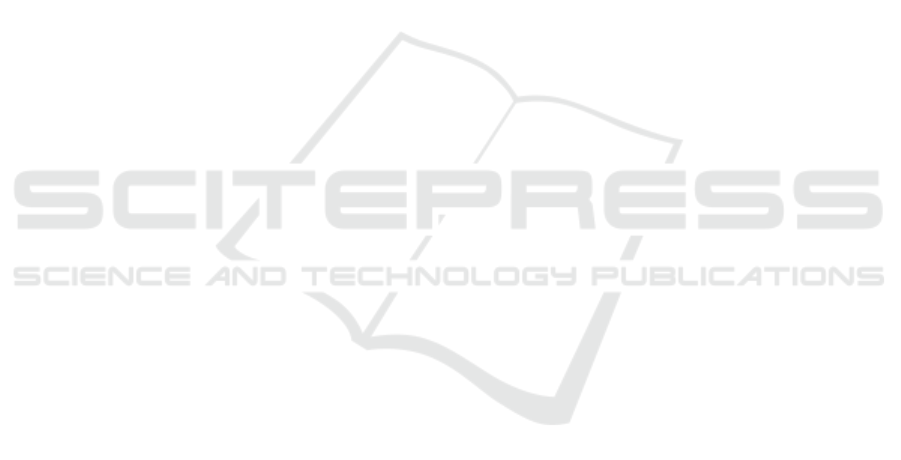
survival analysis to work, we need to either come up
with good measures to ensure data quality or to find
algorithms which can correct the problems.
However, in the light of recent developments such as
Industrie 4.0 and Industrial Internet, maybe the
alternative is to primarily rely on condition
monitoring data. Of course, this means that there will
be other data quality issues to be addressed and future
research is required.
REFERENCES
R. G. Miller 1997. Survival analysis, John Wiley & Sons.
J. Antoni, J.; R. B. Randall 2006. The spectral kurtosis.
Application to the vibratory surveillance and
diagnostics of rotating machines. In Mechanical
Systems and Signal Processing.
R. Gitzel, S. Turring and S. Maczey 2015. A Data Quality
Dashboard for Reliability Data. In 2015 IEEE 17th
Conference on Business Informatics, Lisbon.
R. Gitzel 2016. Data Quality in Time Series Data - An
Experience Report. In. Proceedings of CBI 2016
Industrial Track, http.//ceur-ws.org/Vol-
1753/paper5.pdf.
IEEE 2007. IEEE Standard 493 - IEEE Recommended
Practice for the Design of Reliable Industrial and
Commercial Power Systems.
S. Kunttu, J. Kiiveri 2012. Take Advantage of
Dependability Data, maintworld, 3/2012.
J.W. Hines, A. Usynin 2008. Current Computational Trends
in Equipment Prognostics. In International Journal of
Computational Intelligence Systems.
M. Salgado, W. M. Caminhas W.M; B. R. Menezes 2008.
Computational Intelligence in Reliability and
Maintainability Engineering. In. Annual Reliability and
Maintainability Symposium - RAMS 2008.
S. Wu, A. Akbarov 2012. Forecasting warranty claims for
recently launched products. In Reliability Engineering
& System Safety.
R. Vadlamani 2007. Modified Great Deluge Algorithm
versus Other Metaheuristics in Reliability
Optimization, Computational Intelligence in Reliability
Engineering, Studies in Computational Intelligence.
R. Gitzel, C. Stich 2011. Reliability-Based Cost Prediction
and Investment Decisions in Maintenance – An
Industry Case Study, In. Proceedings of MIMAR,
Cambridge, UK.
Bertino, E.; Maurino, A.; Scannapieco, Monica 2010. Guest
Editors’ Introduction. Data Quality in the Internet Era.
In Internet Computing, IEEE.
D.P. Ballou et al. 1997. “Modeling Information
Manufacturing Systems to Determine Information
Product Quality”, Management Science.
Borek, A.; Parlikad, A. K.; Webb, J.; Woodall, P. 2014.
Total information risk management – maximizing the
value of data and information assets.
Bertino, E.; Maurino, A.; Scannapieco, M. 2010. Guest
Editors’ Introduction. Data Quality in the Internet Era.
In Internet Computing, IEEE.
Becker, D.; McMullen W.; Hetherington-Young K. 2007.
A flexible and generic data quality metamodel. In
Proceedings of International Conference on
Information Quality.
Montgomery, N.; Hodkiewicz, M. 2014. Data Fitness for
Purpose. In. Proceedings of the MIMAR Conference.
Delonga, M. Zuverlässigkeitsmanagementsystem auf Basis
von Felddaten. Universität Stuttgart.
Bendell, T. 1988. An overview of collection, analysis, and
application of reliability data in the process industries.
In Reliability, IEEE Transactions.
Redman, T.C., ed. 1996. Data Quality for the Information
Age.
Leo L. Pipino, Yang W. Lee, Richard Y. Wang 2002. “Data
Quality Assessment”, Communications of the ACM.
Bovee, M.; Srivastava, R. P.; Mak, B. 2003. A Conceptual
Framework and Belief-function Approach to Assessing
Overall Information Quality. In. International Journal
of Intelligent Systems.
Peter Benson 2008. ISO 8000 the International Standard for
Data Quality, MIT Information Quality Industry
Symposium.
Xiaojuan, Ban; Shurong, Ning; Zhaolin, Xu; Peng, Cheng
2008. Novel method for the evaluation of data quality
based on fuzzy control. In Journal of Systems
Engineering and Electronics.
Damerau, Fred J. 1964. A technique for computer detection
and correction of spelling errors. In Communications of
the ACM.
Levenshtein, Vladimir I. 1966. Binary codes capable of
correcting deletions, insertions, and reversals, In Soviet
Physics.
Bard, Gregory V. 2007. Spelling-error tolerant, order-
independent pass-phrases via the Damerau–
Levenshtein string-edit distance metric, In Proceedings
of the Fifth Australasian Symposium on ACSW.
Wu, Shaomin 2013. A review on coarse warranty data and
analysis, In. Reliability Engineering & System Safety.
Hu, X. Joan, Lawless, Jerald F. 1996. Estimation of rate and
mean functions from truncated recurrent event data. In
Journal of the American Statistical Association.
Gitzel, R. 2014. Industrial Services Analytics. Presentation
at the 1. GOR Analytics Tagung.
A Data Quality Dashboard for CMMS Data
177