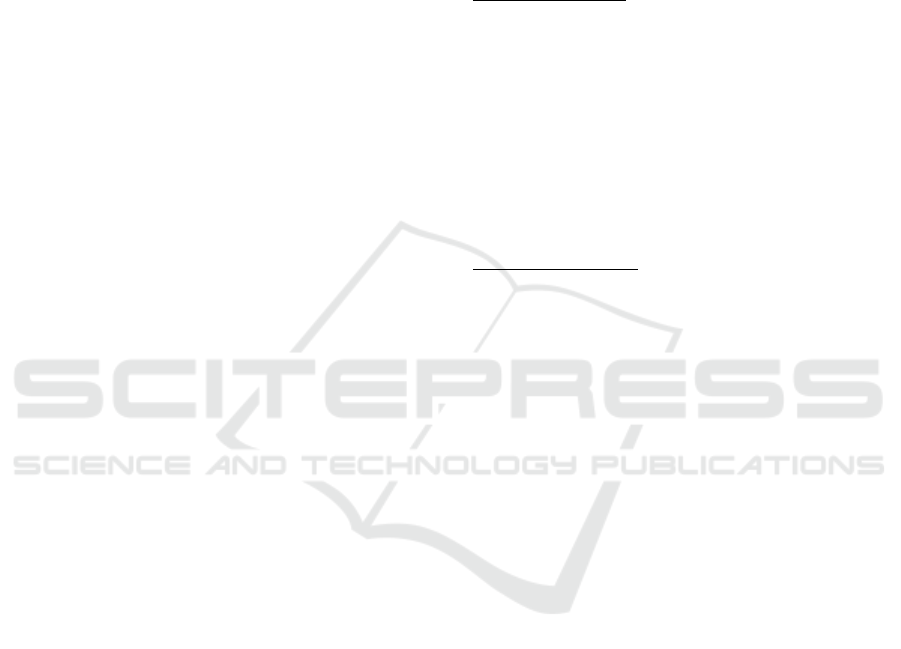
can be divided into clusters such that each part type
is unambiguously assigned to a single cluster (cell).
Nonetheless, it is both an important and tough com-
binatorial optimization question to determine as to
which type of spares to pool together.
Even though pooling of resources are extensively
studied, to the best of our knowledge, no results
have been presented on pooled repair shops designs
in spare part supply systems integrated with capac-
ity decision. Thus, this study will contribute to the
current literature by addressing following fundamen-
tal issues: (i) how many clusters to pool; (ii) which
spare part types to pool together, and; (iii) how to as-
sign servers (capacity) to each cluster.
The rest of the paper is organized as follows. In
Section 2, problem definition and the mathematical
model are presented. The solution algorithm for the
proposed model is discussed in Section 3. Section 4
provides a computational study under different sce-
narios and input settings. Conclusions and future re-
search directions are summarized in Section 5.
2 PROBLEM DESCRIPTION AND
FORMULATION
The design problem of a repair shop in a single ech-
elon repairable multi-item spare part supply system
being considered here is illustrated in Figure 1. The
repair shop consists of several parallel multi-skilled
servers, and storage facilities for the repaired items.
Once a failed part received from technical system at
the installed base, it is queued to be served by a suit-
able server with the required skills. At the same time,
if a repaired (as-good-as-new) part is available in the
inventory, it is sent back to the installed base. If the
item is not available in the stock, the request is back-
ordered. In this case, the technical system goes down
and a downtime cost occurs till the requested ready-
for-use part is delivered.
The repair shop may have pooled structure with
one or more cells/clusters or an arbitrary structure. In
Figure 1(a), an example of a pooled repair shop with
five types of failed stock keeping units (SKUs), two
clusters and four servers is shown. The first cluster
has a dedicated server with the ability to serve one
type of SKU. On the other hand, the second clus-
ter is obtained by pooling remaining four SKUs, and
this cluster has three cross-trained servers to serve all
(four) different types of repairables in that cluster. On
the other hand, in Figure 1(b), an arbitrary design is
presented, where the first and the second clusters have
‘N’ and ‘W’ structures, respectively. It is should be
noted that in arbitrary designs, not all of the servers in
a cluster are fully flexible; i.e., some servers are par-
tially cross-trained to repair only a subset of all SKUs
in the cluster. In this paper, we restrict design alterna-
tives limited to only pooled repair shops as in Figure
1(a), and formulate a stochastic mixed-integer mathe-
matical programming model to find the minimum cost
spare part supply system. The sets, parameters and
decision variables for the developed formulations and
solution procedures are presented as follows.
Decision variables:
S
i
: Amount of initial inventory (basestock level)
kept on stock for SKU type i ( i = 1,...,N),
where S = (S
1
,. ..,S
N
).
z
k
: Number of the operational servers in the cluster
k (k = 1,. . .,y), and where Z = (z
1
,. ..,z
y
).
x
ik
: Binary variable indicating that whether
the cluster k has a skill to repair SKU
type i( i = 1, ..., N) or not, where
X
k
= (x
1k
,. ..,x
Nk
)
T
and X = [X
1
|. ..|X
y
].
y: Number of clusters in the repair shop.
Problem parameters:
N: Number of distinct type of repairables (SKUs).
λ
i
Failure rate of SKU type i ( i = 1, . .., N).
µ
i
: Service rate of SKU type i ( i = 1,.. .,N).
h
i
: Inventory holding cost of SKU type i per unit
time per part ( i = 1,. . .,N).
b: Penalty cost for each back ordered demand per
unit time, which is equivalent to paying per unit
time per technical system that is down because
of a lack of spare parts.
f : Operation cost of a server per unit time (e.g.,
annual wage).
c
i
: Cost of having skills to repair SKU type i per
unit time per server (i = 1, ..., N) (e.g., annual
qualification bonus).
ε: Very small positive real number.
The objective function in Eq.(1) has four cost
terms namely server (capacity), cross-training, hold-
ing and backorder costs. Objective function considers
several trade-offs between the cost terms such as the
cost of holding excess inventory and the cost of down-
time, and also the trade-off between the cost of hav-
ing single or several clusters that include dedicated or
cross-trained servers.
min
S, X, Z
y
∑
k=1
f z
k
+
y
∑
k=1
z
k
N
∑
i=1
c
i
x
ik
!
+
N
∑
i=1
h
i
S
i
+ b
N
∑
i=1
EBO
i
[S
i
,X, Z] (1)
The penalty (backorder) cost term is calculated using
the penalty cost b and the expected total number of
backordered parts EBO
i
[S
i
,X, Z] for each SKU type
A Pooling Strategy for Flexible Repair Shop Designs
273