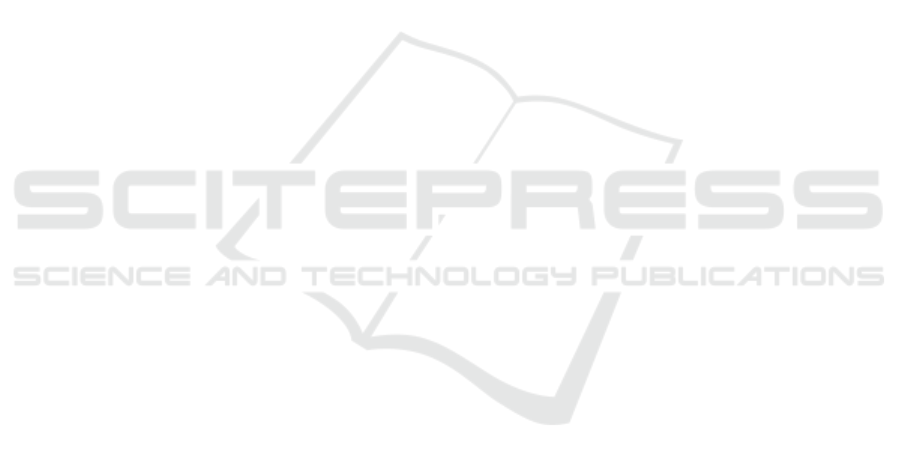
operator is to opt for the maintenance strategy that
would enable a better profitability of the windfarm.
Our method is focused on this priority. Indeed, the
vision of financial profitability, reinforces the
technical vision of maintenance while usually
profitability is often separated from the financial
sector. Availability is no longer the only criterion of
maintenance analysis because the wind farm’s
profitability accentuates this analysis.
Our approach uses a model based on MAS
theory to realize wind farm profitability scenarios
based on available budget forecasts and information
on breakdowns that would occur. The main
objective is to evaluate different scenarios and their
profitability providing financial indicators for one or
many failures list to choose the scenario that suits
the operator's requirements.
1.1 The Problem of Maintenance in
Wind Energy Sector
There are several types of maintenance that are used
in wind energy sector:
Preventive maintenance: it aims to reduce the
breakdowns by anticipating them. The interventions
are carried out after a well-defined duration (annual,
semi-annual etc…) or after a signal appearance
following the failure or the going beyond a
threshold. This type of maintenance aims to reduce
the possible risk of breakdown. It corresponds to a
logic of the breakdowns prevention and
maximization of the availability. Ideally for a wind
farm, this type of maintenance is carried out during
the periods of low wind to ensure availability during
the periods of strong winds.
Curative maintenance: used in a single way,
curative maintenance certainly reduced well the
maintenance costs, but it can quickly exceed the
forecasts and causes important disadvantages related
to the production. As the wind farm ages, the
number of corrective increases and generates
indirect costs which it is difficult to estimate before
the breakdowns.
Corrective maintenance: it’s a type of
maintenance made after a diagnosis of breakdown.
Its goal is to set back an element in operating
condition (Hajej and Rezg, 2012). It’s a strategy
which results in an unquestionable advantage
relating to the maximum use of the wind turbine’s
components; in fact, the equipment is replaced or
repaired only in the event of breakdown. It’s also
called the “breakdown” strategy. In the case of a
wind turbine, the failures often occur during period
of strong wind. However, it is in this period that the
wind turbine must be available to the production.
The wind turbine’s stop throughout corrective
maintenance thus involves a consequent production
loss. The single advantage of a corrective
maintenance is that it makes it possible to use the
equipment until exhaustion.
Hybrid maintenance: it is the most current type
of maintenance. It combines the two types of
maintenance: preventive and corrective. It consists
in anticipating some breakdowns by the means of
preventive interventions and being reactive for the
corrective O&M operations when the breakdowns
occur.
Several maintenance tools were developed by
research laboratories and companies. Each one of
these tools adopts an angle of analysis of
maintenance. It can be oriented to some maintenance
fields like spares management or to the whole O&M
field including: spares management, human
resources, installation etc…). For example:
1. SINBAD (Guillon, 2015): is a tool which main
objective is to predict the behaviour of a wind
turbine at any moment. This project was born
from a recommendation of a Franco-British
partnership dedicated to the offshore oil rig to
create a digital tool allowing the visualization of
the tree structure of wind turbines offshore oil
rigs.
2. The OMCE (Operation and Maintenance Cost
Estimator) (Rademakers et al., 2009): it is one of
the most complete models of simulation,
marketed since 2004. The project was initiated
by a consortium including Vestas, Shell Wind
Energy, DTU and ECN (Energy Research of the
Netherlands). It combines three strategies of
maintenance: corrective, preventive and
predictive to predict the annual cost of the
maintenance actions of wind farms. (Onshore
and Offshores) (van de Pieterman et al., 2011).
As inputs, the tool records the components
reliabilities, maintainer information and the
operation to provide maintenance costs.
From the maintenance operator’s point of view, the
problems consist in finding the “optimal” cost of
maintenance that represents balance between an
expected production of the wind farm and a budget
associated with a series of breakdowns planned
during the period. To optimize maintenance, we thus
must optimize the budget of maintenance
(subcontracts and spares) on the wind farms because
it represents the most important owner’s growth
drivers.
ICAART 2018 - 10th International Conference on Agents and Artificial Intelligence
160