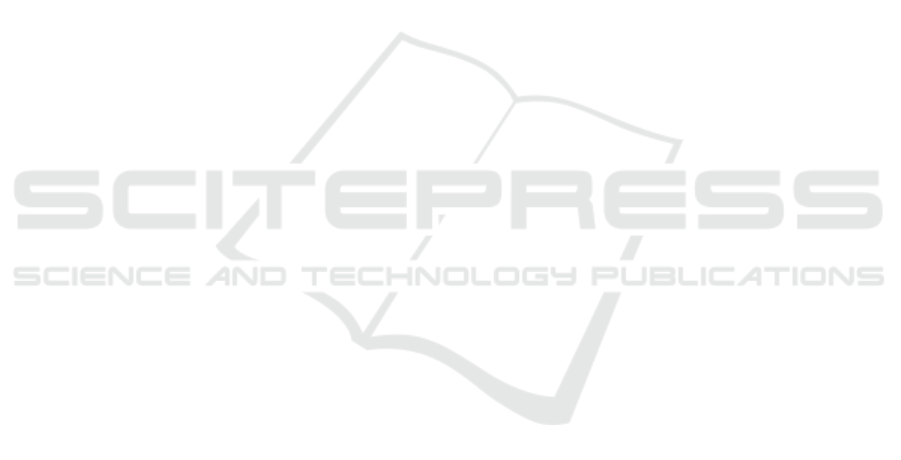
4.1 Safety Assessment with the AHP
and the FMEA
The AHP by Thomas L. Saaty [Saaty, 1990] is used
for making decisions regarding safety in various do-
mains, e.g., in [Jianbin et al., 2009], [Wang et al.,
2011] and [Cheng et al., 2011]. However, the AHP
is also used for making decisions based on security
concerns, e.g., in [Ji et al., 2010] and [Taha et al.,
2014]. A tradeoff analysis on behalf of safety, con-
sidering security and timing concerns as well as func-
tional demands does not seem to have been evaluated
scientifically before and is therefore unique in liter-
ature. Although the AHP is also used for making
decisions on security concerns, e.g., [Jianbin et al.,
2009] and [Taha et al., 2014] a tradeoff analysis on
behalf of safety, taking security and timing issues
as well as functional demands into account doesn’t
seem to have been evaluated scientifically before and
is therefore unique in literature. A fairly similar ap-
proach, performing a tradeoff analysis on behalf of
safety that combines the FMEA with the AHP, is the
work of [Zhao et al., 2013]. They focus on analyzing
the reliability of manufactoring processes by means of
the Process Failure Mode Effect and Critically Anal-
ysis (PFMECA), enhanced by the AHP. This method
has solely been designed for analyzing safety in man-
ufacturing processes. The method proposed in this
paper can be applied to any SCS, product or process.
4.2 Related Projects on Safety and
Security
There is a project which is important to be consid-
ered: SESAMO (Security and Safety Modelling).
Although it pursues quite similar objectives, it fo-
cuses on safety and security requirements, aiming
”to develop a component-oriented design methodol-
ogy based upon model-driven technology, jointly ad-
dressing safety and security aspects and their inter-
relation for networked embedded systems in multi-
ple domains.” [SESAMO, 2015]. One major objec-
tive has been developing procedures for integrated
analysis of safety and security demands, focusing on
identifying hazards to facilitate an informed tradeoff
between contradicting safety and security demands.
One goal is to provide convincing evidence, justifying
”that the risks associated with the system are as low
as reasonably practicable” [Paulitsch et al., 2012].
Stating that a system cannot be safe without being se-
cure, the SESAMO project supports the position of
considering safety as the top-level goal, that can be
affected by security issues. [Paulitsch et al., 2012] In
contrast to this paper, the SESAMO project does not
provide a competitive tradeoff analysis by a system-
atic method like the modified AHP combined with the
FMEA. Moreover, the results of the tradeoff analy-
sis as proposed by SESAMO are not fully compatible
with the FMEA. However, the FMEA is a compulsory
part of the certification requirements in the automo-
tive industry [Paulitsch et al., 2012]. Moreover, there
is another project called SafeCer (Safety Certification
of Software-Intensive Systems with Reusable Com-
ponents). It aims to increase ”[...] efficiency and re-
duce(d) time-to-market by composable safety certifi-
cation of safety-relevant embedded systems.” [Safe-
Cer, 2015] The project focused on providing methods
and tools composing safety arguments for a system
by reusing already established arguments and proven
properties of the subsystems. This project share the
goal of providing means (architectures, tools, pro-
cesses or standardization) to enhance efficient safety
assurance and certification. However, this project
doesn’t explicitly aim to support a MCDA taking
safety, security and timing issues into account, as it
has been proposed in this paper. [SafeCer, 2015]
5 CONCLUSION AND OUTLOOK
In this paper an approach has been presented how to
combine SST concerns for the development of safety-
critical systems. Thereby, safety issues with a max-
imum degree of safety are of primary importance.
For that purpose, an SGH has been introduced which
is based on GSN. This SGH contains all safety-,
security- or timing goals and SPOFs within a hierar-
chical structure. Furthermore, it contains alternative
solutions, in order to calculate a tradeoff. Addition-
ally, it has been demonstrated how to perform risk as-
sessments of the SPOFs using the FMEA technique.
The tradeoff in itself is calculated by means of two
possible methods: The RCM and the PCM. The ba-
sis for the calculation is either the FMEA technique
or the AHP algorithm. Furthermore, the approach has
been evaluated based on an application example com-
paring two different ACC systems by means of three
selected scenarios with respect to stability and adapt-
ability of applied techniques. For further work, it
would be useful to cluster some goals and to perform
the tradeoff analysis in an abstract manner. Thus, it
would be possible without any effort to check if a sys-
tem component is profitable or not. Another aspect
that has not been considered in this paper concerns
product line engineering. In those days there are nu-
merous configuration options of an automotive vehi-
cle. Hence, a product line approach will be developed
contemporary.
Multi-Concerns Engineering for Safety-Critical Systems
509