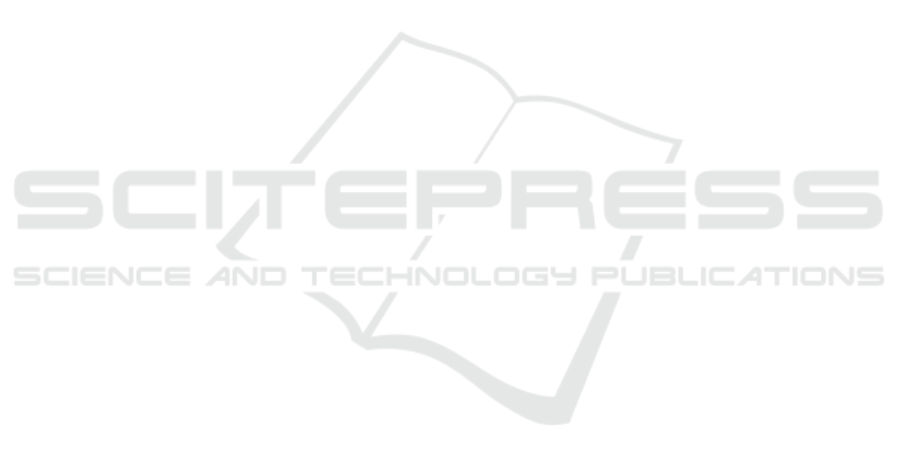
4 CONCLUSIONS
This paper deals with the use of a multistable compli-
ant tensegrity structure for the application in a craw-
ling motion system. Most of the known crawling mo-
tion system allow only a one-way motion or requires
advanced demands to the operating actuator in order
to realize a bidirectional uniaxial motion. In this pa-
per a crawling motion system basing on a multistable
tensegrity structure is modeled. The tensegrity struc-
ture enables multiple stable equilibrium configurati-
ons and is in contact to horizontal plane due to gravity.
As consequence of the acting gravitational forces the
application of certain equilibrium states initiates a til-
ting sequence. Hence, the mode of the entire motion
system is changing. Moreover, total different dynami-
cal properties result for the identical actuation of the
system. Transient simulations are evaluated for se-
lected parameter values of the tensegrity structure and
the steady state solution which assumed after 1000
actuation periods is considered. The motion behavior
which is characterized by the steady state velocity is
analyzed for the different equilibrium configurations
as initial state and diverse friction properties. The re-
sults confirm that a feasible control of the direction
of motion occurs utilizing the given multistability of
the tensegrity structure. At total, these investigations
show that, indeed, a bidirectional uniaxial motion can
be realized by the use of only one actuator with a se-
lected excitation frequency.
However, for a significant parameter range a
change into an additional equilibrium state occurs.
Because of the corresponding low potential energy,
a reverse change into another equilibrium state seems
to be difficult. Hence, after the occurrence of this cri-
tical state the motion system cannot be used anymore.
Therefore, a prototype should be equipped with safe-
guards like mechanical stops which prohibt a change
into that critical equilibrium state.
Moreover, the authors target the development of a
prototype as well as the experimental validation of the
theoretical results shown in this paper.
ACKNOWLEDGEMENTS
This work is supported by the Deutsche Forschungs-
gemeinschaft (DFG project BO4114/2-1).
REFERENCES
B
¨
ohm, V., Sumi, S., Kaufhold, T., et al. (2017). Compli-
ant multistable tensegrity structures. Mechanism and
Machine Theory, 115:130 – 148.
B
¨
ohm, V., Zeidis, I., and Zimmermann, K. (2013). Dyn-
amic analysis of a simple planar tensegrity structure
for the use in vibration driven locomotion systems. In
12th Conference on Dynamical Systems - Theory and
Applications, pages 341–352.
B
¨
ohm, V., Zeidis, I., and Zimmermann, K. (2015). An ap-
proach to the dynamics and control of a planar ten-
segrity structure with application in locomotion sys-
tems. International Journal of Dynamics and Control,
3(1):41–49.
B
¨
ohm, V. and Zimmermann, K. (2013). Vibration-driven
mobile robots based on single actuated tensegrity
structures. In 2013 IEEE International Conference on
Robotics and Automation, pages 5475–5480.
Bolotnik, N., Zeidis, I., Zimmermann, K., et al. (2006). Dy-
namics of controlled motion of vibration-driven sys-
tems. Journal of Computer and Systems Sciences In-
ternational, 45(5):831–840.
Chen, L. H., Kim, K., Tang, E., et al. (2017). Soft spherical
tensegrity robot design using rod-centered actuation
and control. Journal of Mechanisms and Robotics,
9(2):025001–025001–9.
Fang, H.-B. and Xu, J. (2011). Dynamic analysis and op-
timization of a three-phase control mode of a mobile
system with an internal mass. Journal of Vibration
and Control, 17(1):19–26.
Fang, H.-B. and Xu, J. (2012). Controlled motion of a
two-module vibration-driven system induced by inter-
nal acceleration-controlled masses. Archive of Applied
Mechanics, 82(4):461–47.
Hustig-Schultz, D., SunSpiral, V., and Teodorescu, M.
(2016). Morphological design for controlled tense-
grity quadruped locomotion. In 2016 IEEE/RSJ In-
ternational Conference on Intelligent Robots and Sys-
tems (IROS), pages 4714–4719.
Khazanov, M., Jocque, J., and Rieffel, J. (2014). Evolution
of locomotion on a physical tensegrity robot. 14th In-
ternational Conference on the Synthesis and Simula-
tion of Living Systems, pages 232–238.
Kim, K., Chen, L. H., Cera, B., et al. (2016). Hopping and
rolling locomotion with spherical tensegrity robots. In
2016 IEEE/RSJ International Conference on Intelli-
gent Robots and Systems (IROS), pages 4369–4376.
Liu, H., Yu, Y., Sun, P., et al. (2016). Motion analysis of the
four-bar tensegrity robot. In 2016 IEEE International
Conference on Mechatronics and Automation, pages
1483–1488.
Rieffel, J. A., Valer-Cuevas, F. J., and Lipson, H. (2010).
Morphological communication: exploiting coupled
dynamics in a complex mechanical structure to
achieve locomotion. Journal of the Royal Society In-
terface, 7(45):613–621.
Sabelhaus, A. P., Bruce, J., Caluwaerts, K., et al. (2015).
System design and locomotion of superball, an untet-
hered tensegrity robot. In 2015 IEEE International
Conference on Robotics and Automation (ICRA), pa-
ges 2867–2873.
Schorr, P., Sumi, S., B
¨
ohm, V., et al. (2017). Dynamical
investigation of a vibration driven locomotion system
Dynamical Investigation of Crawling Motion System based on a Multistable Tensegrity Structure
129