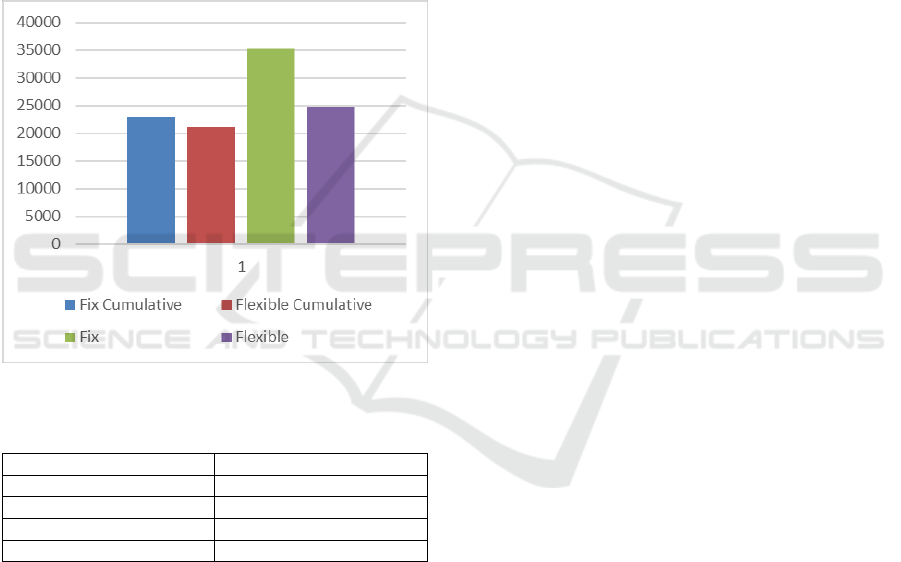
We also consider computation time for each
policy in order to verify the applicability of the
strategy, particularly for larger models. Table 4
presents the computation time per policy for the
whole distribution system. Fixed and flexible silo
allocation models need the minimum time among the
other strategies, while when the model is cumulative
in storage capacity allocation, the required time
becomes larger. Fixed cumulative approach needs 87
seconds to achieve the optimized solution, while it is
even more with Flexible Cumulative approach with
106 seconds. Higher computational time specifies the
model complexity level and computation difficulty
that results in lower interest to apply the complex
solutions for large systems.
Figure 1: Overall costs for each policy.
Table 4: Computation time per policy.
According to the results of the illustrative
example, flexible approach has got the most
reasonable results for both computation time and cost
reduction. But if the model is small in size, the fix
cumulative approach seems more reasonable, since it
is more logical to rent a silo for the whole planning
horizon.
6 CONCLUSIONS
In this paper we considered Stochastic Periodic
Inventory Routing Problem with storage capacity
limitation. The proposed safety stock-based SPIRP
model involved storage capacity as a constraint in the
model to optimize it with regard to cost minimization.
Four different policies are proposed to deal with
storage capacity limitation at retailers. The
advantages and disadvantages of these approaches
have been discussed in this paper. Finding the balance
between transportation and inventory costs together
with the storage costs (silo rent) is the most important
factor in SPIRP model. Definitely it depends on the
value of product itself, silo fee, promised service
level, demand variability rate at the retailers, length
of the planning horizon, etc., to allocate silos to the
retailers. The illustrative example presented in this
paper has revealed the advantages of flexible model
among other policies. In addition for smaller
distribution centres, fixed cumulative approach seems
to be an appropriate strategy to optimize the storage
capacity. As for future research, the applicability of
these approaches will be evaluated in some
experimental cases with design of various
experiments based on the variables. In addition, their
impact on service level, inventory and transportation
costs, and computational time will be measured and
discussed.
REFERENCES
Aghezzaf, E. H. 2007. Robust distribution planning for
supplier-managed inventory agreements when demand
rates and travel times are stationary. J Oper Res Soc, 59,
1055-1065.
Bell, W. J., Dalberto, L. M., Fisher, M. L., Greenfield, A.
J., Jaikumar, R., Kedia, P., Mack, R. G. & Prutzman, P.
J. 1983. Improving the Distribution of Industrial Gases
with an On-Line Computerized Routing and
Scheduling Optimizer. Interfaces, 13, 4-23.
Bertazzi, L., Bosco, A., Guerriero, F. & Laganà, D. 2013.
A stochastic inventory routing problem with stock-out.
Transportation Research Part C: Emerging
Technologies, 27, 89-107.
Coelho, L. C., Cordeau, J.-F. & Laporte, G. 2014a.
Heuristics for dynamic and stochastic inventory-
routing. Computers & Operations Research, 52, Part A,
55-67.
Coelho, L. C., Cordeau, J.-F. & Laporte, G. 2014b. Thirty
Years of Inventory Routing. Transportation Science,
48, 1-19.
Federgruen, A. & Zipkin, P. 1984. A Combined Vehicle
Routing and Inventory Allocation Problem. Operations
Research, 32, 1019-1037.
Pujawan, N., Arief, M. M., Tjahjono, B. & Kritchanchai, D.
2015. An integrated shipment planning and storage
capacity decision under uncertainty A simulation study.
International Journal of Physical Distribution &
Logistics Management, 45, 913-937.
ICORES 2018 - 7th International Conference on Operations Research and Enterprise Systems
222