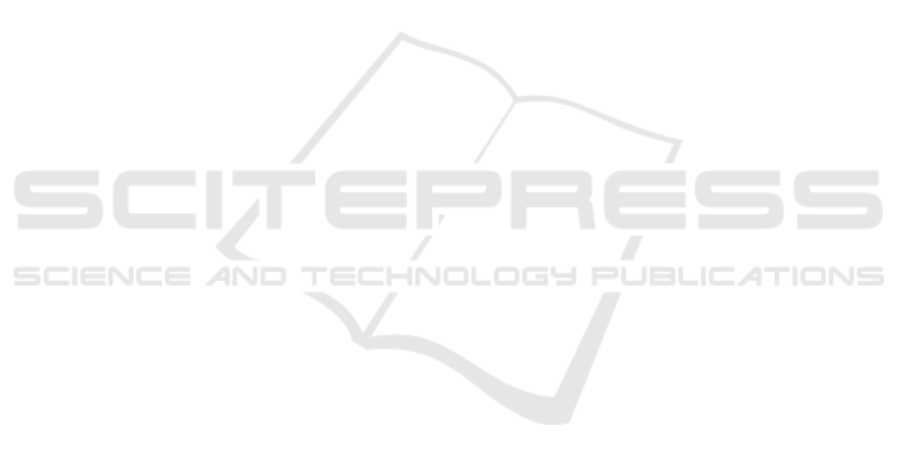
these techniques.
Over the last two decades, numerous prognos-
tic approaches have been developed. Prognostic is
a major scientific challenge for industrial implemen-
tation of maintenance strategies in which the remai-
ning useful life estimation (RUL) is an important task.
For environmental, economic and operational purpo-
ses, the prognostic and the remaining useful lifetime
prediction arouse a big interest. In the framework
of prognostic and health management (PHM), many
prognostic techniques exist and they are basically
classified into three principal classes: data-driven ap-
proaches, model-based approaches, experience-based
approaches, but these can also be classified in two
groups, non-probabilistic methods and probabilistic
methods, see (K.L.Son, 2013). In non-probabilistic
methods the deterioration phenomenon is not random
and in most observations the deterioration can be
fuzzy. With probabilistic methods, the deterioration
phenomenon is considered to be random and with sto-
chastic tools it is considered a random behavior. In
this case the prognostic is based on the future beha-
vior of the stochastic deterioration process and can
give results in terms of probabilities, see (K.L.Son,
2013).
1.1 Knowledge-driven Support Systems
and the Industry 4.0
In modern manufacturing, real-time control of pro-
duction operation to improve system responsiveness,
increase system efficiency and reduce downtime is be-
coming more and more critical. More recently, this
concept is moving forward to the concept of ”Industry
4.0”. It is a current trend and data exchange in ma-
nufacturing technologies. It includes cyber-physical
systems, the internet of things and cloud computing
creating what has been called a ”smart factory”. Most
manufacturing industries have sought to improve a
productivity and quality with this new techniques
where data-driven decision support systems (DSS)
appear as a new paradigm. In (S.H.Muhammad,
2017) we can find a recent review on the use of DSS
in manufacturing. One of the data-driven DSS is the
one called Knowledge-driven DSS. It has its origin in
the Intelligent Decision Support Systems or in a broa-
der sense, in Artificial intelligence (AI),(H.R.Nemati,
2002) ,(M.Negnevitsky, 2005) . Knowledge-driven
DSS are computed-based reasoning systems with the
distinction that AI technologies, management expert
systems, data mining technologies and communica-
tion mechanism are integrated. Intelligent DSS are
divided in some evolutionary developments. One of
them is about rule-based expert systems (A.Chakir,
2016). These systems are based on the use of heuris-
tics, which can be understood as strategies that lead
to the correct solution for the problem. For this sys-
tems it is always necessary to use human expert kno-
wledge collected in a database, (M.Chergui, 2016).
Knowledge-driven DSS are successfully applied for
many applications like for instance, market manage-
ment, (M.Murthadha, 2013) or for radiation therapy
treatment planning (R.R.Deshpande, 2016).
The present study proposes a novel protocol on
how to design Knowledge-driven Maintenance Sup-
port Systems (MSS). Based on real-time measure-
ment of sub-cycle times, with the help of expert kno-
wledge and the statistical analysis of the measure-
ments, we could define rules that allow us to predict
the deterioration of a particular machine part or com-
ponent. In adition to that and, based on the same sta-
tistical analysis and the numerical simulation techni-
ques, allows us to know the loss of production produ-
ced by the component deterioration.
The present paper is organized as follows. Section
2 describes our previous works, in particular, the mat-
hematical model that will allow us to study sub-cycle
times,(E.Garcia, 2016), (E.Garcia and N.Montes,
2017).
Section 3 desribes the change point concept and
their link with the sub-cycle time.
Section 4 shows the experimental platform used to
design our Knowledge-driven MSS. This platform is
based on a welding unit used at Ford Motor Company
located at Almusafes (Valencia).
Section 5 describes the statistical analysis used to
define the rules of our Knowledge-driven MSS.
Section 6 describes the numerical simulation de-
veloped to compute the loss of production rate when
the change point occurs in a welding station.
Section 7 presents the conclusions with an empha-
sis on future research challenges towards a real-time
Preventive Maintenance Schedule System.
2 PREVIOUS WORK. FROM
MICRO-TERM TO
LONG-TERM
The data used in the analysis of the production lines
is classified into long-term and short-term. Long-term
is mainly used for process planning, while short-term
focuses, primarily, on process control. Following the
definition in (L.Li and J.Ni., 2009), short-term is re-
ferred to an operational period not large enough for
machine failure period to be described by a statis-
tic distribution. The machine cycle time is conside-
ICINCO 2018 - 15th International Conference on Informatics in Control, Automation and Robotics
44