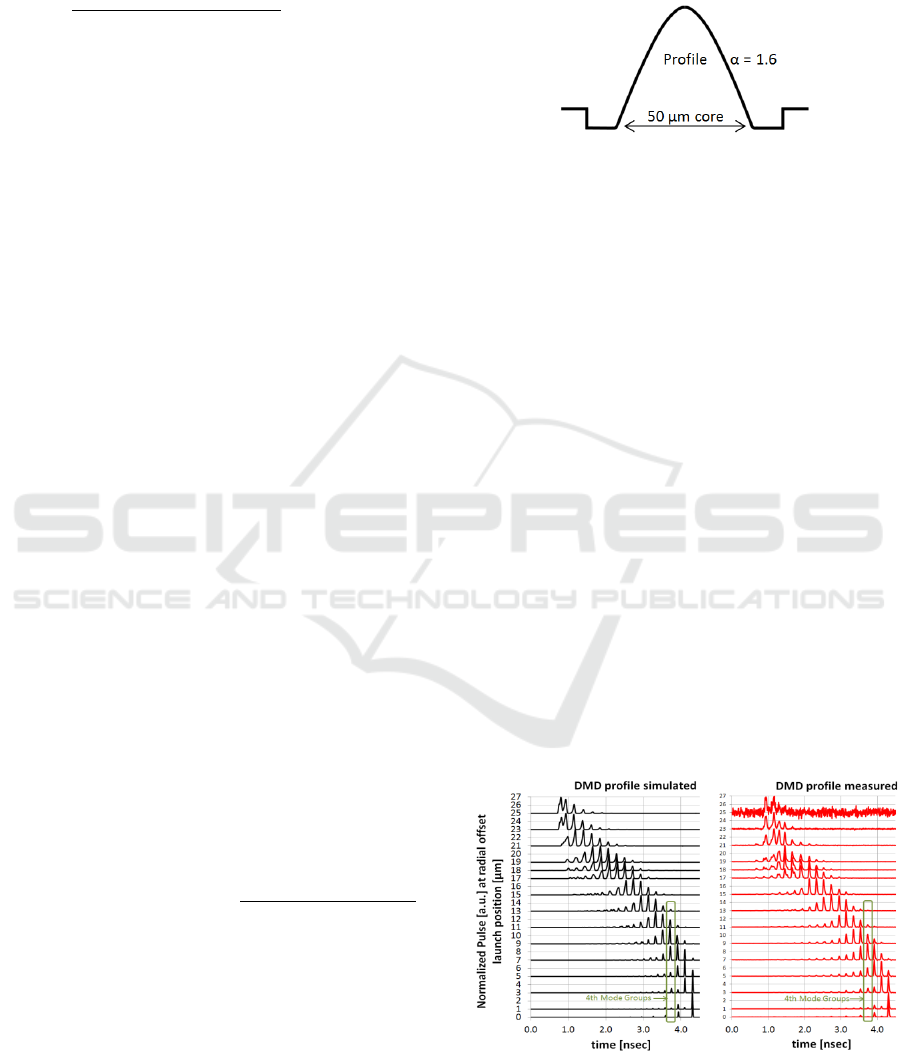
detector may consist of a tapered or lensed core. The
consequence of such a structure is some light will
leave the internal fibre pigtail from the side, and so it
will not reach the sensitive area of the detector. This
causes ‘selective mode detection’. Sometimes the
internal fibre pigtail is bended to fit the small
housing. This will introduce macrobend losses. As
far as we know, no commercial available detector
exists that uses a ‘bend insensitive’ fibre design as
the internal fibre pigtail. Another cause of selective
mode detection may be imperfections of the
sensitive area. If the detector suffers from selective
mode detection, the measured DMD profile of the
OM4 fibre under test is not theoretically correct, and
as a consequence the computed EMB value isn’t
correct either.
This paper describes a method to characterise a
detector, so it can be used to qualify OM4 fibre. The
method is tested on five different detectors from
different manufacturers. These detectors are all
specified for multimode fibre, with a very high
optical bandwidth of at least 10 GHz. A very high
bandwidth is mandatory to qualify short length of
OM4 fibre, for instance close to the maximum
system length of 400 m. All detectors are fibre
pigtailed with a 50 or 62.5 µm core Graded Index
fibre. Also a low bandwidth detector is used as a
reference. This detector cannot detect the individual
pulses (too slow), but can measure the power
distribution on a near DC level. Two of the used
detectors were developed for 850 nm pulse
measurement (so are not suited to qualify wide band
multimode fibres up to 950 nm). For now the
detectors are investigated at 850 nm, but the same
method (for the 950 nm sensitive detectors) can be
used for other wavelengths in the range 850 - 950 nm.
2 CHARACTERIZATION
METHOD
To characterize a detector, a special designed optical
fibre is used. Referred to as ‘mode separating fibre’.
Regular multimode fibres are designed with an
‘Alpha Profile’ refractive index core (Oh, 2012). If
the Alpha value (α) is optimized for a particular
wavelength (OM4: 850 nm), and the refractive index
profile is very accurate, the EMB reaches very high
values at that particular wavelength. This means all
launched modes reach the detector at the same time
after travelling through the fibre. The pulses are
shaped exactly equal as launched into the fibre
(assuming a short fibre length of max 1 km, so
Chromatic Dispersion effects can be neglected). A
typical value for α is 2.0. The special designed
optical fibre (‘mode separating fibre’) has an α of
1.6. The profile is shown in Figure 1.
Figure 1: refractive index profile of the special designed
fibre (’mode separating fibre’).
Because of the low α, the mode groups experience
different times of flight through the fibre. This can
be clearly seen on the resulting (normalized)
measured DMD profile of Figure 2b (used is a
Titanium Sapphire Mode Locked laser, 10 ps pulses,
850 nm). Figure 2a shows a simulated DMD profile
on an ‘ideal’ α = 1.6 fibre. The simulation model is
described in (Gholami, 2011). The method (and
equipment requirements) to get a fibre DMD profile
is described in detail in TIA and IEC documents
(TIA, 2003, IEC, 2017). The 18 mode groups reach
the fibre end at clear different moments in time. So
one can derive the positions in time of the mode
groups leaving the fibre, and the power of the pulses
present within each mode group launched at
different radial offset positions. If the α = 1.6 fibre is
‘perfect’ (equal to the input to the simulation
model), the difference between the detected DMD
profile and simulated DMD profile is a measure for
detector performance. The closer both DMD
profiles, the better detector performance (it then
detects all mode groups leaving the α = 1.6 fibre).
The used length of the α = 1.6 fibre (mode
separating fibre) is 550 m.
a b
Figure 2: simulated and measured DMD profile after 550
m of the ’α = 1.6 fibre’ (mode separating fibre). 18 Mode
Groups are visible and clearly separated in time.
PHOTOPTICS 2018 - 6th International Conference on Photonics, Optics and Laser Technology
142