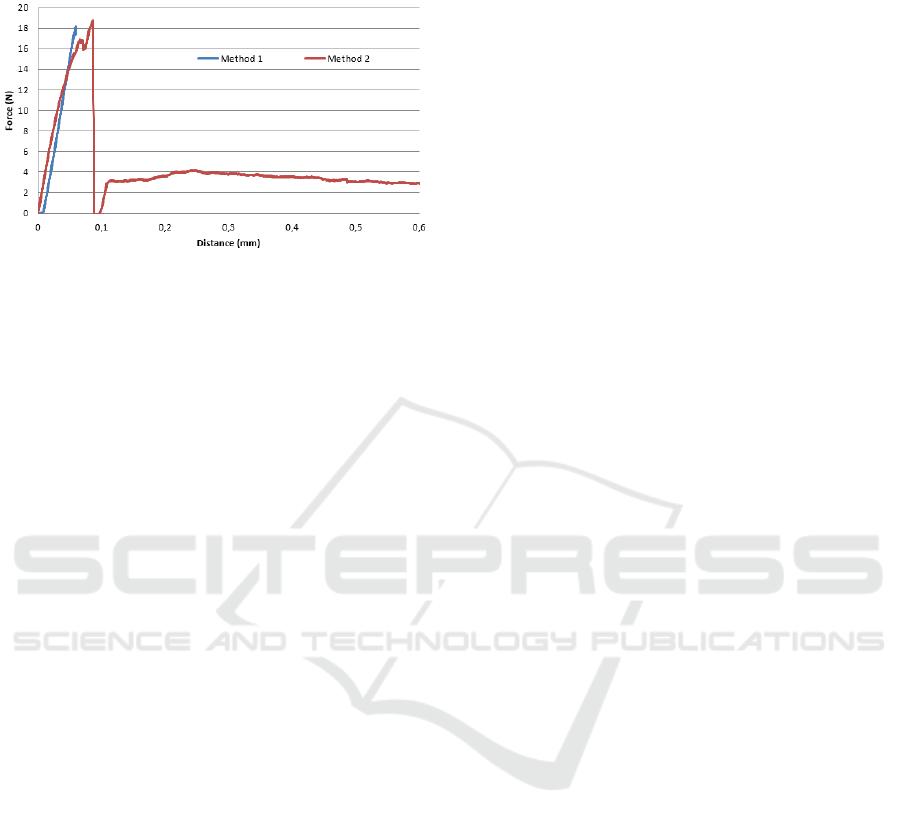
first assembly method was selected as the most
optimal.
Figure 10: The graphical results of the push test for
methods 1 and 2. The graphic represents the moving
distance of the Push tests machine (Zwick Roell Z020) and
the derivate force applied onto the LN assembled crystal.
4.2 Thermal Tests
Thermal annealing tests were performed on four
samples at 300 °C to prove the devices operation
requirements. First the temperature was slowly
increased from room temperature at a rate of
100 °C/h, to finally be kept at a constant 300 °C for
12 h. Afterwards the samples were optically
inspected to check for cracks of the LN chips induced
by thermal stress. As all samples passed the test
successfully they were exposed to a strong
temperature gradient by putting the devices from
room temperature directly into a hot environment at
300 °C and out again. All devices could withstand
three cycles without cracks. Further test are planned
with larger number of samples applying different
temperatures.
5 CONCLUSIONS
Both, the optimal shear strength and wetting
parameters to assemble the lithiumniobate crystal to
a stainless steel sub-mount were shown to be at
3000 mA and 0.5 ms. The general pattern is that
lower laser energies results in higher shear strength
and smaller wetting diameters for the solder bumps.
Soldering Au
80
Sn
20
to stainless steel results in larger
wetting diameters and higher shear strength than
when soldered to lithiumniobate, likely due to the
higher thermal conductivity of stainless steel.
The two assembly methods produced remarkably
similar results in their strength, however considering
that the second method uses more material and time
to be performed, the optimal method is chosen to be
the first one. The final selected method showed to be
capable of handling the required strength demands
imposed by the final device application.
Moreover, other author’s publications focused on
the study of the birefringence effects produced by the
described soldering procedure showed how solderjet
bumping process can assemble optical components
with just a residual stress without affecting the device
optical performances (Ribes-Pleguezuelo, 2016;
Ribes-Pleguezuelo, 2017). Previous studies and
publications make us consider that the same residual
effect will not alter the device functionality for the
present assembled devices.
ACKNOWLEDGEMENTS
The authors want to acknowledge other members of
the Fraunhofer IOF for their support, especially to
Marcel Hornaff for the provided help with the DOE.
To the Deutscher Akademischer Austauschdienst
(DAAD).
This project is partly supported within the
COMET – Competence Centers for Excellent
Technologies - Program by BMVIT, BMWFJ and the
Province of Carinthia.
REFERENCES
Banse, H., Beckert, E., Eberhardt, R., Stöckl, W., Vogel, J.,
2005. Laser Beam Soldering – a New Assembly
Technology for Microoptical Systems. In Microsystems
Technologies 11, pp. 186-193.
Bardong, J., Binder, A., Toskov, S., Miskovic, G.,and
Radosavljevic, G., 2016. Investigation of low-tempera-
ture cofired ceramics packages for high-temperature
SAW sensors. In J. Sens. Sens. Syst., 5, p 85–93.
Beckert, E., Oppert, T., Azdasht, G., Zakel, E., Burkhardt,
T., Hornaff, M., Kamm, A., Scheidig, I., Eberhardt, R.,
Tünnermann, A., Buchmann, F., 2009. Solder Jetting -
A Versatile Packaging and Assembly Technology for
Hybrid Photonics and Optoelectronical Systems. In
IMAPS 42nd International Symposium on
Microelectronics, Proceedings, Vo. 42, pp. 406-412.
Bruckner, G., Schicker, J., Schlumpf, P., 2013, Stress
sensitivity of SAW Rayleigh waves on Lithiumniobate
and its application in pressure sensor design.
Proceedings IEEE International Ultrasonics
Symposium (IUS), Prague, pp. 2140-2143.
Bruckner,G., Bardong, J., Binder, A., Nicolay, P., 2017,
SAW Delay Lines as Wireless Sensors for Industrial
Applications. Proceedings of the VIII ECCOMAS
Thematic Conference on Smart Structures and
Materials, SMART 2017, Madrid, pp. 1433-1442.
PHOTOPTICS 2018 - 6th International Conference on Photonics, Optics and Laser Technology
96