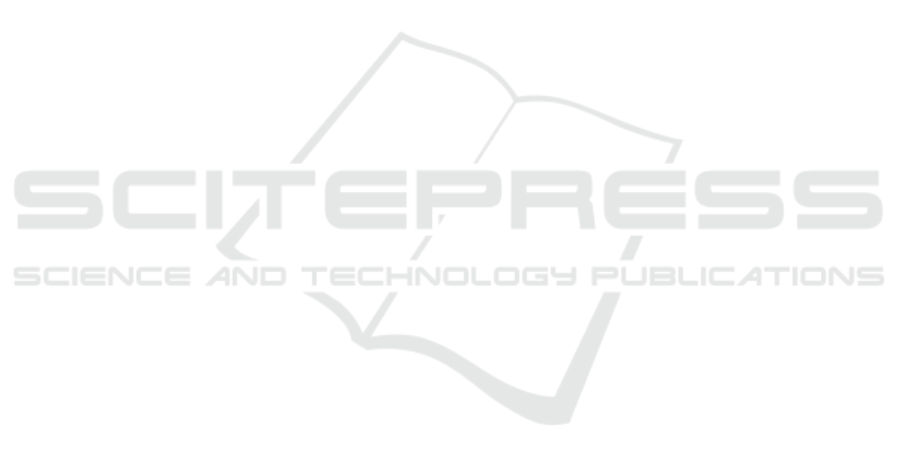
2 RELATED WORK
In related work, driver types are usually divided into
different numbers of classes. For example, into the -
most commonly used - three classes relaxed, normal
and dynamic (Wilde et al., 2008; Park et al., 2017) or
into five classes aggressive, sporty, moderate, anxious
and energy efficient (B
¨
ar et al., 2011; Ara
´
ujo et al.,
2012).
A driver type is primarily definied by the aver-
age acceleration. For urban areas for example, de-
fined ranges are: calm 0.45 to 0.65 m/s
2
, normal 0.65
to 0.80 m/s
2
and aggressive driver 0.85 to 1.10 m/s
2
(de Vlieger et al., 2000). For motorways, on the
other hand, the acceleration for all three driver types
is only in the range from 0.08 to 0.20m/s
2
(Langari
and Won, 2005). Most of the related work use fuzzy
logic to classify the driver (B
¨
ar et al., 2011; Langari
and Won, 2005). A further approach is to use the ra-
tio of the standard deviation of the acceleration and
the average acceleration in order to get a better com-
parability (Langari and Won, 2005).
In this paper, we do not separate the driver
into predefined groups nor we evaluate his driv-
ing behaviour with a fuzzy set. This is one of
the main differences between this work and the
above-mentioned works. After the classification into
driver types, the properties are no longer modified.
Assuming that a driver is assigned to a specific
group of drivers, but his driving style changes within
the boundaries of the group, these changes are not
transferred to a subsequent prediction. This would
lead to an error in the energy demand estimation.
This error can be avoided by evaluating driving
data such as speed and acceleration during the jour-
ney rather than dividing it into individual driver types.
Another difference between this and related work
is the use of input quantities. Other work use the brake
pressure (B
¨
ar et al., 2011) or the moving average val-
ues of the gas and brake pedal during acceleration or
deceleration respectively (Wilde et al., 2008). Spa-
tial (speed limits, roundabouts, school zones, ...) and
temporal (purposes, time, day of the week, ...) condi-
tions are used by (Ellison et al., 2015). Mostly, the in-
put quantities are referenced to special situations such
as approaching towns and villages, taking sharp turns
and approaching a stop sign (B
¨
ar et al., 2011) or to
the driving environment (city, rural, motorway) based
on signposted speed limits (Castignani et al., 2013).
A further approach is to calculate the driver pa-
rameters through speed, acceleration and rotation rate
of a smartphone by processing the data from accelera-
tion sensor, magnetic field and GPS receiver (Castig-
nani et al., 2013; Ara
´
ujo et al., 2012).
In our work, we use a combination of speed limits
and the measured speed profile in order to calculate
driver-specific parameters, which form the base for
a new energy demand estimation. In contrast to a
classified type of driver, this allows us to measure the
driver characteristics depending on each speed limit
range. This avoids the mentioned problem of driving
style changes within the borders of a classified driver
type. Thus, we want to reduce the error in our energy
demand estimation.
A further distinguishing feature between this and
related work is the processing of the collected data.
We continuously calculate parameters which serve for
the determination of cornering speed, acceleration,
braking and the resulting upper speed limit. More-
over, the real and simulated energy consumption are
compared in order to determine correction factors,
which then influences the renewed estimation through
feedback. From all above-mentioned works, only
(Langari and Won, 2005) optimize the driver param-
eters by a direct comparison between estimation and
simulation.
Other work, for example, do not aim to use the
collected data for an energy demand estimation in a
closed-loop, rather they score the driver between 0
and 100, to evaluate the driving behaviour in terms
of accident risks and their avoidance (Ellison et al.,
2015) or in terms of cost-efficiency (Castignani et al.,
2013).
While recording trip data, our model distinguishes
whether a vehicle in front is present or not. This dis-
tinction results in two datasets of driver parameters,
with and without a vehicle in front. If the driver slows
down due to a vehicle in front, signal processing is
interrupted to avoid incorrect classification. This
approach has been partially adopted from (Wilde
et al., 2008) in this paper. The advantage of this is
that, depending on the predicted traffic volume, a
distinction can be made between whether the driver
has nearly unrestricted driving or the traffic is largely
determining his driving behaviour.
Within the framework of the presented methodol-
ogy, the results of the energy demand estimation are
applied as an input quantity. Other work that deals
with prediction of expected energy demand and range
estimation (Sehab et al., 2011; Vaz et al., 2015; Fer-
reira et al., 2013; Zhang et al., 2012), are not de-
scribed in detail here.
VEHITS 2018 - 4th International Conference on Vehicle Technology and Intelligent Transport Systems
350