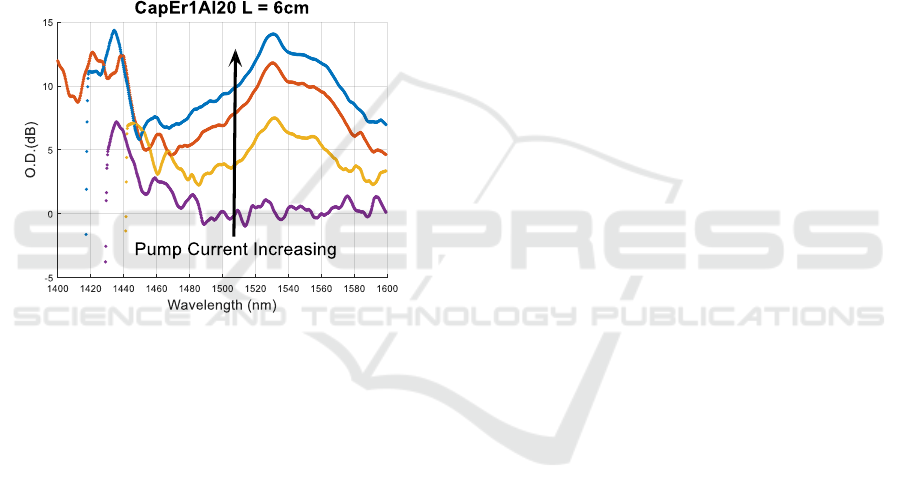
Although the fibers fabricated show promising
spectral results, they suffer from high background
loss, this is mainly due to the purity and preparation
environment and method of the samples.
Furthermore, clean room environment was not
utilized during the process.
Nonetheless, we would like to perceive this
shortcoming in a positive manner: i.e. clean room
environment is not necessary for this prototyping
process, although it would be good for potential better
results. To further improve the fabrication precision,
tighter control of the temperature is essential. This
“quick and dirty” process can be adopted until one is
satisfy with the doping solution composition before
switching it to the standard fabrication for good
quality fibers.
Figure 7: Spectra behavior of the fabricated Erbium doped
silica fiber when pumped at 976 nm.
4 CONCLUSIONS
In conclusion, we have demonstrated a concept of
miniaturizing the standard fiber fabrication processes
to a benchtop version with repeatable results. We
have also successfully fabricated rare earth doped, i.e.
Ytterbium and Erbium doped silica fibers using the
method incorporating with solution doping technique,
and obtained reasonable spectra results. Undeniably,
the length and quality of the fibers are traded-off by
the time and cost involved. This process is beneficial
for those who are requiring small quantity of the
specialty optical fiber for rapid prototyping purposes,
especially for the less mature optical fiber
technologies, such as soft-glasses fibers. It also opens
up the possibilities of exploring other glass hosts with
various materials and compositions in a smaller scale.
ACKNOWLEDGEMENTS
This work is funded by Temasek Laboratories @
NTU (Grant No: 9016100134). We acknowledge the
technical support by the laboratory managers and
technical support officers of OPTIMUS and COFT,
NTU
REFERENCES
T. Izawa, 2000, “Early days of VAD process,” IEEE J. Sel.
Topics Quantum Electron. 6, 1220 – 1227.
V. Petit, A. L. Rouge, F. Beclin, H. E. Hamzaoui, and L.
Bigot, 2010, “Experimental study of SiO2 soot
deposition using the outside vapor deposition method,”
Aerosol Science and Tech. 44, 388 – 394.
M. Blankenship, and C. Deneka, 1982, “The outside vapor
deposition method of fabricating optical waveguide
fibers,” IEEE J. Quantum Electron. 18, 1418 – 1423.
J. Cho, J. Kim, and M. Choi, 1998, “An experimental study
of the heat transfer and particle deposition during the
outside vapor deposition process,” Int J. Heat and Mass
Transfer 41, 435 – 445.
S. R. Nagel, J. B. MacChesney, and K. L. Walker, 1982,
“An overview of the modified chemical vapor
deposition (MCVD) process and performance,” IEEE J.
Quantum Electron. 18, 459 – 476.
V. Matejec, M. Hayer, M. Pospisilova, and I. Kasik, 1997,
“Preparation of optical cores of silica optical fiber by
the sol-gel method,” J. Sol-Gel Science Tech. 8, 889 –
893.
J. L. Auguste, G. Humbert, S. Leparmentier, M. Kudinova,
P. O. Martin, G. Delaizir, K. Schuster, and D.
Litzkendorf, 2014, “Modified powder-in-tube
technique based on the consolidation processing of
powder materials for fabricating specialty optical
fibers,” Materials 7, 6045 – 6063.
S. Tammela, P. Kiiveri, S. Sarkilahti, M. Hotoleanu, H.
Vaikonen, M. Rajala, J. Kurki, and K. Janka, Sep 2002,
“Direct nanoparticle deposition process for
manufacturing very short high gain Er-doped silica
glass fibers” presented at 28th European Conference on
Optical Communication (ECOC), Copenhagen.
J. E. Townsend, S. B. Poole, and D. N. Payne, 1987,
“Solution-doping technique for fabrication of rare-
earth-doped optical fibers,” Elec. Lett. 23, 329 - 331.
K. Oh and U. Paek, 2012, “Preform fabrication and optical
fiber drawing process” in Silica Optical Fiber
Technology for Devices an Components – Design,
Fabrication, and International Standards, Wiley, pp. 83
- 130.
Benchtop Mini Preform Fabrication for Specialty Optical Fibers
189