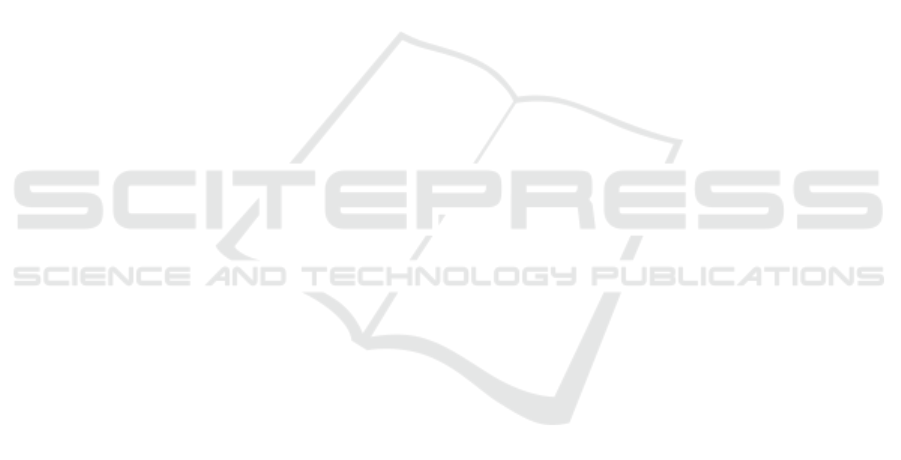
ACKNOWLEDGEMENTS
This work was supported by the European Commis-
sion within the H2020 REFILLS project ID n. 731590
and the H2020 LABOR project ID n. 785419.
REFERENCES
Aldoma, A., Marton, Z.-C., Tombari, F., Wohlkinger, W.,
Potthast, C., Zeisl, B., Rusu, R., Gedikli, S., and
Vincze, M. (2012). Tutorial: Point cloud library:
Three-dimensional object recognition and 6 DOF pose
estimation. IEEE Robotics & Automation Magazine,
19(3):80–91.
Beeson, P. and Ames, B. (2015). TRAC-IK: An open-
source library for improved solving of generic inverse
kinematics. In 2015 IEEE-RAS 15th International
Conference on Humanoid Robots (Humanoids), pages
928–935. IEEE.
Bergstrom, N., Bjorkman, M., and Kragic, D. (2011). Gen-
erating object hypotheses in natural scenes through
human-robot interaction. In 2011 IEEE/RSJ Interna-
tional Conference on Intelligent Robots and Systems,
pages 827–833. IEEE.
Buch, A. G., Kraft, D., Kamarainen, J.-K., Petersen, H. G.,
and Kruger, N. (2013). Pose estimation using local
structure-specific shape and appearance context. In
2013 IEEE International Conference on Robotics and
Automation, pages 2080–2087. IEEE.
Comaniciu, D. and Meer, P. (2002). Mean shift: A robust
approach toward feature space analysis. IEEE Trans-
actions on Pattern Analysis and Machine Intelligence,
24:603–619.
Costanzo, M., De Maria, G., and Natale, C. (2018). Slip-
ping control algorithms for object manipulation with
sensorized parallel grippers. In 2018 IEEE Interna-
tional Conference on Robotics and Automation. IEEE.
Falco, P. and Natale, C. (2014). Low-level flexible planning
for mobile manipulators: a distributed perception ap-
proach. Advanced Robotics, 28:1431–1444.
Hornung, A., Wurm, K. M., Bennewitz, M., Stachniss, C.,
and Burgard, W. (2013). OctoMap: An efficient prob-
abilistic 3D mapping framework based on octrees. Au-
tonomous Robots, 34:189–206. Software available at
http://octomap.github.com.
Kalakrishnan, M., Chitta, S., Theodorou, E., Pastor, P., and
Schaal, S. (2011). STOMP: Stochastic trajectory opti-
mization for motion planning. In 2011 IEEE Interna-
tional Conference on Robotics and Automation, pages
4569–4574. IEEE.
Kavraki, L., Svestka, P., Latombe, J.-C., and Overmars, M.
(1996). Probabilistic roadmaps for path planning in
high-dimensional configuration spaces. IEEE Trans-
actions on Robotics and Automation, 12(4):566–580.
Khatib, O. (1986). Real-time obstacle avoidance for manip-
ulators and mobile robots. Int. J. Rob. Res., 5:90–98.
Khokar, K., Beeson, P., and Burridge, R. (2015). Imple-
mentation of KDL inverse kinematics routine on the
atlas humanoid robot. Procedia Computer Science,
46:1441–1448.
Kuffner, J. and LaValle, S. (2000). RRT-connect: An effi-
cient approach to single-query path planning. In Pro-
ceedings 2000 ICRA. Millennium Conference. IEEE
International Conference on Robotics and Automa-
tion. Symposia Proceedings (Cat. No.00CH37065),
pages 995–1001. IEEE.
Mishra, A. and Aloimonos, Y. (2011). Visual segmentation
of simple objects for robots. In Robotics: Science and
Systems VII, pages 1–8. Robotics: Science and Sys-
tems Foundation.
Muja, M. and Lowe, D. G. (2009). Fast approximate near-
est neighbors with automatic algorithm configuration.
In In VISAPP International Conference on Computer
Vision Theory and Applications, pages 331–340.
Nakhaeinia, D., Payeur, P., and Laganiére, R. (2018).
A mode-switching motion control system for reac-
tive interaction and surface following using indus-
trial robots. IEEE/CAA Journal of Automatica Sinica,
5:670–682.
Pan, J., Chitta, S., and Manocha, D. (2012). FCL: A general
purpose library for collision and proximity queries. In
2012 IEEE International Conference on Robotics and
Automation, pages 3859–3866. IEEE.
Papazov, C. and Burschka, D. (2011). An efficient
RANSAC for 3d object recognition in noisy and oc-
cluded scenes. In Computer Vision – ACCV 2010,
pages 135–148. Springer Berlin Heidelberg.
Phillips, J. M., Bedrosian, N., and Kavraki, L. (2004).
Guided expansive spaces trees: A search strategy for
motion- and cost-constrained state spaces. In 2004
IEEE Intl. Conf. on Robotics and Automation, pages
3968–3973. IEEE.
Rusinkiewicz, S. and Levoy, M. (2001). Efficient variants
of the ICP algorithm. In Proceedings Third Interna-
tional Conference on 3-D Digital Imaging and Mod-
eling, pages 145–152. IEEE Comput. Soc.
Rusu, R. B., Blodow, N., and Beetz, M. (2009). Fast point
feature histograms (FPFH) for 3d registration. In 2009
IEEE International Conference on Robotics and Au-
tomation, pages 3212–3217. IEEE.
Rusu, R. B., Bradski, G., Thibaux, R., and Hsu, J. (2010).
Fast 3d recognition and pose using the viewpoint fea-
ture histogram. In 2010 IEEE/RSJ International Con-
ference on Intelligent Robots and Systems, pages 1–4.
IEEE.
Rusu, R. B. and Cousins, S. (2011). 3d is here: Point cloud
library (PCL). In 2011 IEEE International Conference
on Robotics and Automation. IEEE.
¸Sucan, I. A. and Kavraki, L. E. (2009). Kinodynamic mo-
tion planning by interior-exterior cell exploration. In
Springer Tracts in Advanced Robotics, pages 449–
464. Springer Berlin Heidelberg.
Tombari, F., Salti, S., and Stefano, L. D. (2010). Unique
signatures of histograms for local surface description.
In Computer Vision – ECCV 2010, pages 356–369.
Springer Berlin Heidelberg.
Flexible Motion Planning for Object Manipulation in Cluttered Scenes
121