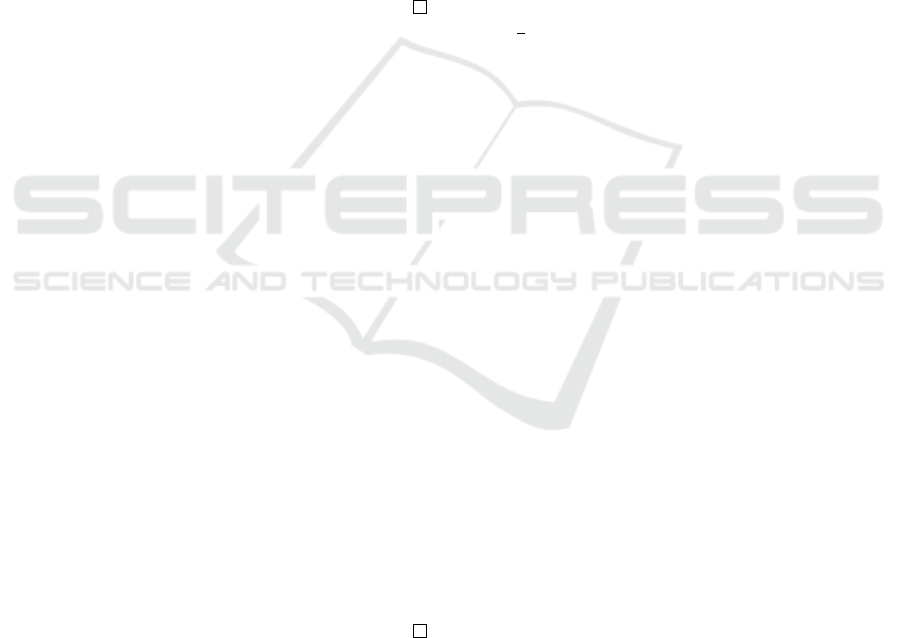
If the random demand d is bounded or Gaussian
then it satisfies (1). (Some companies work with pos-
sibly negative demands. Assuming a normal distribu-
tion is hence not irrelevant.)
The proof of part (iii) relies on the following
technical lemma.
Lemma 2. Consider g(d) = inf
y∈Y
G(y,d), whereY is
non-empty and where the function G is non-negative
and κ-Lipschitz with respect to d. If the random va-
riable d satisfies (1), then g(d) also satisfies (1) with
C
0
= max{1,e
G(y
0
,0)
C} and K
0
= Kκ + G(y
0
,0), for
y
0
∈ Y .
Proof. For u ≥ 0 we take y
0
∈ Y yielding g(d) ≤
G(y
0
,0) + κkdk. We then have E[e
ug(d)
] ≤
E[e
uG(y
0
,0)
e
κukdk
] ≤ C
0
e
K
0
u
2
. For u ≤ 0, by non-
negativity of G we have g(d) ≥ 0, hence E[e
ug(d)
] ≤
1.
Proof of Proposition 1. Let Q
t
be the (bounded) set
of feasible values for the first-stage variables q
t
=
(q
r
t
)
r∈R
in (2SA). Denote by F(q
t
,d) the minimal
cost of (2SA) that can be reached when the first stage-
variables are fixed to q
t
∈ Q
t
and the realization of
the demand is d = (d
r
t
0
)
t
0
≥t,r∈R
. We introduce the
map f : q
t
7→ E[F(q
t
,d)], which associates to a gi-
ven choice of q
t
∈ Q
t
the expected minimal cost, and
similarly the map
ˆ
f
m
, which associates to a q
t
∈ Q
t
the minimal cost of (2SA-m) when the first-stage va-
riables are set to this q
t
.
The map f is continuous and Q
t
is compact. Thus
f is bounded, and, by (Shapiro et al., 2009, Theorem
7.48), we have that (
ˆ
f
m
(q
t
))
m∈Z
+
converges to f (q
t
)
uniformly on Q
t
. Then (i) and (ii) are direct conse-
quences of (Shapiro et al., 2009, Theorem 5.3).
By Lemma 2, there exist K and C such that for
any q
t
∈ Q
t
, F(q
t
,d) satisfy (1). Consequently there
exists σ > 0 such that for all q
t
,q
0
t
∈ Q
t
, the random
variable [F(q
t
,d) − f (q
t
)] − [F(q
0
t
,d) − f (q
0
t
)] is σ-
subgaussian, (see e.g., (Vershynin, 2010)). Further-
more, for any demand d, the map F(·, d) is Lipschitz-
continuous on Q
t
. Then, according to (Shapiro et al.,
2009, Theorem 5.18), for every α ∈ (0,1), there exists
M ∈ Z
+
such that for m ≥ M, we have P(Q
δ
m
⊆ Q
ε
) >
1 − α.
5 NUMERICAL EXPERIMENTS
5.1 Instances
C++11 has been chosen for the implementations and
Gurobi 6.5.1 was used to solve the model on a PC
with Intel(R) Core(TM) i7-3770 CPU @ 3.40GHz
and 8Go RAM.
The instances used are realistic and have been pro-
vided by a client of the partner. The client gave actu-
ally the figures of seven assembly lines but we give
the results for only two of them: L2 and L6. The line
L2 experiences overcapacity: the ratio expected de-
mand over total capacity is smaller than 1 (actually
equal to 0.7). The line L6 experiences undercapacity:
the ratio expected demand over total capacity is lar-
ger than 1 (actually equal to 1.1). The horizon T is
the typical one used in practice by this client, namely
T = 13 weeks (a quarter). The demand is obtained
via d
r
t
= (
¯
d
r
t
+ e
r
t
)
+
, where the
¯
d
r
t
’s are historical data
and where e
r
t
is a generalized autoregressive process
so that e
r
t
= 0.25e
r
t−1
+ 0.75ε
t
, where ε
t
is a Gaussian
white noise process with zero mean and standard de-
viation equal to v
¯
d
r
t
where v is the “volatility” and is
chosen in
{
0.2,0.5
}
. The initial inventory is set to
s
r
0
=
1
3
(
¯
d
r
1
+
¯
d
r
2
+
¯
d
r
3
). The other parameters are pro-
vided in Table 1. In particular, for each value of v,
we have considered three possible values of the unit
backorder cost γ, which have been determined follo-
wing a procedure described in Section 6. At the mo-
ment, we do not discuss further these values and take
them as part of the input, as required by the problem
formulation. The parameter C is the capacity of the
line before normalization. (Recall that problem and
the model have been formulated in Section 2 after nor-
malization.) In the column
˜
h
r
, we indicate the range
of the holding costs before normalization. We obtain
the h
r
’s by dividing these costs by C.
The number m of scenarios used to solve (2SA-m)
is fixed to 20, determined by preliminary experiments
showing that it is a good trade-off between accuracy
and tractability. The time limit of the solver has been
set to 90 seconds.
5.2 Other Heuristics
Our method is compared with three other heuristics.
The first heuristic is the deterministic version
of (S), where the random demand is replaced by its
expectation.
The second one, the lot-size heuristic, consists in
determining before the first week once and for all a
value `
∗
r
for each reference r ∈ R . At time t, if the in-
ventory of reference r is below a precomputed safety
level, the quantity q
r
t
is chosen so that the inventory of
reference r exceeds the safety level of exactly `
∗
r
. In
case of capacity issues, the production is postponed
and thus backorder costs appear. In addition, if some
capacity issues are easily anticipated, the production
of a reference r can be activated even if the inventory