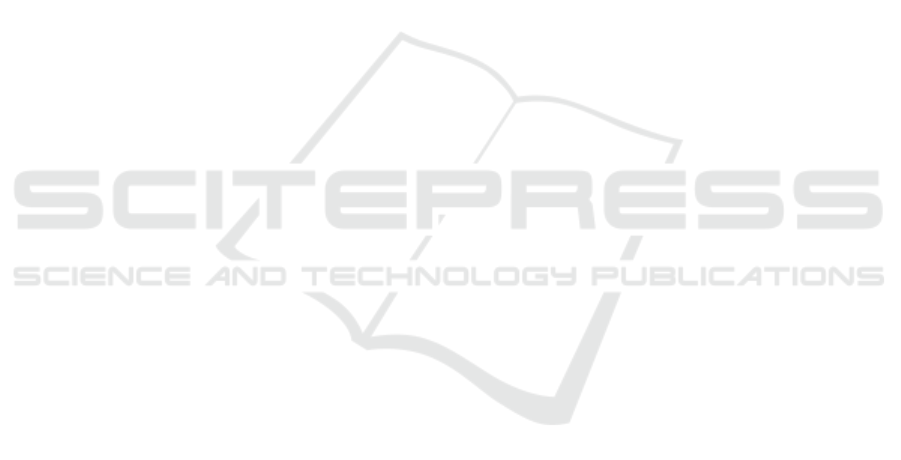
Galceran, E., Eustice, R. M., and Olson, E. (2015). Toward
integrated motion planning and control using poten-
tial fields and torque-based steering actuation for au-
tonomous driving. In 2015 IEEE Intelligent Vehicles
Symposium (IV), pages 304–309. IEEE.
Gayle, R., Sud, A., Lin, M. C., and Manocha, D. (2007).
Reactive deformation roadmaps: motion planning
of multiple robots in dynamic environments. In
Intelligent Robots and Systems, 2007. IROS 2007.
IEEE/RSJ International Conference on, pages 3777–
3783. IEEE.
Guan, W., Weng, Z., and Zhang, J. (2015). Obsta-
cle avoidance path planning for manipulator based
on variable-step artificial potential method. In The
27th Chinese Control and Decision Conference (2015
CCDC), pages 4325–4329. IEEE.
Habib, M. K. (2014). Handbook of Research on Advance-
ments in Robotics and Mechatronics. IGI Global.
Hargas, Y., Mokrane, A., Hentout, A., Hachour, O., and
Bouzouia, B. (2015). Mobile manipulator path plan-
ning based on artificial potential field: Application on
robuter/ulm. In 2015 4th International Conference on
Electrical Engineering (ICEE), pages 1–6. IEEE.
IFR (2017). Executive summary world robotics 2017 indus-
trial robots: How robots conquer industry worldwide.
Frankfurt. International Federation of Robotics Press.
ISO (1998). Iso9283: Manipulating industrial robots-
performance criteria and related test methods.
Kennedy, R. K. (2017). Understanding, Measuring, and
Improving Overall Equipment Effectiveness: How to
Use OEE to Drive Significant Process Improvement.
Productivity Press, New York, 1st edition.
Khatib, O. (1986). Real-time obstacle avoidance for mani-
pulators and mobile robots. The international journal
of robotics research, 5(1):90–98.
Koppula, H. S. and Saxena, A. (2016). Anticipating human
activities using object affordances for reactive robotic
response. IEEE transactions on pattern analysis and
machine intelligence, 38(1):14–29.
Mac, T. T., Copot, C., Hernandez, A., and De Keyser, R.
(2016). Improved potential field method for unknown
obstacle avoidance using uav in indoor environment.
In 2016 IEEE 14th International Symposium on Ap-
plied Machine Intelligence and Informatics (SAMI),
pages 345–350. IEEE.
Mittal, R. and Nagrath, I. (2003). Robotics and control. Tata
McGraw-Hill.
Moellmann, A. H., Albuquerque, A. S., Contador, J. L.,
and Marins, F. A. S. (2006). Aplicac¸
˜
ao da teoria das
restric¸
˜
oes e do indicador de efici
ˆ
encia global do equi-
pamento para melhoria de produtividade em uma linha
de fabricac¸
˜
ao. Revista gest
˜
ao industrial, 2(1).
Mora, M. C. and Tornero, J. (2008). Path planning and
trajectory generation using multi-rate predictive arti-
ficial potential fields. In Intelligent Robots and Sy-
stems, 2008 IEEE/RSJ International Conference on,
pages 2990–2995. IEEE.
Nawrocka, A., Nawrocki, M., and Kot, A. (2014). Fuzzy lo-
gic controller for rehabilitation robot manipulator. In
Control Conference (ICCC), 2014 15th International
Carpathian, pages 379–382. IEEE.
Pinto, L., Davidson, J., and Gupta, A. (2016). Supervision
via competition: Robot adversaries for learning tasks.
arXiv preprint arXiv:1610.01685.
Simoes, M. G. and Shaw, I. S. (2007). Controle e Modela-
gem Fuzzy. Edgard Blucher, Sao Paulo, 2nd edition.
Spong, M. W. (2006). Robot modeling and control, vo-
lume 3. Wiley New York.
Volpe, R. and Khosla, P. (1990). Manipulator control with
superquadric artificial potential functions: Theory and
experiments. IEEE Transactions on Systems, Man,
and Cybernetics, 20(6):1423–1436.
Wang, X., Jin, Y., and Ding, Z. (2015). A path planning
algorithm of raster maps based on artificial potential
field. In Chinese Automation Congress (CAC), 2015,
pages 627–632. IEEE.
Yu, K., Ohnishi, K., Kawana, H., and Usuda, S. (2015a).
Modulated potential field using 5 dof implant assist
robot for position and angle adjustment. In Industrial
Electronics Society, IECON 2015-41st Annual Confe-
rence of the IEEE, pages 002166–002171. IEEE.
Yu, K., Uozumi, S., Ohnishi, K., Usuda, S., Kawana, H.,
and Nakagawa, T. (2015b). Stereo vision based ro-
bot navigation system using modulated potential field
for implant surgery. In Industrial Technology (ICIT),
2015 IEEE International Conference on, pages 493–
498. IEEE.
ICINCO 2018 - 15th International Conference on Informatics in Control, Automation and Robotics
556