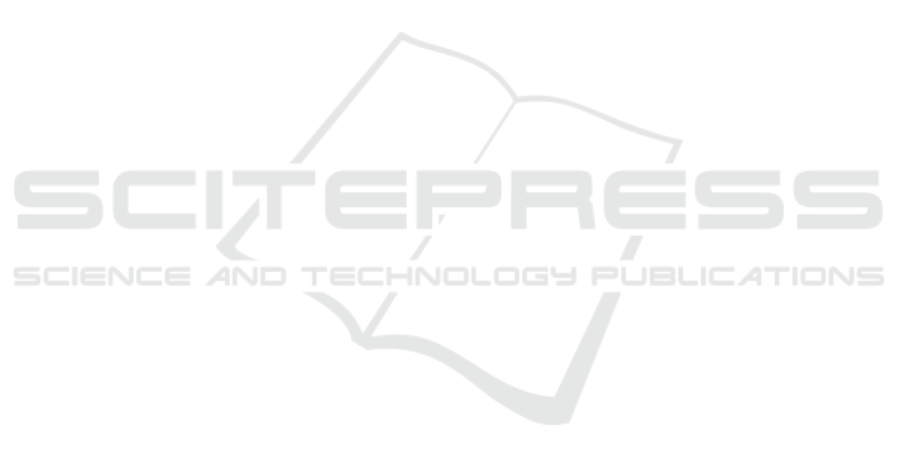
Optimization Parameters for Laser-induced Forward Transfer of
Al and Cu on Si-wafer Substrate
Mohammad Hossein Azhdast
1
, Hans Joachim Eichler
1
, Klaus Dieter Lang
2
and Veronika Glaw
2
1
Institute of Optics and Atomic Physics, Technical University of Berlin, Ernst-Ruska-Gebäude, Berlin, Germany
2
Institute of Electrical Engineering and Computer Science, IZM Fraunhofer, Gustav-Meyer-Allee 25, Berlin, Germany
Keywords: Laser, Material Processing, Laser Direct Writing, Nano Particle Deposition.
Abstract: The research goal is to perform a laser-writing study to deposition of micro/nano particles on the substrate
as interconnection usage. The threshold of laser energy, pulses per laser shot, as well as pulse overlapping is
crucial to achieve the best deposition results possible. The present study aims to the novel technique by laser
deposition of Aluminium and Copper nano particles on silicon wafer substrate. Thin µm films have been
deposited from one-side coated glass to Silicon wafers by sputtering nano particles using laser radiation.
Distance between donor film and substrate (ε) was up to several 100 µm and it has been optimized as 300
µm. A step-by-step optimization guide for deposition parameters were first developed and presented. The
identification of laser energy threshold, pulses per laser shot, in addition to pulse overlapping is essential if
the best deposition results are going to be drawn by laser direct writing method. This technique is regarded
as the most important direct-write alternative for lithographic processes in order to generate patterns with
high-resolution.
1 INTRODUCTION
The goal of this thesis is to perform a complete
study of Laser deposition, structuring, and adhesion
mechanism as one of the generative manufacturing
processes with laser radiation. One of the methods of
making thin films is sputter deposition. This
procedure is a process that particles will be ejected
from the material owing to bombardment of the
solid target by energetic atoms.
The deposition of nano particles is demonstrated
by the preparation of an Under Bump Metallization
(UBM); although, the laser sputtering technique may
be used for a multitude of other applications like:
bonding technology for microelectronics, as well as
micromechanical and micro-optical devices and
components (Craig, 2007 and Pique, 2008). Copper
and Aluminium based on their chemical properties
and different reflectivity, have similar reactions in
Infra-red laser for material processing and different
behaviour in other laser wavelengths (Azhdast, 2017
and Golnaz, 2008).
For large-scale manufacturing situations, where
the parallel creation of identical patterns is essential,
pattern-transfer techniques (PTT) are the most
economical choice. Here, the pattern of interest is
produced onto the substrate in one step at the same
time. Micro contact printing (MCP) as well as a
photolithography (PL) is considered the most widely
applied PTT. Especially photolithography benefitted
enormously from recent technological advances such
as the launch of extreme UV light sources, which
enabled the production of nano structures. However,
for both of these techniques, MCP and PL, a number
of disadvantages are to be taken into account.
This printing process includes three steps; (1) to
ablate material from donor glass with a focused laser
pulse. (2) Transition of ablated particles from
acceptor to receiver substrate. (3) Deposition of
transferring material to be adhered onto the acceptor
substrate (Bera, 2007 and Wartena, 2004).
2 PROCESS EXPLANATION
The procedure type which has been used in this
paper is to deposition nano metal particle by direct
laser radiation from one side coated glass as a donor.
Neither mask nor ultra- violet light source will be
used in nano particle printing, which is so expensive
and they are time consuming method. Compared to
228
Azhdast, M., Eichler, H., Lang, K. and Glaw, V.
Optimization Parameters for Laser-induced Forward Transfer of Al and Cu on Si-wafer Substrate.
DOI: 10.5220/0006627702280231
In Proceedings of the 6th International Conference on Photonics, Optics and Laser Technology (PHOTOPTICS 2018), pages 228-231
ISBN: 978-989-758-286-8
Copyright © 2018 by SCITEPRESS – Science and Technology Publications, Lda. All rights reserved