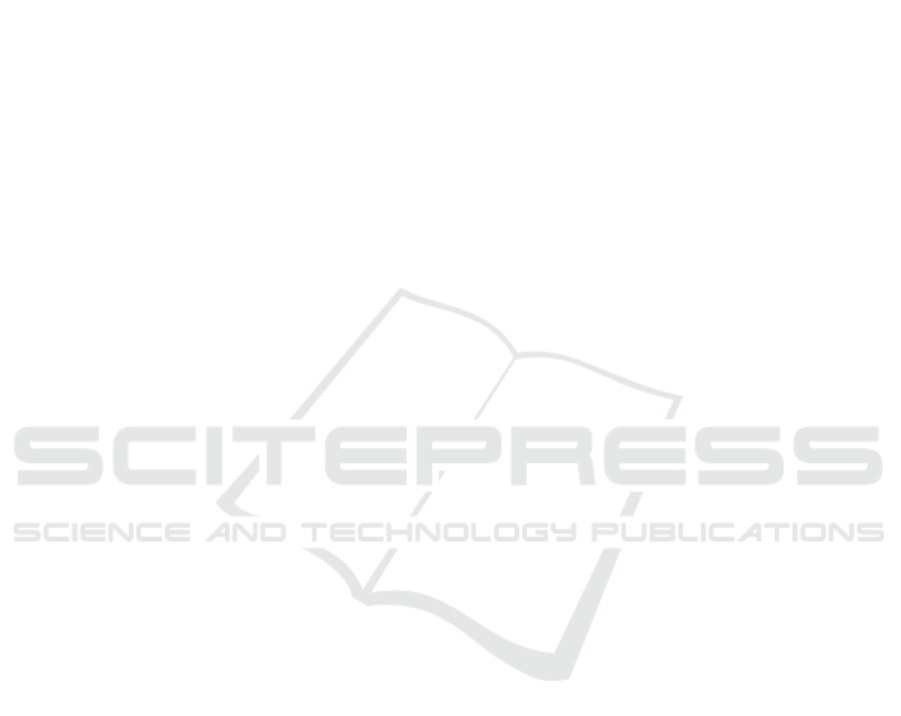
Test Evaluation and Computational Modeling Applicability for
Compression Moldability of Inert Explosive
Jin Sung Lee and Jung Su Park
Agency for Defense Development, Yuseong P.O. Box 35-4, Daejeon, South Korea
Keywords: Shima-Oyane Yield Model, Powder, Moldability Behaviour, Double Action Pressing, Isostatic Pressing,
Computational Model Analysis.
Abstract: Using an inert explosive powder, molding experiments were carried out. And a computational model analysis
was performed to predict moldability behaviour of an inert explosive powder. In order to analysis the Shima-
Oyane yield model to predict the behaviour of the densification for inert explosive powder, using an inert
explosive powder was carried out moldability tests on the pressure, could be obtained volumetric strain on
the pressure, relative density and so on. Based on the results of the curve fitting, it could be derived the
parameters for the yield function of the cap with the critical state. Finite element analysis for both double
action pressing and isostatic pressing process of the two yield models were performed. And changes in relative
density and densification behaviour of an inert explosive powder were analysed. In addition, it investigated
the distribution of the relative density or volumetric strain caused by the overall and local variations. It was
founded the maximum stress and position etc. under working pressure of inert explosive powder.
1 INTRODUCTION
In the manufacturing technologies of P/M products,
isostatic pressing and die compression are widely
used. However, P/M parts formed by die compression
have inhomogeneous density distributions due to the
friction between the powder and die wall.
Process simulations by using a finite element
analysis may be useful to control the shape during
P/M forming process (Lewis, 1993), (Gethin, 1994).
The numerical modelling of the powder compression
process requires the appreciate constitutive models
for densification of a powder material. A number of
yield functions have been developed for densification
behaviour of powder material, so far.
By including the effect of hydrostatic stress on
plastic deformations of porous materials (Kuhn and
Downey, 1971), (Shima-Oyane, 1976), and
(Doraivelu et al., 1984) proposed yield functions from
uniaxial tests of powder compressions. (Fleck et
al.,1992) proposed a microscopic constitutive model
from particle deformations. The yield function by
Fleck et al., however, did not agree well with
experimental data of soft metal powder during die
compaction (Kwon, 1997). A number of researchers
also adopted models for densification of powder from
soil mechanics. Watson et al., (1993) investigated
yield criteria of powder by using the Drucker-Prager-
/Cap model.
In this paper, using an inert explosive powder as a
soft powder material, molding experiments were
carried out. And a computational model analysis was
performed to predict moldability behaviour of an inert
explosive powder.
To apply Shima-Oyane, Drucker-Prager/Cap
yield model to predict the behaviour of the
densification for inert explosive powder, using an
inert explosive powder were carried out moldability
tests. Finite element analysis for double action
pressing and isostatic pressing process were
performed.
2 ANALYSIS
2.1 Constitutive Model
In die compression, the deformation behaviour of the
powder body is based on the yield criterion. Unlike
bulk solids, the yield criterion includes the
hydrostatic pressure due to volume change in
compression. Among many yield criteria for
Lee, J. and Park, J.
Test Evaluation and Computational Modeling Applicability for Compression Moldability of Inert Explosive.
DOI: 10.5220/0006832504290434
In Proceedings of 8th International Conference on Simulation and Modeling Methodologies, Technologies and Applications (SIMULTECH 2018), pages 429-434
ISBN: 978-989-758-323-0
Copyright © 2018 by SCITEPRESS – Science and Technology Publications, Lda. All rights reserved
429