PHOTOPTICS 2018 - 6th International Conference on Photonics, Optics and Laser Technology
26