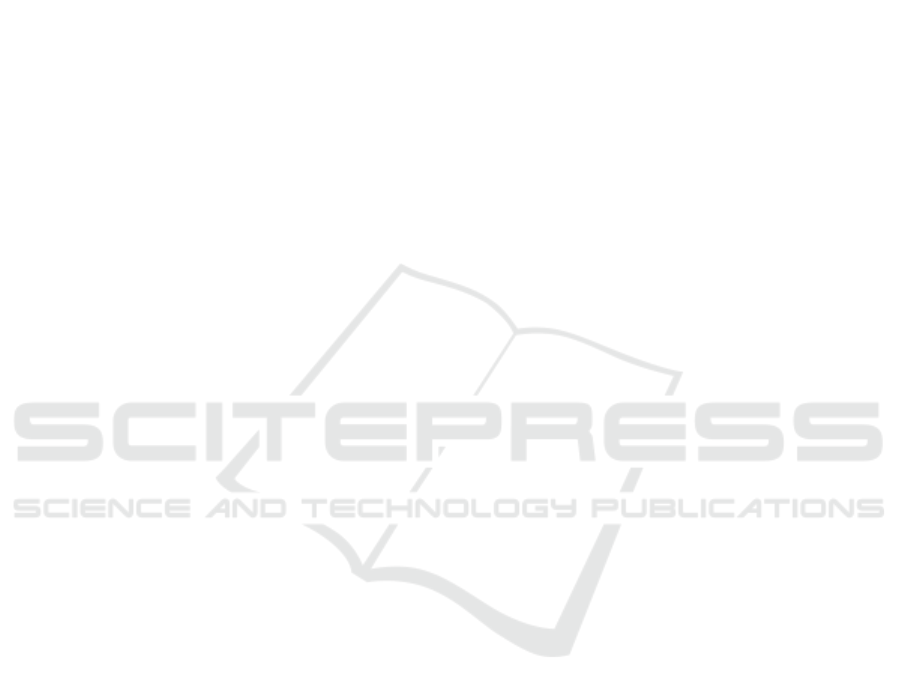
Performance Evaluation of Square Coupled Coils at Different
Misalignments for Electric Vehicle Battery Charging
P. Srinivasa Rao Nayak, Kishan Dharavath, Radhakrushna Dey,
K. Sundareswaran and Sishaj P. Simon
Electrical and Electronics Engineering, National Institute of Technology - Trichy, 620015, Trichy, Tamil Nadu, India
Keywords: Wireless Power Transfer, Mutual Inductance, Electric Vehicle, Misalignment.
Abstract: Wireless Power Transfer (WPT) for electric vehicle battery charging is an advancing battery charging
technology. The crucial part in the WPT system is the coupling coil structure and it plays a major role in
effective power transfer. This paper describes the mutual inductance and flux distribution characteristics of
the square coupled coils with different misalignments also to make more realistic for Electric Vehicle (EV)
battery charging applications the coupled coils are designed with and without core and chassis. The
evaluation contains the mutual inductance gets affected by distance between the coils, lateral and angular
misalignment effects. The results of the analysis are used in the implementation of the wireless EV battery
charging system.
1 INTRODUCTION
The popularity of Electric propulsion vehicle in
automobile industry sector has always been
increasing due to many positive aspects of energy
efficiency, environment friendliness, performance,
and reduced energy dependence on fossil fuels.
However, the use of EV faces some challenges like
driving range, recharge time, battery cost, more
bulk, and weight (Khaligh, 2012), (S. Li, 2014).
Thus, with the growing EV market, we need to
overcome the problems by stimulating new ideas
and developments in this area. On that concern EV
battery charging is an emerging research area. In
conventional conductive battery charging introduces
the inconvenience and risk hazards and this type of
problems can be overcome by a simple concept
wireless battery charging (Roman, 2016), (Seho
Kim, 2017). The principle of the wireless power
transfer (WPT) is like conventional transformer i.e.,
mutual induction. When a current carrying
conductor or coil is excited with alternating source it
will produce magnetic field around the conductor or
coil. When another coil is brought in the vicinity of
the magnetic field of the first coil an EMF will be
induced due to alternating nature of the magnetic
field (F. Y. Lin, 2015), (Fariborz, 2014). In the WPT
system coil connected to the source is referred as
transmitter coil (Tx), and the coil connected to the
load called as receiver coil (Rx).
However, the potency of the power transfer over
this inductive link predominantly depends on flux
linkages between the coupled coils and structure of
the coils. Based on the specific application, the coil
structures like circular, rectangular, DD & DQ and
square shapes (C. Y. Huang, 2015), (Ezhil, 2015)
can be used. The shape of the coil and misalignment
greatly affects the mutual inductance and flux
linkage between the coupled coils. The amount of
power transfer and efficiency mainly depends on MI
(Dharavath, 2016). So, it is necessary to obtain the
MI for designing of the any wireless power transfer
system in particularly EV battery charging
application. The design and optimization of circular
magnetic structure is described (M. Budhia, 2011)
for wireless EV battery charging applications. Based
on the 3D field the mutual inductance between the
circular coupled coils is obtained for IPT system
(Yang Han, 2015) and presented the misalignment
conditions for circular coupled coils. (Merugu,
2016) explained the effect of spiral square coil
dimensions of the square coupled coils on power
transfer capability, efficiency.
In this paper coupling characteristics of square
inductive coupled coils are described with different
misalignments. The basic schematic diagram
representation of wireless electric vehicle battery
290
Nayak, P., Dharavath, K., Dey, R., Sundareswaran, K. and Simon, S.
Performance Evaluation of Square Coupled Coils at Different Misalignments for Electric Vehicle Battery Charging.
DOI: 10.5220/0006672402900297
In Proceedings of the 4th International Conference on Vehicle Technology and Intelligent Transport Systems (VEHITS 2018), pages 290-297
ISBN: 978-989-758-293-6
Copyright
c
2019 by SCITEPRESS – Science and Technology Publications, Lda. All rights reserved