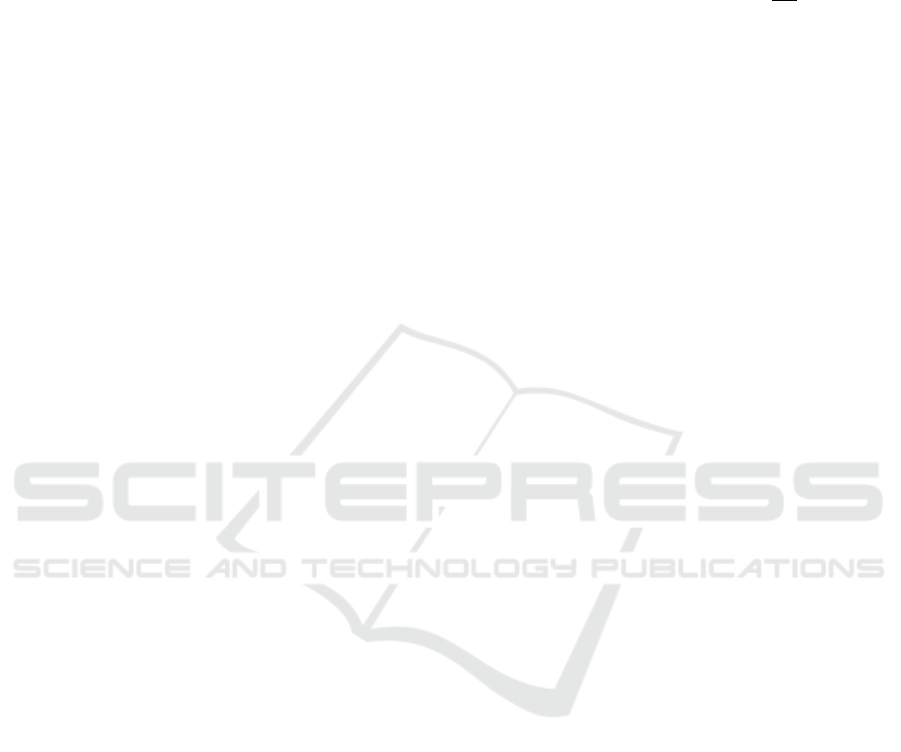
The total distribution cost rate equals the sum of
all the routes r ∈ R that the supplier has to perform to
replenish all his retailers I:
TC
S
=
∑
r∈R
TC
r
(4)
The first phase of the CIRP algorithm thus divides
the set of retailers into subsets that are each covered
by a separate route and for which the route cycle time
is chosen to minimize the cost rate.
The second phase of the CIRP algorithm assigns
the routes to vehicles and to specific periods using a
construct-and-improvement heuristic. The sequence
of the routes stays the same, but their cycle times can
be adjusted to minimize the required number of vehi-
cles and thus the fleet costs.
The construction heuristic is a best-fit insertion
heuristic that inserts the routes into the schedule in
such a way that the cumulative remaining time of the
vehicles to which the routes are assigned is minimal.
The routes are inserted in the schedule using two cy-
cle time selection rules. Firstly, the routes are inserted
with cycle times as close as possible to their optimal
cycle time (resulting in minimal route cost rates). Or
secondly, they are inserted with cycle times as close
as possible to their maximal cycle times (resulting in
minimal fleet cost rate). This results in two initial
schedules that are passed on to the improvement step.
In the improvement step, two local search operators
are applied, namely removing any single route from
the schedule and reinserting it in the cheapest possi-
ble spot, or removing all routes made by the vehicle
with the lowest utilization from the schedule en rein-
serting them in the cheapest possible way. To escape
a potential local optimum, the schedule that results
from the improvement step is scrambled by shuffling
route allocations. Local search is then repeated on the
scrambled solution. A predefined number of scram-
bles is set as a stopping criterion for the improvement
step.
The two-phase route and fleet design approach is
then reiterated within a metaheuristic framework (Raa
and Dullaert (2017)).
4 REDISTRIBUTION STRATEGY
AMONG RETAILERS
Once the routes and their allocation to vehicles are
known, the supplier can execute his distribution plan.
Then, the actual daily demand values a
i,t
are observed
for all retailers in each period. These demand rates
are generated using their known probability distribu-
tion. Since these demand values deviate from the av-
erage demand values, the actual inventory levels and
the resulting inventory holding costs will differ from
the inventory holding costs resulting from the CIRP
solution and have to be recalculated. Hence, in order
to know the actually incurred distribution cost rate,
the inventory holding costs (T
r
∑
i∈I
r
η
i
d
i
2
) have to be
subtracted from the routes’ cost rates TC
r
.
Further, inventory levels may be lower than antici-
pated (after periods with higher than average demand)
and the risk of stockout may occur. This is when re-
distribution through lateral shipments is activated.
Given that the cycle times of the routes can differ,
the time periods in which the retailers are replenished
will also differ from one retailer to another. Hence,
we allow redistribution in each time period across a
certain planning horizon.
At the start of period t, every retailer i has an in-
ventory level SI
i,t
. The ending inventory of retailer i
in that period EI
i,t
is calculated by subtracting the de-
mand in that period from the start inventory (= SI
i,t
-
a
i,t
). Redistribution is assumed to happen ’overnight’
between the periods, so the starting inventory level
of the next period also includes any lateral transship-
ments.
The redistribution quantities are thus determined
based on the ending inventory level of the retailers.
The retailers are divided into three different groups
in each time period. The retailers whose ending in-
ventory is too low to reach a certain desired service
level until their next delivery from the supplier, are
called receivers (1). Retailers whose ending inventory
is more than necessary to reach their desired service
level are called contributors (2). Finally, there are the
retailers that do not want to participate to the redis-
tribution in a specific period (3). The group to which
a retailer belongs can differ from one period to the
next, since his ending inventory will change accord-
ing to his incurred demand rate, redistributed quanti-
ties from the previous period and possible deliveries
from the supplier.
The desired service level is expressed by the fill
rate (i.e., the fraction of demand filled from items
available in inventory). For each time period, three
inventory levels are determined for each retailer, the
critical inventory level CI
i,t
, the threshold inventory
level TI
i,t
and the optimal inventory level OI
i,t
. The
critical inventory level CI
i,t
of a retailer is the inven-
tory level below which he wants to receive goods from
other retailers. So, a retailer is a receiver in time pe-
riod t if EI
i,t
<CI
i,t
. The threshold inventory level TI
i,t
is the inventory level above which he is willing to
share goods with other retailers. Hence, a retailer is
a contributor in time period t if EI
i,t
>TI
i,t
. The opti-
mal inventory level OI
i,t
of a retailer is the inventory
ICORES 2018 - 7th International Conference on Operations Research and Enterprise Systems
234