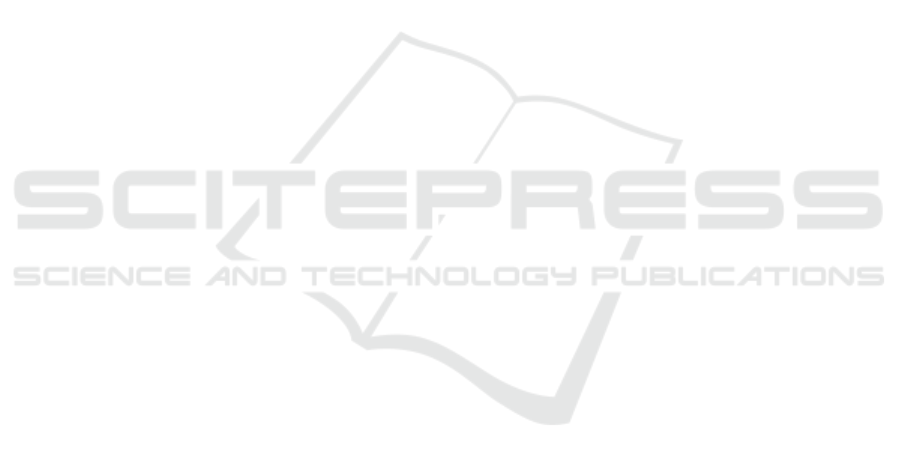
Wireless Communications and Networking Confer-
ence, WCNC 2016, pages 01 – 06.
Ammari, H. M. and Das, S. K. (2012). Centralized and
Clustered k-Coverage Protocols for Wireless Sensor
Networks. IEEE Transactions on Computers, 61(1).
Aziz, A. A., Sekercioglu, Y. A., Fitzpatrick, P., and
Ivanovich, M. (2013). A Survey on Distributed Topol-
ogy Control Techniques for Extending the Lifetime of
Battery Powered Wireless Sensor Networks. IEEE
Communications Surveys & Tutorials, 15(1):121 –
144.
Carlos-Mancilla, M., Lpez-Mellado, E., and Siller, M.
(2016). Wireless Sensor Networks Formation: Ap-
proaches and Techniques. Journal of Sensors,
2016(2016):1 – 18.
Ceclio, J. and Furtado, P. (2014). Wireless Sensors in Het-
erogeneous Networked Systems, chapter Wireless Sen-
sor Networks: Concepts and Components, pages 5 –
25. Springer.
Deshpande, N., Shaligram, A. D., Botre, B. A., Bindal, S.,
and Sadistap, S. . (2010). Embedded E-nose Appli-
cation to Sense the Food Grain Storage Condition. In
Proceedings of International Conference of Compu-
tational Intelligence and Communication Networks,
pages 608 – 611.
Fan, G. J. and Jin, S. (2010). Coverage Problem in Wire-
less Sensor Network: A Survey. Journal of Networks,
5(9):1033 – 1040.
Hadjidj, A., Souil, M., Bouabdallah, A., Challal, Y., and
Owen, H. (2013). Wireless sensor networks for re-
habilitation applications: Challenges and opportuni-
ties. Journal of Network and Computer Applications,
36(1):01 – 15.
Hellevang, K. J. (2010). Grain drying. NDSU Extension
Service, Fargo, ND (1994).
Hong, Z., Wang, R., and Li, X. (2016). A Clustering-
tree Topology Control Based on the Energy Fore-
cast for Heterogeneous Wireless Sensor Networks.
68 IEEE/CAA JOURNAL OF AUTOMATICA SINICA,
3(1):68 – 77.
Hu, F. (2013). Tele-Healthcare Computing and Engineer-
ing: Principles and Design , chapter Hardware: Sen-
sor Mote Architecture and Design. SCIENCE PUB-
LISHERS, CRC Press.
Manay, N. and M.Shadaksharaswamy (2008). Foods Facts
and Principles. New Age International, 3rd edition.
Mishra, A. K. and Samantara, M. K. (2016). A dynamic
energy-efficient chain formation scheme for PEGA-
SIS in wireless sensor networks. In Proceedings of
2nd International Conference on Computational In-
telligence & Networks, CINE 2016, pages 41 – 46.
Puthal, D., Malik, N., Mohanty, S. P., Kougianos, E., and
Yang, C. (2018). The blockchain as a decentralized se-
curity framework. IEEE Consumer Electronics Mag-
azine, 7(2):18–21.
Roy, S. S., Puthal, D., Sharma, S., Mohanty, S. P., and
Zomaya, A. Y. (2018). Building a sustainable internet
of things: Energy-efficient routing using low-power
sensors will meet the need. IEEE Consumer Electron-
ics Magazine, 7(2):42–49.
Sahoo, B., Rath, S., and Puthal, D. (2012). Energy efficient
protocols for wireless sensor networks: A survey and
approach. International Journal of Computer Appli-
cations, 44(18):43–48.
Sawant, A., Patil, S. C., Kalse, S. B., and Thakor, N. J.
(2012). Effect of temperature, relative humidity and
moisture content on germination percentage of wheat
stored in different storage structures. AgricEngInt:
CIGR Journal, 14(2):01 – 14.
Sharma, S., Puthal, D., Jena, S. K., Zomaya, A. Y., and
Ranjan, R. (2017a). Rendezvous based routing pro-
tocol for wireless sensor networks with mobile sink.
The Journal of Supercomputing, 73(3):1168–1188.
Sharma, S., Puthal, D., Tazeen, S., Prasad, M., and Zomaya,
A. Y. (2017b). Msgr: A mode-switched grid-based
sustainable routing protocol for wireless sensor net-
works. IEEE Access, 5:19864–19875.
Tanwar, S., Kumar, N., and Rodrigues, J. J. (2015). A
systematic review on heterogeneous routing protocols
for wireless sensor network. Journal of Network and
Computer Applications, 53(0):39 – 56.
Tripathy, A. K., kumar Mishra, A., Kumar, A., and Das,
T. (2017). A Two-Tailed Chain Topology in Wire-
less Sensor Networks for Efficient Monitoring of
Food Grain Storage. In Proceedings of 5th Interna-
tional Conference on Advanced Computing, Network-
ing, and Informatics (ICACNI).
Yang, C., Puthal, D., Mohanty, S. P., and Kougianos, E.
(2017). Big-sensing-data curation for the cloud is
coming: A promise of scalable cloud-data-center mit-
igation for next-generation iot and wireless sensor
networks. IEEE Consumer Electronics Magazine,
6(4):48–56.
Yu, Z., Teng, J., Bai, X., Xuan, D., and Jia, W. (2011). Con-
nected coverage in wireless networks with directional
antennas. In Proceedings of IEEE INFOCOM, pages
2264–2272.
Zin, S. M., Anuar, N. B., Kiah, M. L. M., and Pathan,
A.-S. K. (2014). Routing protocol design for se-
cure WSN: Review and open research issues. Journal
of Network and Computer Applications, 41(0):517 –
530.
ICE-B 2018 - International Conference on e-Business
98