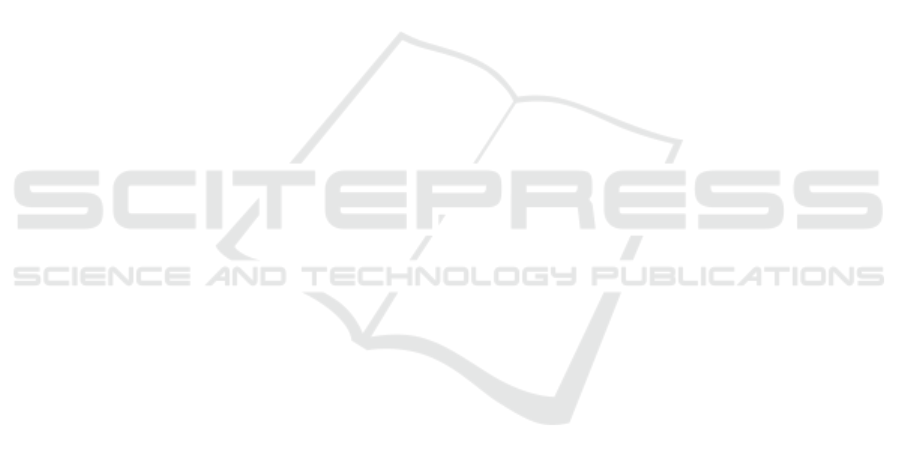
optimization with storage and active DSM for the
residential sector. Solar Energy, 85(9), 2338-2348.
Costanzo, G. T., Kheir, J., and Zhu, G. (2011, June). Peak-
load shaving in smart homes via online scheduling. In
Industrial Electronics (ISIE), 2011 IEEE International
Symposium on (pp. 1347-1352). IEEE.
Di Giorgio, A., and Liberati, F. (2014). Near real time load
shifting control for residential electricity prosumers
under designed and market indexed pricing models.
Applied Energy, 128, 119-132.
Arnold, M., and Andersson, G. (2011, August). Model
predictive control of energy storage including
uncertain forecasts. In Power Systems Computation
Conference (PSCC), Stockholm, Sweden (Vol. 23, pp.
24-29).
Herter, K. (2007). Residential implementation of critical-
peak pricing of electricity. Energy Policy, 35(4),
2121–2130.
Wirth, H., and Schneider, K. (2015). Recent facts about
photovoltaics in Germany. Fraunhofer ISE, 92.
Morais, H., Faria, P., and Vale, Z. (2014). Demand
response design and use based on network locational
marginal prices. International Journal of Electrical
Power and Energy Systems, 61, 180-191.
Palensky, P., and Dietrich, D. (2011). Demand side
management: Demand response, intelligent energy
systems, and smart loads. IEEE transactions on
industrial informatics, 7(3), 381-388.
Parisio, A., Rikos, E., Tzamalis, G., and Glielmo, L.
(2014). Use of model predictive control for
experimental microgrid optimization. Applied Energy,
115, 37-46.
Petrollese, M., Valverde, L., Cocco, D., Cau, G., and
Guerra, J. (2016). Real-time integration of optimal
generation scheduling with MPC for the energy
management of a renewable hydrogen-based
microgrid. Applied Energy, 166, 96-106.
Riffonneau, Y., Bacha, S., Barruel, F., and Ploix, S.
(2011). Optimal power flow management for grid
connected PV systems with batteries. IEEE
Transactions on Sustainable Energy, 2(3), 309-320.
Schmelas, M., Feldmann, T., da Costa Fernandes, J., and
Bollin, E. (2015). Photovoltaics energy prediction
under complex conditions for a predictive energy
management system. Journal of Solar Energy
Engineering, 137(3), 031015.
Spring, A., Becker, G., and Witzmann, R. (2014, June).
Grid Voltage Influences Of Reactive Power Flows Of
Photovoltaic Inverters With A Power Factor
Specification Of One. In Cired Workshop-Rome (pp.
11-12)..
Stetz, T., Marten, F., and Braun, M. (2013). Improved low
voltage grid-integration of photovoltaic systems in
Germany. IEEE Transactions on Sustainable Energy,
4(2), 534-542.
Tonkoski, R., Lopes, L. A. C., and El-Fouly, T. H. M.
(2010, July). Droop-based active power curtailment
for overvoltage prevention in grid connected PV
inverters. In Industrial Electronics (ISIE), 2010 IEEE
International Symposium on (pp. 2388-2393). IEEE.
Turitsyn, K., Sulc, P., Backhaus, S., and Chertkov, M.
(2010, October). Local control of reactive power by
distributed photovoltaic generators. In Smart Grid
Communications (SmartGridComm), 2010 First IEEE
International Conference on (pp. 79-84). IEEE.
Weckx, S., Gonzalez, C., and Driesen, J. (2014).
Combined central and local active and reactive power
control of PV inverters. IEEE Transactions on
Sustainable Energy, 5(3), 776-784.
Weniger, J., Bergner, J., and Quaschning, V. (2014).
Integration of PV power and load forecasts into the
operation of residential PV battery systems. In 4th
Solar Integration Workshop (pp. 383-390).
Wu, Z., Tazvinga, H., and Xia, X. (2015). Demand side
management of photovoltaic-battery hybrid system.
Applied Energy, 148, 294-304.
Yang, J., Zhang, G., and Ma, K. (2014). Matching supply
with demand: A power control and real time pricing
approach. International Journal of Electrical Power
and Energy Systems, 61, 111-117.
A Model Predictive Control based Peak Shaving Application for a Grid Connected Household with Photovoltaic and Battery Storage
63