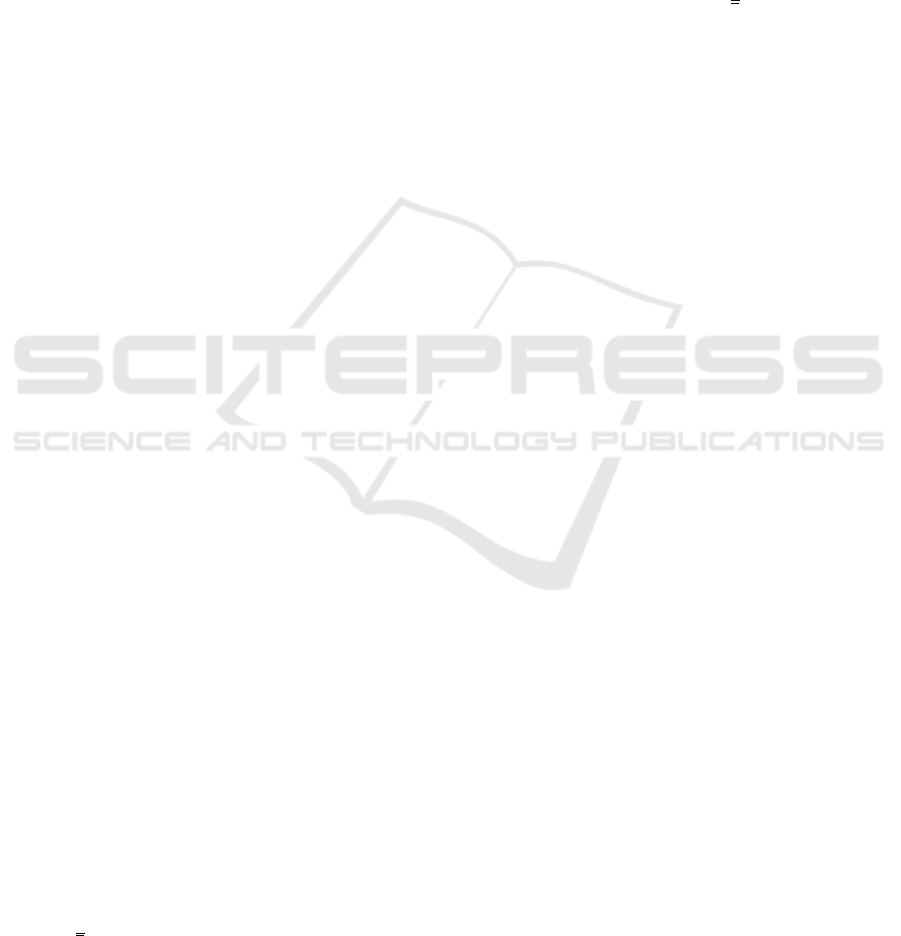
tions evaluated in this workstrongly differ in their per-
formance. Results show that preprocessing has a high
impact on classifier performance and that basic edge-
enhancing methods allow the best class separability,
outperforming direction-sensitive approaches such as
the Sobel-of-Gaussian or Gabor Filters. An interest-
ing fact is that the per-image classification rate gen-
erally remains constantly high and is generally robust
towards drops in the patch-wise classification perfor-
mance.
6 CONCLUSION
In this paper, we have described and thoroughly eval-
uated a solution for the fully automated detection of
faulty weft threads in automated weaving machines
using computer vision. First, we developed a robust
multi-camera setup capable of capturing the entire
shed area with high resolution. The resulting images
were divided into small patches and each patch was
classified independently. We described and evaluated
a number of methods for preprocessing, feature ex-
traction and feature-based classification. Parameter
variations of the extraction and classification methods
were analyzed and optimized settings were reported.
Finally, we introduced a maximum-a-posteriori-based
method for the final defect classification of a whole
image based on the detection distributions in positive
and negative test images. Results have shown that
our presented methods allow a reliable error detec-
tion with high classification rates, making the system
suitable for future industrial applications.
REFERENCES
Bishop, C. M. (2006). Pattern recognition. Machine Learn-
ing, 128.
Bovik, A. C., Clark, M., and Geisler, W. S. (1990). Multi-
channel texture analysis using localized spatial filters.
IEEE transactions on pattern analysis and machine
intelligence, 12(1):55–73.
Breiman, L. (2001). Random forests. Machine learning,
45(1):5–32.
Dalal, N. and Triggs, B. (2005). Histograms of oriented gra-
dients for human detection. In 2005 IEEE Computer
Society Conference on Computer Vision and Pattern
Recognition (CVPR’05), volume 1, pages 886–893.
IEEE.
Hanbay, K., Talu, M. F., and Ömer Faruk Özgüven
(2016). Fabric defect detection systems and meth-
odsâC”a systematic literature review. Optik - In-
ternational Journal for Light and Electron Optics,
127(24):11960 – 11973.
Karayiannis, Y. A., Stojanovic, R., Mitropoulos, P., Koula-
mas, C., Stouraitis, T., Koubias, S., and Papadopoulos,
G. (1999). Defect detection and classification on web
textile fabric using multiresolution decomposition and
neural networks. In Electronics, Circuits and Systems,
1999. Proceedings of ICECS’99. The 6th IEEE Inter-
national Conference on, volume 2, pages 765–768.
IEEE.
Kumar, A. (2008). Computer-vision-based fabric defect de-
tection: a survey. IEEE transactions on industrial
electronics, 55(1):348–363.
Ngan, H. Y., Pang, G. K., and Yung, N. H. (2011). Auto-
mated fabric defect detectionâ
C”a review. Image and
Vision Computing, 29(7):442–458.
Ojala, T., Pietikainen, M., and Maenpaa, T. (2002). Mul-
tiresolution gray-scale and rotation invariant texture
classification with local binary patterns. IEEE Trans-
actions on pattern analysis and machine intelligence,
24(7):971–987.
Sari-Sarraf, H. and Goddard, J. S. (1999). Vision system
for on-loom fabric inspection. IEEE Transactions on
Industry Applications, 35(6):1252–1259.
Schneider, D., Holtermann, T., and Merhof, D. (2014). A
traverse inspection system for high precision visual
on-loom fabric defect detection. Machine Vision and
Applications, pages 1–15.
Stojanovic, R., Mitropulos, P., Koulamas, C., Karayiannis,
Y., Koubias, S., and Papadopoulos, G. (2001). Real-
time vision-based system for textile fabric inspection.
Real-Time Imaging, 7(6):507–518.
Wada, Y. (1984). Optical weft sensor for a loom. US Patent
4,471,816.
ICPRAM 2018 - 7th International Conference on Pattern Recognition Applications and Methods
132